Share this article:
Key Takeaways from this article
As industries expand, so does the fluctuation in product demand and supply. In periods of economic boom, manufacturers often grapple with surplus inventory, struggling to find adequate storage solutions. Conversely, during downturns, products may languish in warehouses, tying up valuable resources and capital.
These challenges have prompted a strategic pivot among forward-thinking companies towards Just In Time (JIT) delivery, a revolutionary logistics strategy that refines traditional supply chain management.
It involves a precise timing of material and product deliveries to exactly match demand, which helps to eliminate unnecessary stockpiles, reduce waste and maximize efficiency of the project operations.
As we explore its implementation across sectors, you’ll see what profound impact Just In Time has. Let's break down how exactly does Just In Time delivery work in the real world and how does it impact project outcomes across various industries?
The Operational Power of Just In Time
Just In Time delivery is a practical and vital strategy for keeping operations sharp, efficient and responsive. It acts as a linchpin in the strategies across industries, proving that timing really is everything. When properly implemented, it keeps business operations not just running, but excelling.
One thing is to understand Just In Time delivery delivery in theory, another to see it in practice.
Here are a few prominent examples of Just In Time delivery in action employed by business giants, showcasing how adapting just in time principles can lead to significant improvements in efficiency, cost reduction, and operational flow.
Dell Computers Redefines PC Manufacturing with Just In Time
Dell utilized Just In Time delivery to revolutionize the PC manufacturing industry by assembling computers based on customer orders rather than stocking finished goods. This approach allowed Dell to keep inventory costs low and customize products to individual customer requirements, which was a significant competitive advantage during the rapid growth phase in the late 1990s and early 2000s.
McDonald’s Fresh Food Just In Time Service Revolutionizing Fast Food
McDonald's uses a form of Just In Time in its kitchen management, often referred to as "made for you" system. This system began in the late 1990s as a way to make sure that customers receive fresh food while also minimizing waste by preparing products only in response to actual orders.
Harley-Davidson's Leap with Just In Time Implementation
After facing quality and production issues, Harley-Davidson adoptedJust In Time principles to revamp its manufacturing processes in the early 1980s. The implementation of Just In Time helped reduce the production schedule from 1-2 years to just two weeks! and significantly improved product quality and worker productivity.
How Walmart Optimizes Just In Time for Retail Success
Walmart employs a sophisticated Just In Time inventory system in its supply chain management. By optimizing its stock levels and logistics, Walmart can effectively manage its inventory, reduce carrying costs, and pass on the savings to customers with lower prices.
As you see, Just In Time has proven its worth beyond the confines of traditional manufacturing. It's equally transformative in sectors like healthcare, where timely delivery of medical supplies can affect patient care outcomes, and in high tech, where rapid product cycles demand precise inventory management.
Just In Time principles can be indeed applied universally.
Now, let's zoom in on an example from a construction site to see Just-In-Time delivery in action in a more demanding context. A perfect illustration of this is the construction of a notable skyscraper, where every detail counts and timing is everything.
The Shard: A Just In Time Delivery Masterpiece
How they even managed to build that massive glass tower - the tallest in Western Europe at the time of completion in 2012 - right in the heart of London? Remarkably, at the peak of its construction, the project brought together 1,450 workers from 60 different countries.
Just In Time delivery was very important in this project, not by chance but by careful planning. Everything needed, from the 11,000 glass panels to the massive 500-tonne prefabricated steel spire, was timed to arrive exactly when required. Imagine coordinating such precision in a congested urban area with very limited usable space.
