Share this article:
Key Takeaways from this article
- Supply chain management creates competitive advantage by connecting all steps from raw materials to customer delivery
- The five essential components—plan, source, make, deliver, and return—form a comprehensive framework for managing the entire supply chain
- Effective supply chain operations require both data-driven decision making and real-time monitoring to prevent disruptions before they cascade
- Just-in-Time methodology reduces waste and costs in predictable environments, while agile approaches offer flexibility for changing markets
- Construction companies face unique supply chain challenges that require specialized digital tools like those provided by Lcmd
- Companies that view supply chains as strategic assets rather than just operational functions gain significant market advantages
Your supply chain is only as strong as its weakest link - and that link determines your competitive edge.
Every product starts with raw materials, but success depends on how seamlessly each step is connected. Supply chain management isn’t just about moving parts—it’s about building a system that delivers goods with precision, adaptability, and cost-efficiency.
Businesses that master this process don’t just keep operations running—they turn supply chains into a competitive advantage. So, how do you make it work for you? Let’s break it down.
All About Supply Chain Management: Core Concepts
A product doesn’t just appear on a shelf. Behind every finished item lies a network of decisions, movements, and precise coordination - supply chain management.
At its core, supply chain management (scm) coordinates all activities involved in producing and delivering products or services, from raw materials to finished products reaching the end consumer.
It's the force that assures the right products arrive
- at the right place,
- at the right time,
- in the right condition and
- at the right cost.
A well-run supply chain network minimizes disruptions, reduces waste, and helps businesses meet demand while keeping costs under control.
What Is the Definition of Supply Chain Management in Today's Business Landscape
Traditionally, supply chain management focused on moving raw materials through manufacturing processes to produce finished goods. Today, it's far more complex. Businesses must balance demand forecasting, inventory management, and logistics planning - all while navigating global supply chains, economic uncertainty, and ever-changing customer needs.
Supply chain management today is not just logistics - it’s a strategic function shaping profitability and customer experience. Today's supply chain is an integrated network of suppliers, manufacturers, warehouses, distribution centers, and retailers connected through both physical product flows and digital information flows.
The Difference Between Supply Chain and Supply Chain Management
Before diving deeper, let's distinguish between two often confused terms:
- The supply chain includes all organizations, resources, activities, and technology involved in creating and delivering a product. It is the network itself.
- Supply chain management is the strategic coordination of these supply chain activities to maximize value and gain competitive advantage.
For illustration: If the supply chain is a highway, then supply chain management is the traffic control system that keeps everything flowing efficiently.
How Does Supply Chain Management Work: SCM Processes
You order a smartphone. Behind that simple action, a global supply network moves in perfect sync - raw materials are sourced, production is scheduled, and logistics ensure timely delivery.
Each step in the process follows five key supply chain components:
- Plan: The company forecasts customer demand, determines production schedules, and optimizes inventory levelsto prevent shortages or overstocking.
- Source: Manufacturers secure raw materials like lithium for batteries and silicon for chips, ensuring reliable and ethical sourcing.
- Make: These materials transform into finished products across various facilities, forming a key part of the supply chain management concept.
- Deliver: Logistics providers handle warehouse management, distribution, and transportation, ensuring timely and cost-effective delivery.
- Return: When necessary, businesses manage customer returns, repairs, and recycling to maintain sustainability and customer satisfaction.
Now, what happens when something goes wrong? ...Like a sudden shortage of lithium from a key supplier. Production slows, leading to delays in manufacturing and unfulfilled orders. Logistics bottlenecks further increase transportation costs, and dissatisfied customers start looking elsewhere.
This is why organizations prioritize effective supply chain management. A single weak link can disrupt an entire supply chain, but a well-executed strategy connects all five key components into a resilient, high-performing system.
