Share this article:
Key Takeaways from this article
Think back to your last stroll through a construction site. The familiar sight of unused materials stacking up and teams paused, waiting on the next batch of supplies…This isn’t just a sign of a disorganized project—it’s a blueprint for bleeding money.
Every minute and material counts in construction, yet the industry is notoriously fraught with inefficiency. From overproduced materials cluttering sites to precious hours lost waiting for deliveries, waste is not just common—it’s costly!
Implementing lean production principles can significantly reduce these inefficiencies by supporting a continuous flow of materials and work processes. This approach minimizes downtime and keeps your projects moving smoothly.
Let’s dive into the 8 types of waste in lean construction that are dragging down your projects and provide clear, actionable steps to eliminate them.
It's time to clean up the mess.
What is Lean Waste and Its Impact on Value Creation
In the context of lean principles, "waste" is defined as any activity or process that does not add value to the customer.
In lean thinking, value is created by producing goods or services that meet the needs of the customer at the right time and at an appropriate price, as defined by the customer. Anything that does not contribute to this value is considered waste.
Acronym for the 8 Wastes in Lean Construction
Lean methodology identifies specific types of waste using the acronym "DOWNTIME" or the original Japanese term “Muda.”
Originally conceived as part of the Toyota Production System, Muda, a key concept in lean philosophy, translates as "futility" or "wastefulness." Muda is a key concept in lean construction management. It targets any activity that consumes resources without enhancing customer value, emphasizing the critical need for waste elimination.
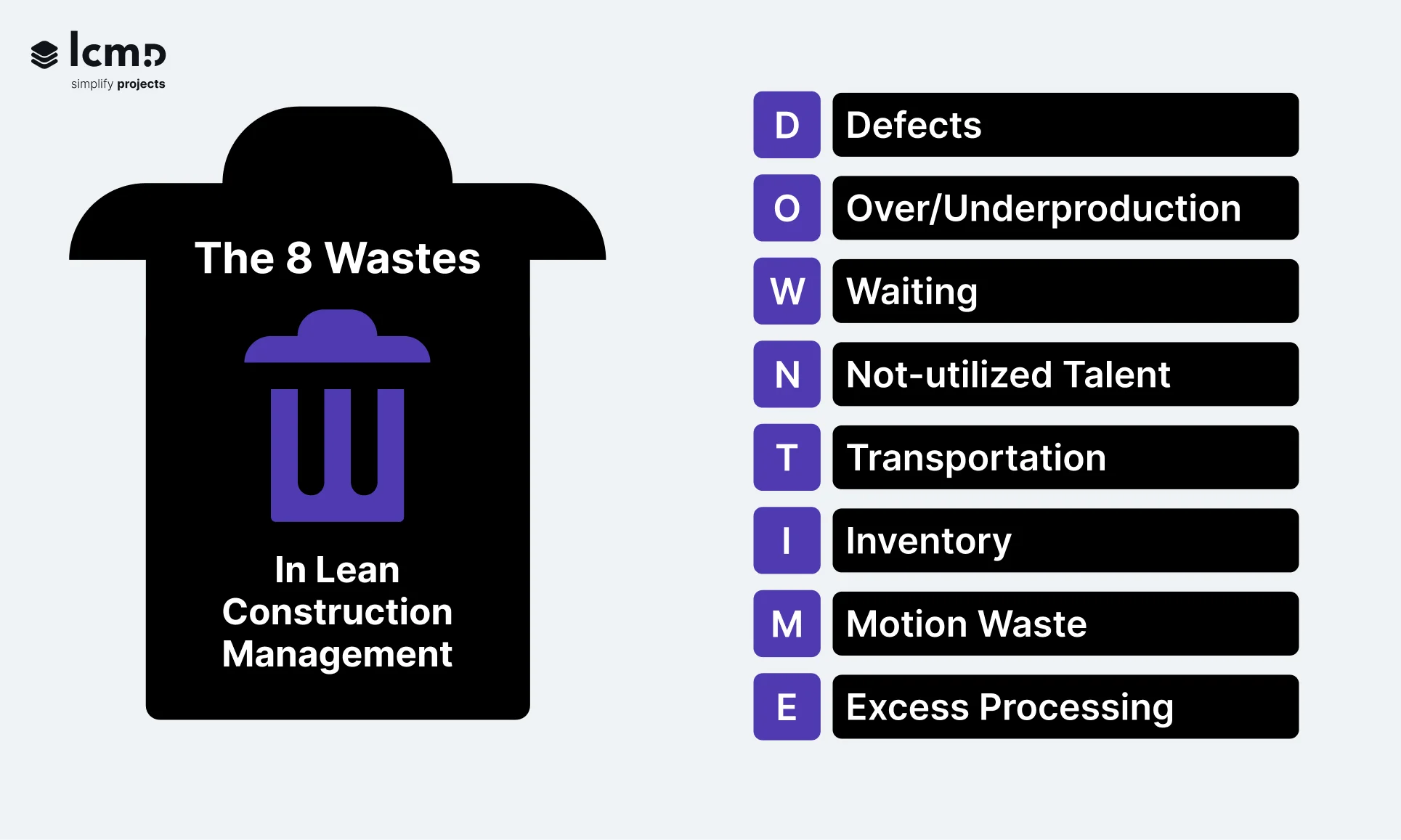
All we are doing is looking at the timeline from the moment the customer gives us an order to the point when we collect the cash. And we are reducing that timeline by removing the non-value-added wastes.
Taiichi Ohno
The western world has adopted this approach as a perfect example of effective waste management.
To tackle these inefficiencies, the acronym "DOWNTIME" categorizes specific types of waste within lean manufacturing. This framework guides you to identify waste and pinpoint areas needing improvement, critical for elevating efficiency and quality management in the construction and manufacturing process.
As we turn the page, let's confront the sobering reality of waste in our industry head-on.
8 Wastes of Lean: Key Challenges and Solutions
The waste in our industry is staggering. It’s crucial to be efficient in our designs and processes to minimize this and build sustainably
Frank Gehry
