Share this article:
Key Takeaways from this article
- Lean principles transform both design and construction by focusing on HOW work gets done
- Integration of trade partners from early stages prevents issues rather than solving them later
- Effective tools like Last Planner, Big Room, and Value Stream Mapping enable seamless workflow between design and construction
- Clear communication and structured collaboration create predictable outcomes across construction sites
- The future of building industry lies in systematic integration of lean practices into both design and construction phases
Perfect control over YOUR projects from day 1 and fast delivery at the highest quality? That’s exactly what lean design and construction aims for — it brings more value to projects by optimizing every aspect of construction from the ground up.p.
Lean construction is redefining how you envision, plan, and execute construction projects. You're not just solving problems; you're working together to improve outcomes across the board. The integration of lean thinking from early design through completion creates a systematic approach to project management that allows a seamless flow and maximizes value delivery.
The bottom line? Getting quality work done efficiently. Let's see how lean works in practice across construction sites.
How Lean Construction Revolutionizes Process Design
The construction industry continues to evolve, seeking ways to deliver projects more efficiently.
Lean construction recognizes this challenge and focuses on HOW work gets done. It offers specific methodologies and tools to optimize construction processes.
While project delivery methods like Design-Build tackle WHO manages the process, lean principles work regardless of the chosen delivery approach, systematically eliminating waste and maximizing value throughout the entire project lifecycle.
Traditional vs. Lean Approach in Design and Construction
Traditional construction projects often create artificial barriers between planning and execution teams, leading to:
- Delayed problem detection
- Costly design changes
- Communication barriers
- Resource waste
- Extended project timelines
Lean Design Principles: Maximizing Value from Early Stages of Construction Projects
The integration of lean thinking transforms both design and construction process from the earliest project stages. This systematic approach creates value through three fundamental aspects of lean:
- Value Generation: Everything starts with understanding what customers value from early stages. Clear communication across team members helps map value stream and identify value-adding activities. Through systematic flow, trade partners ensure maximizing stakeholder value throughout delivery.
- Systematic Waste Elimination: Value stream mapping reveals and prevents the eight types of waste. Pull systems replace traditional push approaches, creating continuous flow. Through problem solving, teams achieve productivity gains with fewer resources while maintaining quality standards.
- Process-Driven Continuous Improvement: Lean methodology thrives on feedback loops and constant learning. Teams implement structured problem-solving frameworks that connect design decisions directly to construction outcomes. This creates a cycle of continuous improvement where each phase informs and enhances the next, leading to better project delivery.
Implementing Lean Production Philosophy into Design and Construction Industry
Integration goes beyond simple collaboration. It creates a unified team where trade partners actively shape solutions together. This deeper level of engagement transforms traditional workflows into synchronized delivery systems.
1. Early Team Integration
Trade contractors don't just join early – they become instrumental in decision-making. This means:
