Teile diesen Beitrag:
Die wichtigsten Erkenntnisse aus diesem Artikel:
Die Implementierung von 5S bei GE hat nicht nur unsere Fabrikhallen, sondern unsere gesamte betriebliche Ethik verändert, indem sie auf allen Ebenen Effizienz steigerte und Verschwendung reduzierte.
Jack Welch, ehemaliger CEO von General Electric
Die 5S-Methode, die ihren Ursprung im Toyota-Produktionssystem hat, ist ein systematischer Ansatz. Sie wurde entwickelt, um die Effizienz und Sicherheit am Arbeitsplatz durch die Organisation der Arbeitsumgebung zu verbessern.
Im Kern geht es darum, einen Arbeitsbereich zu schaffen, in dem alles seinen Platz hat und alles immer an seinem Platz steht.
Indem man die fünf Prinzipien – Sortieren (Seiri), Systematisieren (Seiton), Säubern (Seiso), Standardisieren (Seiketsu) und Selbstdisziplin (Shitsuke) – befolgt, beseitigt man unnötigen Ballast und optimiert tägliche Aufgaben.
Das Ergebnis? Ein sauberer Arbeitsplatz ohne verschwendeten Raum, an dem visuelle Kontrolle aufrechterhalten wird, um die Qualität kontinuierlich zu verbessern.
Was bedeutet 5S?
Die 5S-Methode ist ein umfassendes Konzept, das für Lean Management von entscheidender Bedeutung ist, hauptsächlich weil es eng mit dem Hauptziel des Lean-Ansatzes verbunden ist - der Eliminierung von Verschwendung. Diese Methode findet breite Anwendung in verschiedenen Bereichen, z.B. Lean Manufacturing oder Lean Construction.
Die 5S-Methode zielt zwar nicht unmittelbar auf alle acht im Lean-Konzept definierten Verschwendungsarten ab, beeinflusst aber dennoch mehrere davon maßgeblich.
Indem alles an seinem richtigen Platz gehalten und sichergestellt wird, dass der Arbeitsbereich sauber und standardisiert ist, reduziert 5S Verzögerungen, Fehler und unnötige Arbeit. Dies steigert nicht nur die Produktivität, sondern hält auch alles sicher und ordentlich.
Das 5S-System dreht sich um fünf Schlüsselphasen:
- Sortieren (Seiri)
- Systematisieren (Seiton)
- Säubern (Seiso)
- Standardisieren (Seiketsu)
- Selbstdisziplin (Shitsuke)
Mit standardisierten Arbeitspraktiken aus 5S bleibt jeder Teil des Arbeitsplatzes effizient. Und wissen Sie was? Dieses System ist ein fester Bestandteil vieler Produktivitätsinitiativen weltweit, wie bei Boeing, Ford oder dem bereits erwähnten Toyota.
Vorteile des 5S-Systems
Die Implementierung des 5S-Systems bietet mehrere wichtige Vorteile, die die Effizienz steigern und einen hohen Standard der Arbeitsabläufe am Arbeitsplatz aufrechterhalten.
Zahlreiche Studien in verschiedenen Branchen wie der Automobilindustrie dem Gesundheits- und dem Bauwesen belegen dies und zeigen positive Korrelationen zwischen 5S und verbesserter Leistung. Detaillierte Einblicke finden Sie in den umfassenden Fallstudien, die in folgenden Ressourcen bereitgestellt werden: Studie zur Automobilkabelproduktion, 5S-Fallstudien und Lean-Management-Implementierungen.
Hier eine Aufschlüsselung der Vorteile, die 5S liefert:
- Macht Arbeitsprozesse effizienter
- Fördert kontinuierliche Verbesserung am Arbeitsplatz
- Reduziert Zeitverschwendung und unnötige Bewegungen
- Verringert das Risiko von Geräteausfällen und erhöht die allgemeine Sicherheit
- Fördert visuelle Hinweise für allgemeine Sauberkeit
- Schafft eine besser organisierte, produktivere und abfalleffizientere Arbeitsumgebung
Wie genau kann 5S also Ihren Arbeitsplatz transformieren?