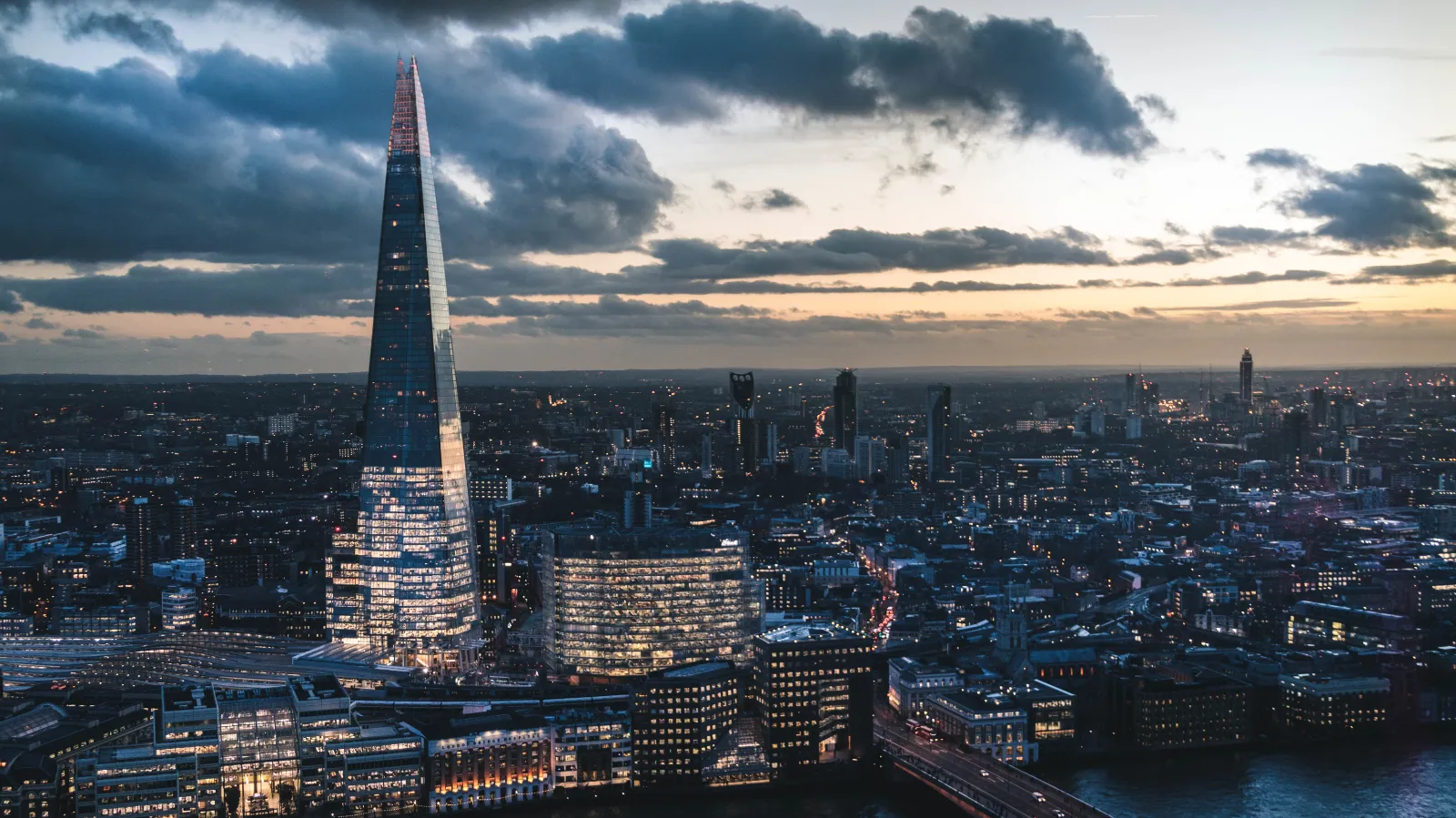
Just In Time on The Shard
- On-the-dot Delivery
JIT delivery secured that each material piece arrived just in the nick of time, effectively minimizing lead times and preventing the need to halt production. No clutter, no chaos—just pure efficiency. This level of supply chain management helped to maintain smoother production flow.
- Cost-Smart
By minimizing on-site storage, Just In Time delivery significantly reduced costs associated with excess inventory and storage facility, helping to keep the project within budget.
- Schedule Sharp
They planned everything down to the minute. This meant no delays and everything moving forward smoothly, even with so many workers hustling around.