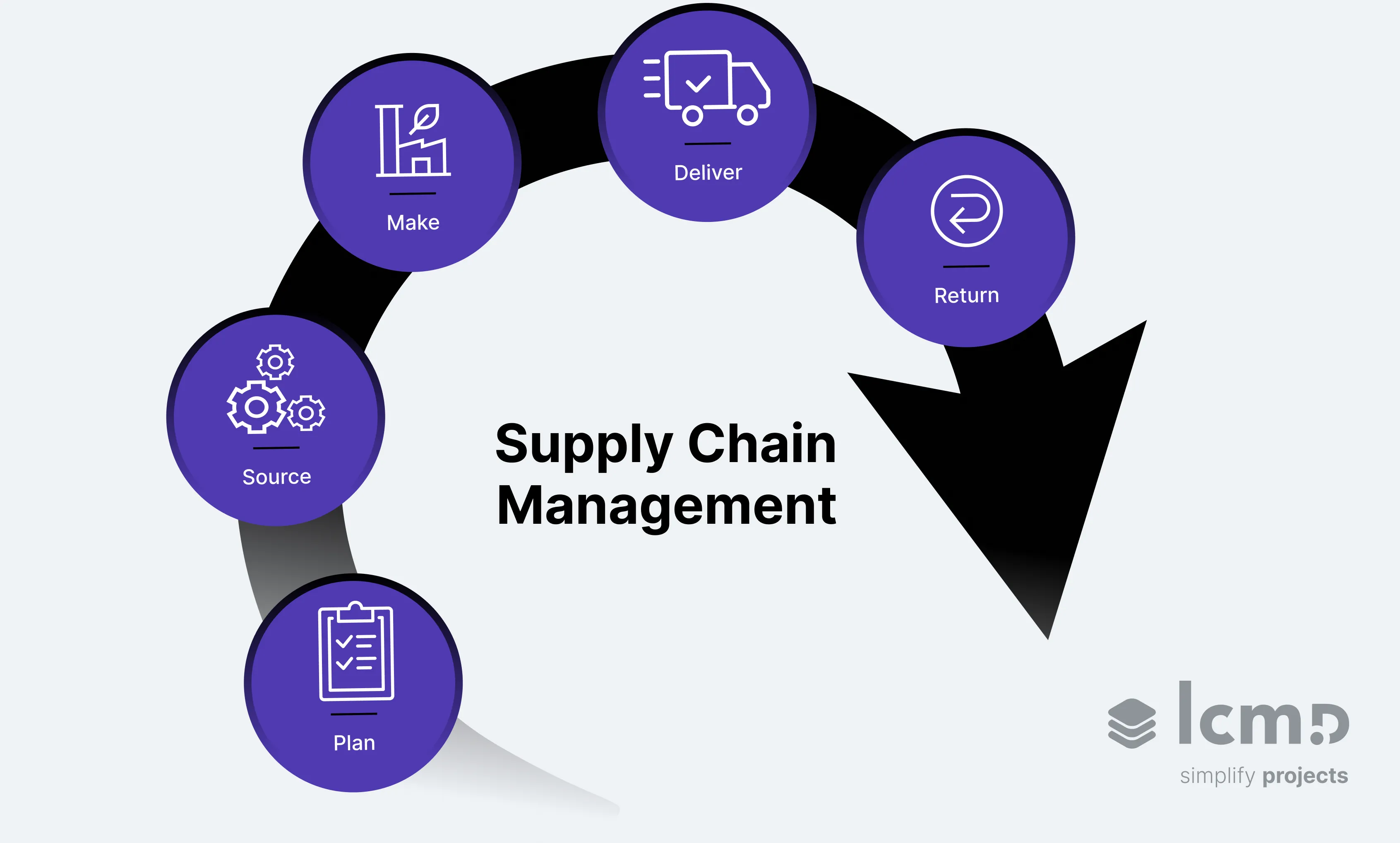
5 Essential Components Supply Chain Management
Plan, source, make, deliver, and return are the five basic supply chain management components. This framework, sometimes called the Supply Chain Operations Reference (SCOR) model, provides a comprehensive view of the entire process.
Let’s break it down and see how each component contributes to a well-functioning supply chain network.
1. Plan: Setting the Foundation
Every strong supply chain starts with a solid plan. Businesses must forecast customer demand, map out logistics planning, and align supply chain processes with business strategy.
A well-structured supply chain network requires:
- Demand forecasting – Predicting what customers need before they do.
- Inventory management – Balancing stock levels to avoid shortages or overflows.
- Risk management – Preparing for supply disruptions, delays, or market shifts.
Without proper planning, businesses risk overproduction (tying up capital in excess inventory) or underproduction (missing sales opportunities and disappointing customers). A well-planned supply chain network means fewer surprises and greater overall productivity.
2. Source: Securing the Right Materials
Without raw materials, there's no product. Sourcing is about securing the right supply chain partners to provide high-quality materials and services on time and at the right cost.
Modern supply chain sourcing isn’t just about cutting costs - it’s about building resilience and sustainability and encompasses:
- Supplier evaluation and selection
- Contract negotiation
- Quality control management
- Integrating suppliers into the business processes
Companies leverage enterprise resource planning systems to track suppliers, manage contracts, and keep operations running smoothly. For example, a car manufacturer needs consistent access to thousands of components. A delay in one finished good can halt production, making sourcing one of the most critical supply chain functions.