Laden Sie unsere kostenlose 5S-Checkliste herunter
Bevor Sie mit Ihrer 5S-Reise beginnen, empfehlen wir Ihnen dringend, unsere kostenlose 5S-Checkliste herunterzuladen. Dieses umfassende Tool hilft Ihnen, während des gesamten Prozesses organisiert und fokussiert zu bleiben. Unsere XLSX-Datei enthält integrierte Berechnungen, mit denen Sie Ihren Fortschritt in jeder Phase der 5S-Methodik einfach verfolgen können.
So funktioniert es:
- Bewerten Sie jedes Element der Checkliste mit einem Wert von 1 bis 5, wobei 5 die bestmögliche Bewertung darstellt.
- Streben Sie einen Durchschnittswert von 4 (80% Gesamt-5S-Score) über alle Elemente an, um Ihren 5S-Prozess als erfolgreich umgesetzt zu betrachten.
- Denken Sie daran: Gemäß dem Kaizen-Prinzip der kontinuierlichen Verbesserung gibt es immer Raum für Wachstum. Streben Sie nach dem idealen 100%-Score!
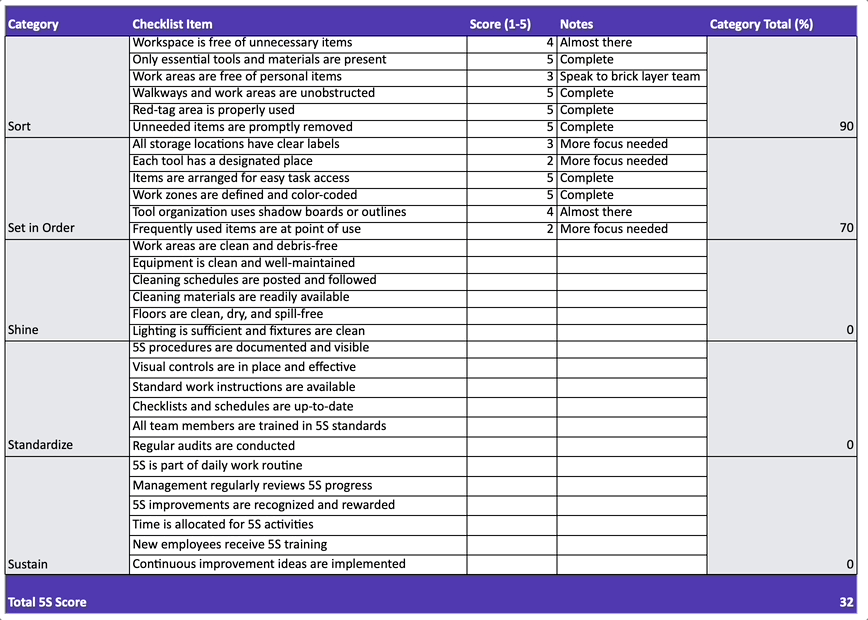
Ob Sie 5S auf einer Baustelle oder in einem Lager implementieren, ein 5S-Audit durchführen oder eine maßgeschneiderte 5S-Reinigungscheckliste erstellen möchten - unsere 5S-Checkliste als Excel-Vorlage oder PDF bietet eine solide Grundlage. Sie ist perfekt für Anfänger und erfahrene Anwender, die ihren 5S-Ansatz verfeinern möchten.
{{asset}}
1. SCHRITT: Sortieren (Seiri)
Die Rolle des Sortierens in der Arbeitsplatzorganisation
Sortieren ist der erste Schritt in der 5S-Methodik, bei dem Sie alle Gegenstände in der Arbeitsumgebung kategorisieren.
Das Hauptziel besteht darin, überfüllte Räume und unnötige Gegenstände aus dem Arbeitsbereich zu entfernen, um die Anhäufung von Gegenständen zu verhindern, die für die unmittelbare Arbeit nicht erforderlich sind und die Arbeitsprozesse verlangsamen können.