This precise inventory management and reliable delivery schedules were vital for maintaining manufacturing timelines and efficiently meeting customer demand. It also guaranteed that each segment of the production process was perfectly synchronized, from the arrival of materials to final assembly.
- Quality at Every Step
Rigorous quality control measures were crucial. Each component had to meet exact standards upon arrival due to the limited time for returns or adjustments. This required trustworthy partners to adhere strictly to delivery commitments.
- Lean Just In Time Practices
The project effectively applied lean principles into JIT delivery strategies, focusing on eliminating waste through streamlined inventory management and optimized logistics. This integration maximized efficiency, directly aligning supply with real-time demand.
- By doing so, the project could maintain high operational flexibility, reduced overhead costs and enhancing overall project agility.
For more detailed information about The Shard and its construction, you can visit the WSP project page.
{{cta}}
The Airbus Just In Time Assembly Line in Europe
Airbus, one of the world's leading aircraft manufacturers, uses Just In Time delivery principles extensively in its assembly lines across Europe. This is particularly evident in the production of the Airbus A380, the largest passenger airliner in the world.
Assembling an aircraft of this magnitude involves complex logistics, given the enormous size of its parts and the necessity for precise coordination with various international suppliers.
Optimizing Airbus Operations with JIT Delivery
- Global Supply Chain Operations
Components such as wings from the UK, fuselage sections from Germany and Spain, and tail sections from France are delivered just in time to assembly facilities. This efficient use of resources showcases the global coordination and efficiency central to Airbus's supply chain management.
This efficient use of resources showcases global coordination. Additionally, it optimizes warehouse space usage by avoiding unnecessary stockpiling of large aircraft components, which significantly reduces inventory costs.
- Coordinated Assembly
The precise timing of component delivery is critical to keep assembly lines running smoothly and without interruption. It optimizes the production flow and reduces turnaround times.
This reliable delivery schedule is vital for maintaining manufacturing timelines and meeting customer demand efficiently. It also secures that each segment of the production process is synced, from the arrival of raw materials to final assembly.
- Inventory Control
By applying Just In Time principles, Airbus manages its inventory with exceptional precision.
It effectively lowers storage costs and maintains minimal inventory levels, while enhancing the overall lean manufacturing process.
- Quality Control
Stringent quality control measures are in place to guarantee that each component meets Airbus's high standards upon delivery. With no margin for error, any defect could delay the tightly scheduled production timelines.
This necessitates robust quality checks from vetted partners before shipment, an integral part of Airbus's supply chain management strategy. These continuous improvement efforts in quality control are fundamental for maintaining customer satisfaction and adhering to delivery commitments.
- Lean Just in Time Manufacturing
Airbus’s implementation of Just In Time manufacturing principles allows for a highly flexible and optimized production process that can quickly adapt to changing customer demand and market conditions. This responsive approach is key to managing production volumes effectively, avoiding overproduction, and closely aligning with actual market conditions.
It enables substantial cost savings by minimizing excess inventory and reducing storage costs, which supports Airbus’s lean manufacturing goals and enhances overall supply chain efficiency.
This example of Airbus showcases how is Just-In-Time applied in complex, multi-national manufacturing environments.
Wrapping It Up: The Just In Time Mindset
Just In Time Delivery isn't just a strategy; it's a mindset that keeps companies agile and prepared.
By syncing operations closely with actual needs, JIT transforms potential chaos into calm, efficient processes. Isn’t that what every business strives for?
Instead of merely reacting, why not anticipate and prepare?
Just In Time Delivery is a model of operational excellence that your projects, too, can aspire to.
The broad applicability of Just In Time across industries underscores its fundamental role in shaping modern operational strategies, making it the secret sauce for anyone looking to thrive in today’s dynamic economic landscape.
So, how ready are you to integrate JIT into your strategy and see how it revolutionizes your operations?
Take the leap with Lcmd’s intuitive software—designed to optimise every aspect of your construction project. Take your management to the next level and stay on top of things. Making just-in-time delivery possible.
{{cta}}