Share this article:
Key Takeaways from this article
- The 5S method is a systematic approach to workplace organization, originating from Toyota, that improves efficiency and safety.
- The 5 S's stand for Sort, Set in Order, Shine, Standardize, and Sustain - each representing a crucial step in the process.
- Follow our step-by-step guide to apply the 5S method to your workplace.
- Access our practical 5S checklist template to guide your implementation process.
Implementing 5S at GE transformed not just our factory floors but our entire operational ethos, driving efficiencies and reducing waste at every level.
Jack Welch, former CEO of General Electric
The 5S method, originating from the Toyota Production System, is a systematic framework. It is designed to improve workplace efficiency and safety by organizing the work environment.
At its core, it’s about creating a work space where everything has its place and everything is in its place.
By following the five principles—Sort, Set in Order, Shine, Standardize, and Sustain—you eliminate unnecessary clutter and streamline daily tasks.
The result? A workplace clean and free of wasted space, where visual control is maintained to consistently improve quality.
What does the 5S stand for?
The 5S method is a broader construct crucial in lean management, primarily because it is closely connected with key lean managament goal - eliminating waste. This method is widely used in various areas, e.g. lean manufacturing or lean construction.
While 5S does not directly address all 8 types of waste recognized in lean, it significantly impacts several of them.
By keeping everything in its right place and ensuring the work space is clean and standardized, 5S cuts down on delays, errors, and unnecessary work. This not only boosts productivity but also keeps things safe and sound.
The 5S system revolves around five key stages:
- Sort
- Set in Order
- Shine
- Standardize
- Sustain
With standardized work practices from 5S, every part of the workplace stays efficient. And you know what? This setup is a staple in many productivity press initiatives worldwide, like Boeing, Ford or previously mentioned Toyota.
Benefits of the 5S System
Implementing the 5S system offers several key benefits that drive efficiency and maintain a high standard of operations in the workplace.
Numerous studies across sectors like automotive and healthcare support this, showing a positive correlations between 5S and enhanced performance. For detailed insights, see the comprehensive case studies provided in the following resources: Study on Automotive Cable Production, 5S Case Studies, and Lean Management Implementations.
Here’s a breakdown of what advantages 5S delivers:
- Makes work processes more efficient
- Promotes continuous improvement in the workplace
- Cuts down on wasted time, unnecessary motion
- Reduces the risk of equipment failure and increases overall safety
- Encourages visual cues for overall cleanliness
- Creates a more organized, productive, and waste-efficient work environment
So how exactly can 5S transform any workplace?
Step-by-Step & 5S Checklist Template
Before you begin your 5S journey, we highly recommend downloading our free 5S checklist template. This comprehensive tool will help you stay organized and focused throughout the process. Our XLSX file includes built-in calculations, allowing you to easily track your progress across each phase of the 5S methodology.
Here's how it works:
- For each item on the checklist, assign a value from 1 to 5, with 5 being the best possible grade.
- Aim for an average score of 4 (80% Total 5S Score) across all items to consider your 5S process successfully implemented.
- Remember, following the Kaizen principle of continuous improvement, there's always room for growth. Strive for that ideal 100% score!