Warum Sortieren in 5S wichtig ist
Indem Sie nur das Notwendige behalten, optimieren Sie die Abläufe und reduzieren die Zeit, die für die Suche nach Gegenständen aufgewendet wird. Dies verbessert auch die visuelle Kommunikation und erleichtert es den Teammitgliedern, Arbeitsabläufe schnell zu verstehen und notwendige Werkzeuge ohne Verwirrung zu finden.
Sortierstrategien im 5S-Programm
- Kategorisieren:
Gruppieren Sie Gegenstände in Kategorien wie "wesentlich", "nicht wesentlich" und "unsicher", um zu bestimmen, was behalten, gelagert oder entsorgt werden sollte. - Rotes-Etikett-System:
Implementieren Sie ein Rotes-Etikett-System, um Gegenstände zu markieren, die vor der Entsorgung oder Verlagerung weiter bewertet werden müssen. Effektiv organisierte rot markierte Gegenstände und optimierte Werkzeugaufbewahrung machen klar, welche Gegenstände zu behalten und welche zu entfernen sind. - Digitales Sortieren:
Berücksichtigen Sie digitales Sortieren, indem Sie Dateien und Ordner auf Ihrem Computer organisieren. Löschen Sie veraltete Dateien und ordnen Sie die verbleibenden digitalen Elemente in strukturierte Ordner ein, genau wie bei physischen Gegenständen. - Visuelle Managementtools:
Organisieren Sie physische Werkzeuge und Ausrüstung mithilfe visueller Hinweise wie Etiketten, Bodenmarkierungen oder Schattenbretter, damit es für jeden einfacher ist zu erkennen, wohin die Dinge gehören, wenn sie mit dem Aufräumen beginnen.
Schaffung sichererer und effizienterer Baustellen
Im Bausektor ist der Sortierschritt entscheidend für die Aufrechterhaltung eines optimierten und sicheren Arbeitsbereichs. Durch die Bewertung aller Werkzeuge und Ausrüstungen identifizieren und entfernen die Arbeiter unnötige Gegenstände, die veraltet sind oder selten verwendet werden. Verbleibende Gegenstände können sofort entsorgt werden.
Diese Entrümpelung verbessert die Arbeitsplatzeffizienz erheblich, indem sie Platz schafft. So werden unnötige Transporte reduziert und die Notwendigkeit häufiger Abteilungsrundgänge minimiert und damit Sicherheitsrisiken verringert.
Das Ergebnis ist eine besser organisierte Umgebung, in der wesentliche Werkzeuge leicht zugänglich sind, wodurch die Abläufe beschleunigt werden und die Sicherheit auf der Baustelle gewährleistet ist.
2. SCHRITT: Systematisieren (Seiton)
Organisation für Effizienz und Beherrschung des Arbeitsplatzlayouts
Systematisieren (Seiton) baut auf dem Fundament auf, das durch die Sortierphase gelegt wurde. Dieser Schritt, manchmal auch als "Ordnen" bezeichnet, beinhaltet die Anordnung aller notwendigen Gegenstände, sodass sie leicht zugänglich und logisch positioniert sind, um Aufgaben und Arbeitsabläufe zu optimieren.
Warum alles seinen Platz haben sollte
Systematisches Ordnen in 5S ermöglicht die Maximierung des benötigten Raums und unterstützt effiziente Produktionsprozesse.
Es reduziert die Zeit, die Sie mit der Suche nach Dingen verbringen, und verringert Unterbrechungen im Arbeitsablauf. Genau zu wissen, wo sich alles befindet, bedeutet, dass Sie schneller und reibungsloser durch Ihre Aufgaben gehen können. Ist das nicht eine Erleichterung?