3. Make: Production and Manufacturing Processes
With sourcing complete, we reach the transformation stage of the supply chain. Here, manufacturing processes convert raw materials into finished products that satisfy market demands.
A well-optimized supply chain management approach ensures:
- Efficient inventory planning – No wasted stock, no missing parts.
- Smooth operations management – Production lines function without bottlenecks.
- Automated processes – Integrating cutting-edge technologies like AI-driven manufacturing.
From mass production to custom-built solutions, how businesses manage this stage defines their success and ability to meet demand.
4. Deliver: Logistics and Distribution Management
The deliver component bridges the gap between production and consumption. While logistics providers, distribution centers, and warehouse management form the backbone of this stage, the true measure of success is the customer experience. Properly executed, this component moves products efficiently but also delivers goods in ways that build customer loyalty.
Effective delivery systems focus on:
- Optimizing worldwide logistics – Coordinating international shipping, customs, and regional transportation networks.
- Logistics planning – Optimizing routes and carrier selection to reduce costs and minimize delays.
- Meeting customer needs – Creating flexible delivery options that drive higher customer satisfaction.
The delivery component often represents the most visible part of the supply chain to end customers. Efficient systems help businesses meet demand while minimizing transportation costs and environmental impact.
5. Return: Managing Product Recovery and Reverse Flow
Not everything moves forward in a supply chain. Sometimes, products need to come back. Whether it’s returns, repairs, or recycling, reverse supply chain processes are a critical part of operations.
Strategic return management includes:
- Processing customer returns efficiently through proper inventory control
- Recycling and reducing waste to support sustainability and creating net value
- Capturing data from returns to improve quality and future supply chain processes
In many industries, effective reverse supply chain processes have become a competitive edge not just by reducing costs, but by creating value. Companies that optimize customer returns can recover assets, enable refurbishment or resale, and enhance brand loyalty, turning a challenge into a business opportunity.
Supply Chain Management Operations in Action
A supply chain is more than a series of steps - it’s a living operation that reacts to every decision, from sourcing materials to delivering the final product. When managed well, supply chains stay agile, reducing costs and meeting demand. But when disruptions hit, even small setbacks can trigger delays, financial strain, and lost customer trust.
This chapter explores how effective supply chain management works in practice, what exactely can drive efficiency and what could cause breakdowns.
A Day in the Life of Supply Chain Managers
Imagine starting the day with a dashboard overview: inventory levels, supplier updates, shipment tracking. Everything looks stable, but an unexpected disruption is always just one notification away.
A supplier delay in China, a logistics bottleneck at a major port, or a sudden spike in demand - each issue requires immediate action to keep the supply chain from breaking down.
On any given day, supply chain professionals are:
- Coordinating with suppliers to confirm raw material availability.
- Adjusting inventory planning based on fluctuating customer demand.
- Troubleshooting transportation delays to ensure on-time delivery.
- Communicating with logistics providers to re-route shipments when necessary.
- Monitoring warehouse management systems for real-time stock levels.
Supply chain operations are dynamic and complex, requiring quick thinking, strong communication, and technology-driven insights to maintain efficiency.
The Impact of a Well-Optimized Supply Chain
When a supply chain network functions as intended, products move seamlessly from raw materials to finished goods, reaching customers
- on time,
- at the right cost,
- and with minimal waste.
The best supply chains are not just efficient—they are resilient, flexible, and scalable.
How Strong Supply Chains Drive Business Success
Amazon: The Benchmark for Supply Chain Management Efficiency
Amazon’s predictive analytics, robotics-driven warehouses, and global logistics network allow it to process millions of orders daily while keeping inventory levels optimized. Its real-time demand forecasting and automated fulfillment centers ensure higher customer satisfaction with rapid, accurate deliveries.
Zara: Fast Fashion, Faster Supply Chain
Zara has built an agile supply chain model that can bring new fashion designs from concept to store shelves in just a few weeks. By producing in smaller batches, Zara reduces inventory risks, avoids overproduction, and maintains a competitive infrastructure that keeps products fresh and in demand.
Toyota: Mastering Lean Supply Chain Management
Toyota’s Just-in-Time (JIT) production system relies on the precise delivery of materials, eliminating excess inventory and reducing waste. This lean supply chain management approach allows Toyota to increase efficiency while maintaining quality and minimizing costs.
The Cost of Supply Chain Failures
A weak or disrupted supply chain process can result in product shortages, financial losses, and damaged reputations. The following cases illustrate how supply chain failures can ripple across industries.