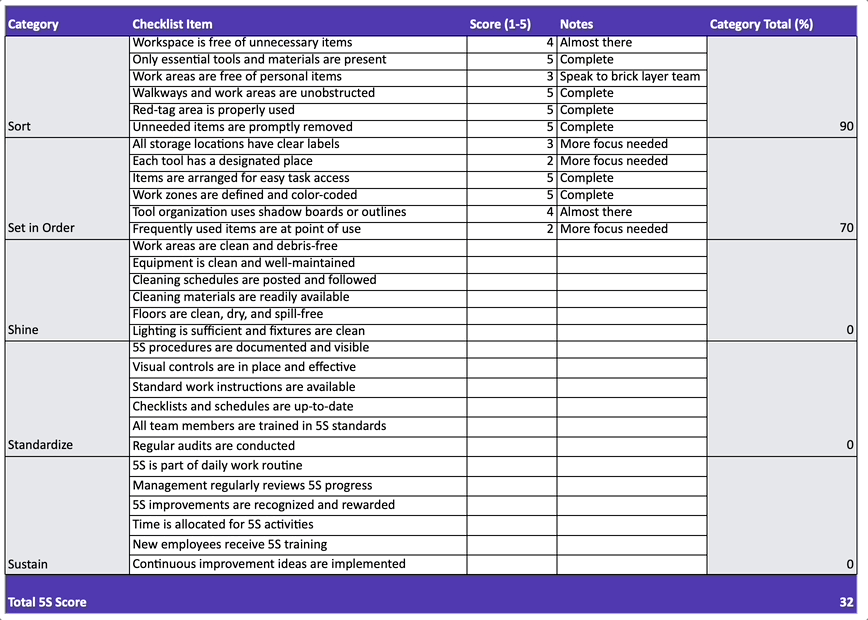
Whether you're implementing 5S on a construction site or in a warehouse, conducting a 5S audit, or creating a customized 5S cleaning checklist, our 5S checklist template Excel file provides a solid foundation. It's perfect for both beginners and experienced practitioners looking to refine their 5S approach.
{{asset}}
1. STEP: Sort
The Role of Sort in Workplace Organization
Sort is the first step in the 5S methodology, where you categorize all items in the work environment.
The primary goal is to clear cluttered space and unneeded items from the work area to prevent the accumulation of items that are not required for immediate work which can slow down work processes.
Why Sorting Matters in 5S
By keeping only what's necessary, you streamline operations and reduce the time spent searching for items. This also improves visual communication, making it easier for team members to quickly understand workflows and locate necessary tools without confusion.
Sorting Strategies in the 5S Program
- Categorize and Clarify:
Group items into categories such as "essential," "non-essential," and "unsure" to determine what should be kept, stored, or discarded. - Red Tag System:
Implement a red tag system to mark items that need further evaluation before being discarded or relocated. Effectively organized red tagged items and optimized tool storage makes clear which items to keep and which to remove. - Digital Sorting:
Consider digital sorting by organizing files and folders on your computer. Delete any obsolete files and arrange the remaining digital items into structured folders, just as you would with physical items. - Visual Management Tools:
Organize physical tools and equipment using visual cues like labels, floor markings, or shadow boards so that is easier for everyone to identify where things should go as they begin to declutter.
Creating Safer, More Efficient Construction Sites
In the construction sector, the Sort step is crucial for maintaining an optimized and safe workspace. By evaluating all tools and equipment, workers identify and remove unnecessary items that are obsolete or seldom used. Remaining items can be immediately discarded.
This decluttering significantly enhances workplace efficiency by clearing up space, which reduces unnecessary transportation and minimizes the need for frequent department tours, thereby reducing safety hazards.
The result is a more organized environment where essential tools are readily accessible, thereby speeding up operations and ensuring safety on the site.
2. STEP: Set in Order (Seiton)
Organizing for Efficiency and Mastering Workspace Layout
Set in Order builds on the foundation laid by the Sort phase. Sometimes referred to as "Straighten," this step involves arranging all necessary items so they are easily accessible and logically positioned to streamline tasks and workflows.
Why Everything Should Have Its Place
Sort in order in 5S facilitates the maximization of space needed and supports efficient production processes.
It slashes the time you spend hunting for stuff and cuts down on workflow interruptions. Knowing exactly where everything is means you can move faster and more smoothly through your tasks. Isn't that a relief?
Strategies for Optimal Organization in 5S: Making Every Item Count
- Label and delineate specific areas:
Focus on fine-tuning the organization established in the Sort phase. Use labels, signs, and floor marking tape to reinforce the established layout, making it easier for everyone to keep the workspace orderly. - Implement Ergonomic Considerations:
Arrange items so that they are stored at heights and locations that minimize physical strain. Tools frequently used should be the most accessible. - Utilize Job Cycle Charts:
Incorporate job cycle charts to visualize the sequence of tasks and their corresponding tool locations. This can significantly aid in planning and maintaining an organized workflow.
Implementing 5S for Orderly Construction Environments
In the dynamic environment of a construction site, keeping tools and equipment organized can significantly impact productivity. Set in Order can be implemented by creating designated zones for different types of tools and supplies, marked clearly with floor marking tape.