Strategien für optimale Organisation in 5S: Jeden Gegenstand zählen lassen
- Kennzeichnen und abgrenzen spezifischer Bereiche:
Konzentrieren Sie sich darauf, die in der Sortierphase etablierte Organisation zu verfeinern. Verwenden Sie Etiketten, Schilder und Bodenmarkierungsband, um das festgelegte Layout zu verstärken und es für jeden einfacher zu machen, den Arbeitsbereich ordentlich zu halten. - Ergonomische Überlegungen einbeziehen:
Ordnen Sie Gegenstände so an, dass sie in Höhen und an Orten gelagert werden, die die körperliche Belastung minimieren. Häufig verwendete Werkzeuge sollten am leichtesten zugänglich sein. - Arbeitszyklus-Diagramme verwenden:
Integrieren Sie Arbeitszyklus-Diagramme, um die Abfolge von Aufgaben und die entsprechenden Werkzeugstandorte zu visualisieren. Dies kann erheblich bei der Planung und Aufrechterhaltung eines organisierten Arbeitsablaufs helfen.
Implementierung von 5S für geordnete Bauumgebungen
In der dynamischen Umgebung einer Baustelle kann die Organisation von Werkzeugen und Ausrüstung die Produktivität erheblich beeinflussen. Systematisieren kann durch die Schaffung festgelegter Zonen für verschiedene Arten von Werkzeugen und Vorräten umgesetzt werden, die deutlich mit Bodenmarkierungsband gekennzeichnet sind.
Am häufigsten verwendete Werkzeuge könnten auf mobilen Werkzeugwagen platziert werden, die bei Bedarf zu verschiedenen Teilen der Baustelle bewegt werden können. Dies reduziert Zeitverschwendung und Aufwand beim Holen und Zurückbringen von Werkzeugen. So wird die Baustelle effizienter und körperliche Ermüdung der Arbeiter wird verringert.
3. SCHRITT: Säubern (Seiso)
Säubern als vorbeugende Wartung
Nach dem Aufräumen ist es Zeit zu reinigen, zu inspizieren und in bestimmten Fällen regelmäßige Wartungen durchzuführen. Der Hauptvorteil des Säubern-Schritts im 5S-Programm ist, dass Sie Probleme sofort erkennen und unerwartete Ausfälle verhindern können.
Säubern geht über das bloße Sauberhalten hinaus. Es schafft eine Umgebung, in der alles optimal funktioniert.
Sauber halten - Effizient bleiben
Ein sauberer Arbeitsbereich reduziert potenzielle Gefahren, die zu Fehlfunktionen, Geräteausfällen und Sicherheitsproblemen führen können. In einer aufgeräumten Umgebung verschwenden Sie keine Zeit (überflüssige Bewegungen) mit der Suche nach Werkzeugen oder der Behebung von Unterbrechungen durch Geräteausfälle. Zudem vereinfacht es den Lernprozess für neue Mitarbeiter.
Ein sauberer und gut gewarteter Arbeitsplatz ist der Schlüssel zur Verbesserung der Qualität und zur Aufrechterhaltung hoher Standards in Ihren täglichen Abläufen. Und seien wir ehrlich: Ist es nicht einfach angenehmer, in einem Raum zu arbeiten, in dem alles genau da ist, wo es sein sollte?
Wichtige Strategien für eine effektive Wartung
- Einen Reinigungsplan erstellen:
Es geht nicht nur ums Aufräumen, sondern auch ums genauere Hinsehen. Regelmäßige Reinigungszeiten sollten gleichzeitig als Inspektionszeiten dienen. - Sofort reinigen:
Haben Sie eine Verschüttung oder Schmutz bemerkt? Gehen Sie nicht daran vorbei. Reinigen Sie es sofort. So bleibt Ihr Bereich sicher und bereit für das, was als Nächstes kommt. - Detaillierte Inspektionen sind entscheidend:
Führen Sie während der Reinigung auch Inspektionen auf Verschleiß oder Beschädigungen durch. Dies stellt sicher, dass Ihre Ausrüstung zuverlässig und sicher bleibt.
Eine Baustelle zum Vorbild für Sauberkeit machen
Auf Baustellen kann Säubern buchstäblich Leben retten. Bereiche frei von Trümmern zu halten und saubere Ausrüstung zu gewährleisten, kann Unfälle verhindern. Alle, einschließlich des Reinigungspersonals, müssen Sauberkeitsstandards einhalten, um kleine Probleme frühzeitig zu erkennen und zu beheben.