- Value stream planning starts immediately
- Clear communication prevents later issues
- Problem solving happens before problems grow
- Lower costs through early coordination
2. Dynamic Work Structuring
Trade partners work based on real site needs:
- Weekly planning with all trade contractors
- Continuous improvement through daily checks
- Productivity gains through direct coordination
- Fewer resources wasted on rework
3. Knowledge Integration
Teams use practical tools for maximizing stakeholder value:
- Daily team member updates
- Problem solving in real time
- Clear communication standards
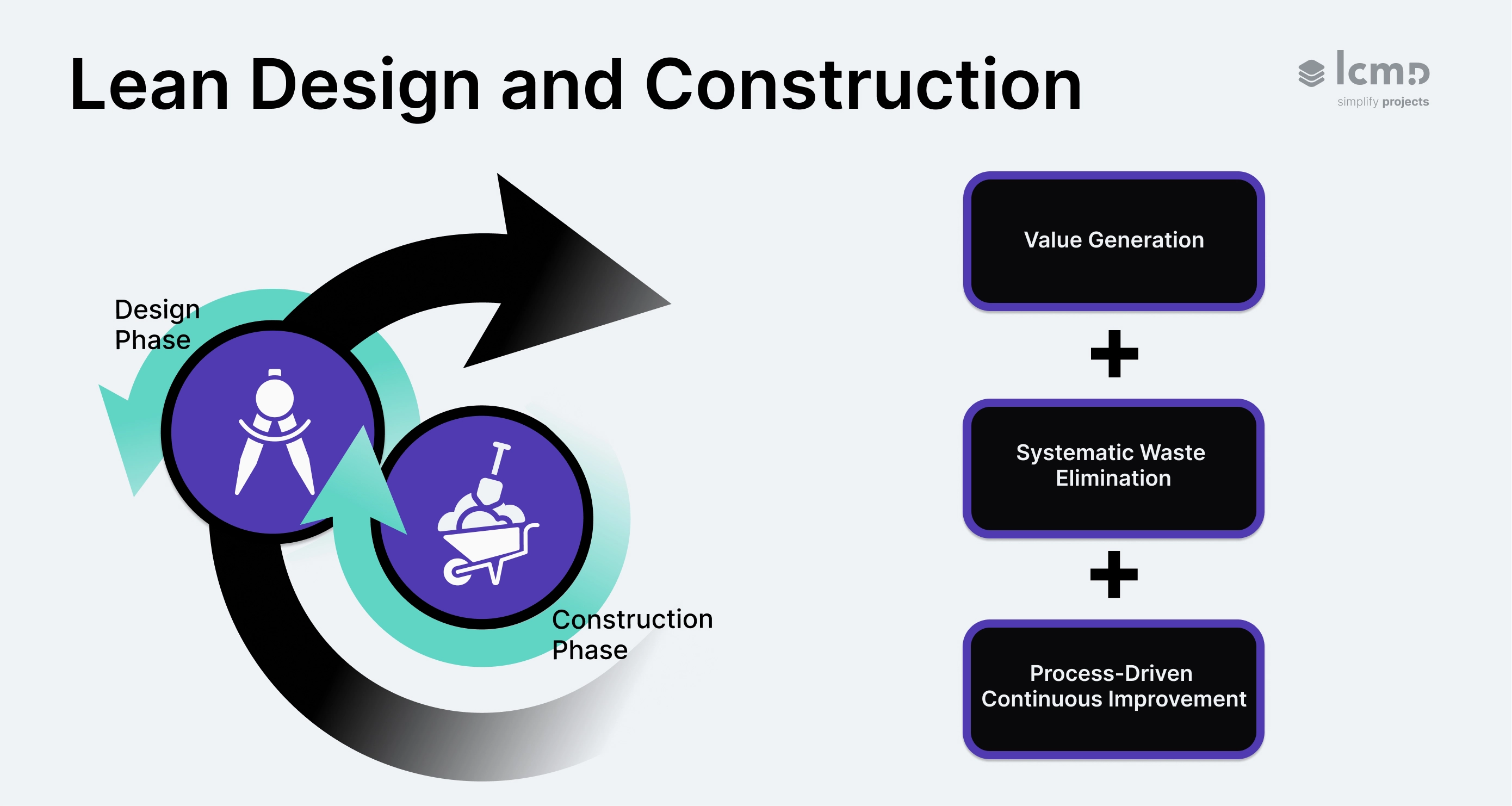
Effective Lean Tools for Design and Construction Success
While integration creates the framework, specific tools make lean project delivery work day to day. Let's explore how teams use proven methods to achieve more value with fewer resources in real projects.
Last Planner System
As the backbone of effective planning, design teams and trade partners coordinate their supply chain needs to establish realistic deliverables. Regular coordination ensures both design development and site work adjust to actual conditions, creating reliable workflows.
This brings:
- Design milestone planning aligned with construction needs
- Early integration of planning and building expertise
- Coordinated decision-making across all phases
- Quality improvements through proactive planning
Beyond scheduling, successful teams need dedicated space for collaboration:
Big Room Collaboration
Whether physical or virtual, these sessions bring designers and builders together for real-time problem solving.
Teams work in one space to:
- Optimize designs with construction input
- Resolve design-construction interfaces quickly
- Review progress across both phases
- Solve complex issues while designs develop
Effective collaboration reveals opportunities for systematic improvement:
Value Stream Mapping
Value stream mapping shows where improvements matter in both design and construction. By understanding how work flows from concept to completion, teams spot waste in both processes.
This helps:
- Streamline design development and construction
- Optimize design-to-construction handoffs
- Create smoother flow between phases
- Continuous improvement opportunities in both design and building processes
Modern technology amplifies the power of these collaborative practices:
Digital Integration Tools
Building Information Modeling (BIM) and specialized lean construction software help teams coordinate complex work in real time.
These tools transform how teams detect and solve issues by enabling:
- Virtual design validation with builders' input
- Real-time coordination of design changes
- Seamless design-to-field information flow
- Integrated progress tracking across phases
{{cta}}
Lean Practices Transform Future Projects in Design and Construction Industry
Lean principles transform HOW we work, regardless of project delivery method. It reshapes construction work flow, making projects more predictable from design through completion.
It's about changing how construction teams work together to create value at every step, using proven tools and methods to work as one.
Last Planner aligns everyone's work, while Big Room sessions help eliminate waste through collaborative problem-solving. Value Stream Mapping reveals opportunities for more value that traditional approaches miss. This is when lean mindset shows its true power and creates better project outcomes.
The lean tools and methods we've explored aren't tied to any particular contract structure - they're guiding principles for better integration into both design and construction phases. This is how our industry evolves, creating better buildings more efficiently.