Tools most commonly used could be placed on mobile tool carts that can be moved as needed to various parts of the site. This reduces waste time and effort in retrieving and returning tools, making the site more efficient and reducing physical fatigue for workers.
3. STEP: Shine (Seiso)
Shine as Preventative Maintenance
When you've cleaned things up, it's time to clean up, inspect and in certain instances do regular maintenance. Shine step 's main advantage in 5S program is that you can detect problems immediately and prevent unexpected breakdowns.
Shine isn’t just about keeping things looking good—it’s about maintaining an environment where everything functions at its best.
Keeping it Clean - Keeping it Efficient
Keeping your work area clean reduces those potential hazards that can cause malfunctions, equipment failure and safety issues. A tidy environment means you're not wasting time (extra motion) hunting for tools or dealing with interruptions from equipment breakdowns. Plus, it streamlines the learning process of new employees.
Clean and well maintained workplace is a key to improving quality and maintaining high standards in your daily operations. Plus, let's be honest, isn’t it just nicer to work in a space where everything is right where it should be?
Key Strategies for Effective Maintenance
- Set a cleaning schedule:
It's not just about picking up; it's about looking closer. Regular cleaning times should double as inspection times. - Clean as you go:
Spotted a spill or some debris? Don't walk by; clean it up right away. It keeps your space safe and ready for whatever's next. - Detailed inspections are key:
During cleanups, also inspect for wear or damage to ensure your equipment remains reliable and safe.
Turning a Construction Site into a Model of Shine
On construction sites, Shine can literally save lives. Keeping areas clear of debris and ensuring equipment is clean can prevent accidents. Everyone, including janitorial staff, must uphold cleanliness standards to catch and address small issues before they escalate.
By involving all team members in the 5S program you ensure that unneeded items are quickly identified and removed, preventing them from becoming obstacles. Designated areas for waste, portable cleaning stations, and organized cleaning tools make it easier for everyone to keep their surroundings in top condition.
Shine helps you maintain a space that’s as ready to work as you are. It means you can walk into your site each morning knowing everything is set up for success. Isn’t it better when things just work like they’re supposed to?
4. STEP: Standardize (Seiketsu)
Uniform Practices for Peak Performance
The next phase is to standardize the previous steps to maintain cleanliness, order, and maintenance consistently across all shifts and team members.
The Significance of Setting Standards
Think about how smooth operations are when everyone is on the same page. That’s exactly why standardization is key.
By creating uniform procedures and expectations, you make sure that everyone knows exactly what to do and when to do it, which improves efficiency and reduces errors. This standardize step builds the foundation for a visual workplace where processes are clear, and operations run seamlessly.
Laying Foundations for Ongoing Productivity Press
- Develop clear guidelines:
Write down the best practices for maintaining the workspace, from cleaning protocols to tool handling rules. This helps everyone follow the same standards, reinforcing the underlying concepts of 5S. - Implement training sessions:
Regular training ensures that all employees, including the newcomers, understand and can execute the standardized procedures effectively. - Use visual aids:
Support understanding and compliance with visual tools like signs, color codes, and placards that remind everyone of the standards in place.
Maintaining Standards on Construction Sites
On construction sites, where variables and chaos are common, standardizing operations significantly boosts efficiency. Setting procedures for tool maintenance, workspace organization, and operational protocols ensures smooth operations, even with team or project changes.
For example, standardizing the location and upkeep of safety equipment ensures quick access in emergencies, reducing risks. Embedding these practices creates a visual factory environment, where consistency drives productivity and processes become predictable, reliable, and secure.
5. STEP: Sustain (Shitsuke)
Continuous Improvement Through Consistent Action
This step focuses on maintaining the standards set by the previous steps and embedding them into the culture of the workplace, securing it remains a visual workplace.
Keeping Good Habits Alive
Sustain is supposed to keep the good habits going, to make sure that the improvements in efficiency and cleanliness become a permanent part of daily operations. How effective would it be if everyone consistently upheld high standards, no matter the project or day?