Indem Sie alle Teammitglieder in das 5S-Programm einbeziehen, stellen Sie sicher, dass unnötige Gegenstände schnell identifiziert und entfernt werden. So werden sie nicht zu Hindernissen. Festgelegte Bereiche für Abfälle, mobile Reinigungsstationen und organisierte Reinigungswerkzeuge erleichtern es allen, ihre Umgebung in Top-Zustand zu halten.
Säubern hilft Ihnen, einen Raum zu erhalten, der genauso arbeitsbereit ist wie Sie. Es bedeutet, dass Sie jeden Morgen Ihre Baustelle betreten können und wissen, dass alles für den Erfolg bereit ist. Ist es nicht besser, wenn die Dinge einfach so funktionieren, wie sie sollen?
4. SCHRITT: Standardisieren (Seiketsu)
Einheitliche Praktiken für Höchstleistungen
Die nächste Phase besteht darin, die vorherigen Schritte zu standardisieren. Ziel ist es, Sauberkeit, Ordnung und Wartung über alle Schichten und Teammitglieder hinweg konsistent aufrechtzuerhalten.
Feste Standards sind wichtig
Stellen Sie sich vor, wie reibungslos Abläufe sind, wenn alle auf dem gleichen Stand sind. Genau deshalb ist Standardisierung der Schlüssel.
Durch die Schaffung einheitlicher Verfahren und Erwartungen stellen Sie sicher, dass jeder genau weiß, was zu tun ist und wann. Dies verbessert die Effizienz und reduziert Fehler. Dieser Standardisierungsschritt legt den Grundstein für einen visuellen Arbeitsplatz, an dem Prozesse klar sind und Abläufe nahtlos funktionieren.
Grundlagen für kontinuierliche Produktivitätssteigerung schaffen
- Klare Richtlinien entwickeln:
Dokumentieren Sie die besten Praktiken für die Instandhaltung des Arbeitsbereichs. Dies umfasst Reinigungsprotokolle bis hin zu Regeln für den Umgang mit Werkzeugen. So können alle die gleichen Standards einhalten und die grundlegenden Konzepte von 5S werden verstärkt. - Schulungen durchführen:
Regelmäßige Schulungen stellen sicher, dass alle Mitarbeiter, einschließlich Neueinsteiger, die standardisierten Verfahren verstehen und effektiv umsetzen können. - Visuelle Hilfsmittel einsetzen:
Unterstützen Sie Verständnis und Einhaltung mit visuellen Hilfsmitteln. Schilder, Farbcodes und Plakate erinnern alle an die geltenden Standards.
Standards auf Baustellen aufrechterhalten
Auf Baustellen, wo Variablen und Chaos häufig sind, steigert die Standardisierung von Abläufen die Effizienz erheblich. Die Festlegung von Verfahren für Werkzeugwartung, Arbeitsplatzorganisation und betriebliche Abläufe gewährleistet reibungslose Operationen, selbst bei Team- oder Projektänderungen.
Ein Beispiel: Die Standardisierung des Standorts und der Wartung von Sicherheitsausrüstung gewährleistet schnellen Zugriff in Notfällen. Dies reduziert Risiken. Die Verankerung dieser Praktiken schafft eine visuelle Fabrikumgebung. Hier treibt Konsistenz die Produktivität an, und Prozesse werden vorhersehbar, zuverlässig und sicher.
5. SCHRITT: Selbstdisziplin (Shitsuke)
Kontinuierliche Verbesserung durch konsequentes Handeln
Dieser Schritt konzentriert sich darauf, die durch die vorherigen Schritte gesetzten Standards aufrechtzuerhalten. Ziel ist es, sie in die Kultur des Arbeitsplatzes einzubetten und so einen visuellen Arbeitsplatz zu sichern.