What stands between efficiency and unnecessary expenses? Often, it’s these wastes lurking in the shadows, along with additional waste that can creep into any process.
Therefore, it's so important for any construction project to identify, reduce, or even eliminate all 8 wastes of lean.
Doing so leads to better production process management, improved project management, and smarter use of construction resources, facilitating a continuous flow of work.
However, as lean practitioners focused on eliminating waste, how do you identify and tackle these critical challenges? What are the best strategies and tools for managing these issues effectively in your day-to-day operations?
We’ll guide you on this lean journey and offer you practical solutions that can transform the way you manage construction tasks. Ready to streamline your processes and elevate your operational efficiency?
Here are the core types of waste as typically defined in lean methodology:
- Defects: Errors or defects in the product or service that require rework or corrections.
- Overproduction: Producing more of a product or service than is needed, which can lead to excess inventory.
- Waiting: Idle time when resources are not being used effectively, often due to bottlenecks in the workflow.
- Non-utilized talent: Underusing people’s talents, skills, or knowledge.
- Transportation: Unnecessary movements of products or materials, which do not add value.
- Inventory: Excess products and materials not being processed.
- Motion: Unnecessary movements by people, such as walking or adjusting equipment, which do not add value.
- Excess processing: More work or higher quality than is required by the customer.
The most dangerous kind of waste is the waste we do not recognize.
Shigeo Shingo
1. Defects
Ever seen what a small flaw can do to a large project? It's like a tiny crack in a dam—it might not seem like much, but it can lead to a flood of problems. Defects in construction can be anything from issues in raw materials, human error, equipment failures, or inadequate specifications.
Why does this matter? Because every time something goes wrong, it means going back, spending more, and delaying the next steps.
So, what's the challenge here? Reducing defects can be particularly challenging because it requires a deep understanding of the entire production process, precise quality control, and often significant changes to processes or even design to avoid over processing waste.
How to Tackle Defects in Construction Projects for Improved Efficiency
- It starts with setting up tight quality controls that catch problems before they escalate, preventing extra processing.
- Addressing defects also requires continuous monitoring and improvement to minimize over processing.
- Quality management features in Lean Software can help track defects and trends over time, enabling more proactive quality control measures. This enables in reducing the rate of defects and minimizing the need for rework.