Major Supply Chain Disruptions and What They Revealed
The 2021 Global Chip Shortage: A Crisis Across Industries
A severe semiconductor shortage caused production halts in automotive, electronics, and tech industries, exposing the dangers of over-reliance on a few key suppliers. Without a robust risk management plan, major companies were left scrambling for alternatives, leading to delays, price increases, and lost market opportunities.
Ever Given: When a Single Ship Blocks the World
In March 2021, the Ever Given container ship blocked the Suez Canal for six days, causing a global supply chain disruption. With 12% of world trade passing through this crucial route, the backlog delayed billions of dollars worth of goods, illustrating the fragility of worldwide logistics and the importance of contingency planning.
Berlin Brandenburg Airport: A Construction Supply Chain Disaster
The Berlin Brandenburg Airport (BER) project, originally set to open in 2011, faced severe supply chain failures that delayed its completion by nearly a decade. Poor supplier coordination, critical material shortages, and repeated human errors led to safety violations, forcing costly redesigns. The entire supply chain breakdown resulted in billions in overruns, proving how fragile construction supply chains can be without proper risk management.
What Smart Companies Learn from Supply Chain Crises
What separates a resilient supply chain from one that collapses under pressure? These lessons apply across industries:
- Data-Driven Decision-Making is Crucial
Companies like Amazon and Toyota use real-time data and AI-driven insights to make proactive supply chain decisions. Measuring performance globally allows businesses to detect inefficiencies and reduce costs before problems escalate. - Supplier Diversification Reduces Risk
Over-reliance on a single supplier or region makes businesses vulnerable. The global chip shortage taught companies that having backup suppliers and flexible sourcing strategies is non-negotiable. - Agility Matters More Than Ever
The ability to quickly adapt to market shifts, supply chain disruptions, and customer needs is a defining factor of supply chain success. Whether through lean supply chain management or advanced logistics planning, companies that remain flexible have the competitive advantage. - Technology is No Longer Optional
From automated processes to machine learning-driven forecasting, digital transformation is shaping the future of supply chain operations. Businesses that invest in cutting-edge technologies can improve efficiency, scalability, and resilience.
The strongest supply chains don’t just react to disruptions. They build agility into their processes. Companies like Toyota have proven that lean supply chain management can minimize waste, improve inventory planning, and optimize supplier relationships.
Up next, we explore one of the most influential methodologies reshaping how businesses operate.
Just-in-Time Supply Chain Management
Toyota's pioneering approach to production efficiency has evolved into a comprehensive strategy adopted worldwide. Just-in-Time (JIT) supply chain management stands out as a methodology that reduces waste, integrates suppliers efficiently, and optimizes inventory planning.
By aligning production closely with demand, Just-in-Time transforms business functions, making supply chains leaner, more responsive, and more cost-effective.
What Is Just-in-Time Supply Chain Management
Just-in-Time (JIT) supply chain management is a strategy built on precision - materials and components arrive exactly when needed, eliminating excess stock and reducing waste. This lean approach prevents companies from tying up capital in unnecessary inventory.
Key Characteristics of JIT Supply Chains:
- Demand-driven inventory – Companies order materials only as needed, preventing excess stock.
- Strong supplier relationships – Close coordination with suppliers supports rapid delivery.
- Efficient production cycles – Manufacturers produce goods in response to customer demand, not forecasts.
- Reduced storage requirements – Minimal warehouse space is needed, cutting costs.
Just-in-Time requires precise coordination across the entire supply chain, making SCM processes more agile and responsive. For a more detailed exploration see our in-depth article Optimizing Supply Chain Efficiency with Just-in-Time Delivery.
Lean vs. Agile Supply Chain Management
Just-in-Time is a core principle of lean supply chain management because both approaches share a fundamental goal: eliminating waste. Lean supply chain management focuses on reducing inefficiencies in production, inventory, and resource use, that every component in the supply chain adds value.
However, lean supply chains work best when demand is stable. In industries where demand fluctuates or disruptions are frequent, agile supply chain management offers an alternative, prioritizing flexibility and rapid adaptation.
Lean, Agile, or Both? Choosing the Right Supply Chain Model
While some industries benefit from a pure lean or agile approach, many companies blend elements of both to balance efficiency and adaptability.
For example:
- Automotive manufacturers rely on lean Just-in-Time systems to minimize inventory costs and optimize production.
- Fashion retailers operating in fast-changing markets often prefer agile supply chains to quickly adapt to shifting demand.
Most businesses require a mix of stability and flexibility. A hybrid approach allows companies to apply lean efficiency where predictability exists while incorporating agility to handle shifting demand.
At the heart of this balance is the decoupling point - the stage in the supply chain where products shift from standardized to customized. Before this point, lean principles dominate; after it, agility takes over to meet dynamic customer needs.