Gute Gewohnheiten am Leben erhalten
Selbstdisziplin soll die guten Gewohnheiten aufrechterhalten. Es geht darum, sicherzustellen, dass die Verbesserungen in Effizienz und Sauberkeit zu einem festen Bestandteil des täglichen Betriebs werden. Wie effektiv wäre es, wenn jeder konsequent hohe Standards einhielte, unabhängig vom Projekt oder Tag?
5S nachhaltig verankern
- Regelmäßige Audits und Überprüfungen:
Planen Sie regelmäßige Kontrollen, um sicherzustellen, dass alle 5S-Standards kontinuierlich eingehalten werden. Diese Überprüfungen helfen, Rückschritte zu erkennen und gute Praktiken zu verstärken. Sie fördern die Beteiligung und machen diese Standards zu einem wichtigen Teil der Unternehmenskultur. - Unternehmensführung einbeziehen:
Die Führungsebene spielt eine entscheidende Rolle bei der Aufrechterhaltung der 5S-Praktiken. Wenn Unternehmensleiter aktiv am 5S-Programm teilnehmen und es unterstützen, sendet dies ein starkes Signal. Es zeigt, dass diese Praktiken nicht optional, sondern wesentlich für die Optimierung der Produktionsprozesse und den langfristigen Erfolg sind. - Neue Praktiken einführen:
Um den Schwung aufrechtzuerhalten, erwägen Sie die Integration von Ansätzen, die auf dem bestehenden 5S-Rahmen aufbauen. Dies könnte innovative Wege zur Abfallreduzierung, zum Management überschüssiger Bestände oder zur Förderung von Verantwortlichkeit umfassen. - Anerkennung und Belohnungen:
Implementieren Sie ein System zur Anerkennung und Belohnung der Einhaltung und Verbesserung von 5S-Praktiken. Dies motiviert alle, sich an die etablierten Standards zu halten.
5S auf Baustellen aufrechterhalten
Auf Baustellen, wo sich die Bedingungen schnell ändern können, ist die Aufrechterhaltung organisierter und effizienter Praktiken entscheidend. Die regelmäßige Überprüfung der Baustellenorganisation, Sauberkeit und Sicherheitsstandards gewährleistet, dass jede Projektphase den höchsten Standards entspricht.
Stellen Sie sich vor, jeder Arbeiter beginnt seine Schicht jeden Tag in einer gut organisierten, sicheren und effizienten Umgebung. Dies reduziert Risiken, verringert Verschwendung und steigert Moral und Produktivität erheblich.
Durch die tiefe Integration dieser Praktiken in die Routine macht Selbstdisziplin das 5S-System zu einem natürlichen Aspekt des täglichen Arbeitslebens, anstatt nur zu einem weiteren Regelwerk. Ist es nicht beruhigender, wenn die Standards für das Team zur zweiten Natur werden?
Revolutionieren Sie 5S mit aktuellen Lean-Trends
Moderne technologische Fortschritte haben das traditionelle 5S erheblich verbessert. Dies macht es in der heutigen digitalen und umweltbewussten Lean-Landschaft noch relevanter.
Integration digitaler Technologien
Die Integration von digitalen Technologien wie IoT, KI und Echtzeit-Datenüberwachung transformiert 5S und macht es dynamischer. Ein Beispiel dafür ist die Lcmd-Software, die für Lean Management in der Bauindustrie entwickelt wurde. Sie ermöglicht Projektmanagern, Echtzeit-Übersicht zu behalten und sich schnell an Veränderungen anzupassen. Dies erleichtert die sofortige Identifizierung und Lösung von Problemen und hält hohe Sauberkeits- und Organisationsstandards aufrecht.
Digitale Technologien ermöglichen ein präziseres und vorausschauendes Management von Arbeitsabläufen und Ressourcen. Dies verspricht erhebliche Verbesserungen in der betrieblichen Effizienz und Entscheidungsfindung.