Making 5S Stick
- Regular audits and reviews:
Schedule regular checks to ensure that all 5S standards are continuously met. These reviews help catch any backsliding and reinforce good practices, fostering building participation and making these standards a key part of the organizational culture. - Involve Company Leaders:
Leadership plays a crucial role in sustaining 5S practices. When company leaders actively participate and support the 5S program, it sends a strong message that these practices are not just optional, but essential for optimizing production processes and ensuring long-term success. - Introduce New Practices:
To keep the momentum going, consider integrating approaches that build on the existing 5S framework. This could involve innovative ways to reduce waste, manage excess inventory, or promote accountability. - Recognition and rewards:
Implement a system to recognize and reward compliance and improvements in 5S practices. This motivates everyone to adhere to the established standards.
Sustaining 5S on Construction Sites
On construction sites, where conditions can change rapidly, sustaining organized and efficient practices is crucial. Regularly reviewing site organization, cleanliness, and safety standards guarantees that every phase of a project adheres to the highest standards.
Imagine every worker starting their shift in a well-organized, safe, and efficient environment, every single day. It reduces risks, cuts down on waste, and significantly boosts morale and productivity.
By deeply integrating these practices into the routine, Sustain makes the 5S system a natural aspect of everyday work life, rather than just another set of rules to follow. Isn’t it more reassuring when the standards become second nature to the team?
Revolutionizing 5S with Current Lean Trends
Modern technology advancements have significantly enhanced the traditional 5S, making it more relevant in today's digital and environmentally conscious lean landscape.
The integration of digital technologies like IoT, AI, and real-time data monitoring is transforming 5S, making it more dynamic. For example, Lcmd software, designed for lean management in the construction industry, enables project managers to maintain real-time oversight and adapt swiftly to changes. This facilitates the immediate identification and resolution of issues, maintaining high cleanliness and organizational standards.
Digital technologies are poised to revolutionize 5S by enabling more precise and anticipatory management of workflows and resources, promising substantial improvements in operational efficiency and decision-making.
Digital Twin Technology is a virtual replica of a physical system, process, or environment that allows for real-time simulation and analysis. It has significant potential to support the 'Set in Order' phase of 5S, particularly in environments where the complexity and costs of rearranging physical spaces are high, such as large manufacturing facilities, aerospace, automotive or healthcare facilities.
Augmented Reality (AR) is a technology that overlays digital information onto the real world, optimizing users' perception and interaction with their environment. Utilized for training and maintenance, AR aligns with the 'Standardize' phase of 5S, offering real-time, interactive guidance that maintains process consistency and reduces training times across various industries.
Modern documentation systems offer efficient ways to record changes and processes. In the context of the 5S methodology, especially in the 'Set in Order' phase, they can be very useful.
Simple digital solutions like databases or spreadsheet tools are sufficient for most 5S implementations. They improve efficiency in managing tools and materials by well-documenting updates to the organizational system.
These digital tools complement the traditional visual controls of 5S and support effective, data-driven continuity of improvement processes.
Circular Economy focus on material reuse and recycling to reduce waste. When integrated with the 5S methodology in lean management, its principles elevate the 'Sort' and 'Sustain' phases, leading to more sustainable and efficient use of resources.
Conclusion
We used 5S not just to organize our spaces but to streamline our entire logistical operations, making our fulfillment centers some of the most efficient on the planet.
Jeff Bezos, founder of Amazon
With the 5S system, you’re taking the workplace from ‘just okay’ to a lean machine. It’s designed to reduce waste majorly, which means every little bit of your workplace needs to be spot-on. The 5S method is a starting point for any company that wants to achieve high goals and positions.
Think about it—how much time is wasted just because things aren't where they are supposed to be?
Embedding the 5S system into the daily grind is what makes those initial efforts worth more than just a one-time tidy-up. It’s about making sure you don’t slip back and that the new, cleaner, more ordered space is here to stay, making a difference in reducing waste and avoiding unplanned downtime - boosting your productivity long-term.
And yes, this means everyone—from newcomers to those who’ve been here forever—needs to pitch in. It’s a team effort. Every piece of equipment, every tool, every process that you improve is an up front investment in our productivity.
Let’s not let this momentum fade. Keeping up with 5S means you continue to evolve and improve, not just settle for "good enough."