Industry Focus: Just-in-Time Supply Chain Management in Construction
The construction industry presents unique challenges for Just-in-Time supply chain management. Unlike manufacturing, where lean supply chains thrive due to predictable workflows, construction demands a more flexible approach. Projects are influenced by weather, site conditions, and shifting schedules, making a hybrid model that blends efficiency with adaptability the most effective solution.
For Just-in-Time to work in construction, supply chains must integrate materials, labor, and logistics seamlessly—reducing waste and avoiding costly disruptions.
Key Factors for Successful Just-in-Time Implementation in Construction
- Demand planning that anticipates project phases
- Supplier integration with reliable, on-time deliveries
- Inventory management that balances immediate needs with buffer stock
- Digital tools that provide real-time supply chain visibility
When properly implemented, Just-in-Time principles help construction companies reduce on-site congestion, minimize material waste, decrease storage costs, and improve project cash flow - transforming how projects operate from start to finish.
How Lcmd Supports Just-in-Time in Construction
While Just-in-Time is a staple in manufacturing, construction firms are adopting it to optimize material use, scheduling, and collaboration. Lcmd construction management software simplifies this process by:
- Managing inventory in real-time to prevent material shortages.
- Optimizing workflows with predictive analytics and scheduling tools.
- Integrating suppliers seamlessly into project timelines.
- Supporting the Last Planner System for clear communication and coordination.
- Providing digital oversight to keep all stakeholders aligned.
With Lcmd, construction firms can implement Just-in-Time strategies to enhance efficiency, lower costs, and optimize resource utilization. Its takt planning capabilities create flow-oriented schedules with a single click, ensuring seamless trade progression.
Lcmd empowers construction teams to apply Just-in-Time principles with confidence, keeping projects on track without unnecessary waste or costly delays.
Conclusion: The Strategic Power of Supply Chain Management
A well-executed supply chain goes beyond logistics—it drives business resilience, efficiency, and long-term competitive growth. While individual supply chain components matter, their real strength lies in seamless integration. The importance of SCM processes extends beyond cost-cutting; they shape adaptability, innovation, and long-term market leadership.
Companies that optimize their key components don’t just reduce waste or improve efficiency - they gain the flexibility to navigate disruptions and respond to demand shifts with precision. In a world where supply chains are no longer just logistical networks but strategic assets, the future belongs to organizations that continuously refine their systems, embrace digital transformation, and turn operational excellence into a growth engine.
FAQ on Supply Chain Management
What is a primary focus of supply chain management (SCM)?
The primary focus of supply chain management (SCM) is optimizing the flow of goods, services, and information from supplier to customer to provide maximum value at minimum cost. While cost control is important, leading organizations recognize that customer satisfaction is the ultimate goal, with the right balance of efficiency, responsiveness, and quality.
How do supply chain management operations differ from logistics?
Logistics is one component of the broader supply chain management field. While logistics focuses specifically on the movement and storage of goods, supply chain management encompasses the entire process from planning and sourcing through manufacturing and delivery. Logistics answers "how do we get products from A to B efficiently?" while supply chain management addresses the broader question, "how do we create and deliver value throughout the entire network?"
What skills do modern supply chain managers need?
Today's supply chain managers require a diverse skill set:
- Analytical thinking: Ability to interpret data and identify improvement opportunities
- Technology savvy: Familiarity with digital tools and emerging technologies
- Communication: Clear articulation of complex concepts to diverse stakeholders
- Relationship management: Building productive partnerships with suppliers and customers
- Problem-solving: Quick resolution of inevitable supply chain disruptions
- Strategic thinking: Aligning supply chain initiatives with business goals
- Change management: Leading teams through process and technology transitions
This combination of technical knowledge, business acumen, and interpersonal skills makes supply chain management a challenging but rewarding career.
What are the biggest challenges in supply chain management today?
Modern supply chains face several critical challenges:
- Supply chain visibility – Gaining end-to-end transparency across complex networks
- Risk management – Building resilience against disruptions (geopolitical, weather, supplier failures)
- Sustainability pressures – Meeting environmental and social responsibility demands
- Talent shortages – Finding skilled professionals in a competitive labor market
- Technology integration – Implementing and connecting digital solutions effectively
- Balancing efficiency and resilience – Optimizing costs while maintaining flexibility
How does technology improve supply chain management?
Modern supply chain management relies on AI-driven forecasting, real-time inventory tracking, and automation to enhance efficiency. Digital tools help companies predict demand, optimize delivery routes, and reduce costs while improving overall supply chain visibility.