{{cta}}
Digital Twin Technologie
Ein Digital Twin ist eine virtuelle Nachbildung eines physischen Systems, Prozesses oder einer Umgebung. Er ermöglicht Echtzeit-Simulation und -Analyse. Diese Technologie hat großes Potenzial, die 'Systematisieren'-Phase von 5S zu unterstützen. Besonders nützlich ist sie in Umgebungen, wo die Komplexität und Kosten für die Neuanordnung physischer Räume hoch sind, wie in großen Produktionsanlagen, Luft- und Raumfahrt, Automobilindustrie oder Gesundheitseinrichtungen.
Augmented Reality (AR)
AR ist eine Technologie, die digitale Informationen über die reale Welt legt. Sie optimiert die Wahrnehmung und Interaktion der Nutzer mit ihrer Umgebung. AR wird für Schulungen und Wartung eingesetzt und passt zur 'Standardisieren'-Phase von 5S. Sie bietet in Echtzeit interaktive Anleitungen, die die Prozesskonsistenz aufrechterhalten und Schulungszeiten in verschiedenen Branchen verkürzen.
Digitale Dokumentationssysteme
Moderne Dokumentationssysteme bieten effiziente Möglichkeiten zur Aufzeichnung von Änderungen und Prozessen. Im Kontext der 5S-Methodik, besonders in der 'Systematisieren'-Phase, können sie sehr nützlich sein.
Einfache digitale Lösungen wie Datenbanken oder Tabellenkalkulations-Tools sind für die meisten 5S-Implementierungen ausreichend. Sie verbessern die Effizienz bei der Verwaltung von Werkzeugen und Materialien, indem sie Aktualisierungen des Organisationssystems gut dokumentieren.
Diese digitalen Werkzeuge ergänzen die traditionellen visuellen Kontrollen von 5S und unterstützen eine effektive, datengestützte Kontinuität der Verbesserungsprozesse.
Kreislaufwirtschaft
Die Kreislaufwirtschaft konzentriert sich auf Materialwiederverwendung und Recycling zur Abfallreduzierung. Wenn ihre Prinzipien in die 5S-Methodik im Lean Management integriert werden, verbessern sie die 'Sortieren'- und 'Selbstdisziplin'-Phasen. Dies führt zu einer nachhaltigeren und effizienteren Nutzung von Ressourcen.
Fazit
Wir haben 5S nicht nur zur Organisation unserer Räume genutzt, sondern um unsere gesamten logistischen Abläufe zu optimieren. Dadurch wurden unsere Fulfillment-Center zu einigen der effizientesten weltweit.
Jeff Bezos, Gründer von Amazon
Mit dem 5S-System verwandeln Sie den Arbeitsplatz von "gerade so okay" in eine “Lean Machine”. Das bedeutet, jeder kleinste Teil Ihres Arbeitsplatzes muss perfekt sein. Die 5S-Methode ist ein Ausgangspunkt für jedes Unternehmen, das ambitionierte Ziele erreichen möchte.
Denken Sie darüber nach - wie viel Zeit wird verschwendet, nur weil Dinge nicht dort sind, wo sie sein sollten?
Die Einbettung des 5S-Systems in den Arbeitsalltag macht die anfänglichen Bemühungen zu mehr als nur einem einmaligen Aufräumen. Es geht darum sicherzustellen, dass Sie nicht zurückfallen. Der neue, sauberere und geordnetere Raum soll dauerhaft bestehen bleiben. Er macht einen Unterschied bei der Reduzierung von Verschwendung und der Vermeidung ungeplanter Ausfallzeiten - und steigert langfristig Ihre Produktivität.
Und ja, das bedeutet, dass jeder - von Neulingen bis zu denjenigen, die schon ewig dabei sind - mitmachen muss. Es ist eine Teamleistung. Jedes Stück Ausrüstung, jedes Werkzeug, jeder Prozess, den Sie verbessern, ist eine Vorabinvestition in unsere Produktivität.
Lassen Sie diesen Schwung nicht nachlassen. Die Aufrechterhaltung von 5S bedeutet, dass Sie sich weiterhin entwickeln und verbessern, anstatt sich mit "gut genug" zufriedenzugeben.