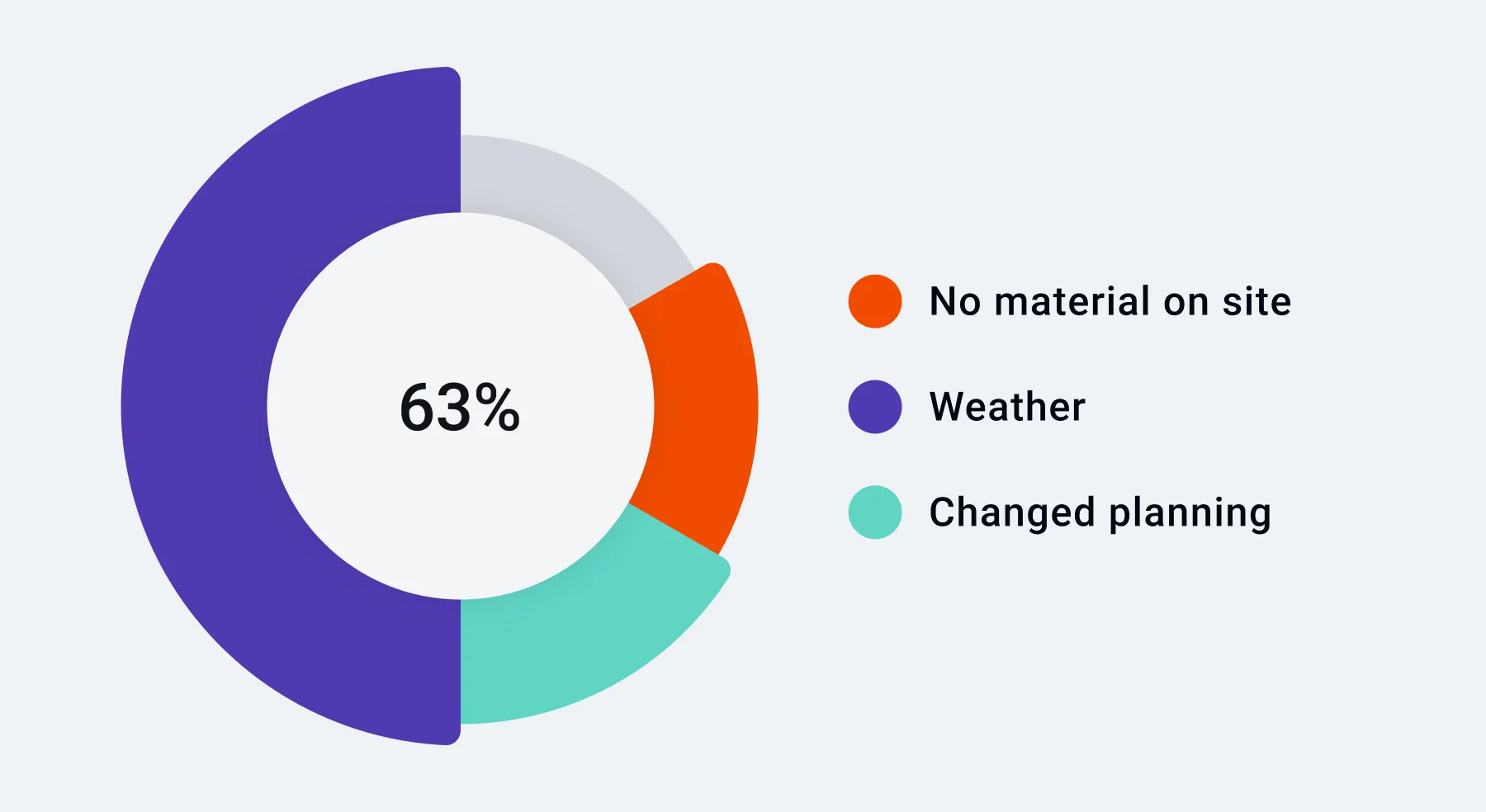
Think about it—by investing a bit more in prevention, you gain a new perspective on quality. You can save a lot not just in costs, but in preserving the integrity and timeline of your project.
2. Overproduction
Overproduction in construction ties up your resources and space with excess materials that might never be used. Why does this happen? Sometimes, it's the 'just in case' mentality, other times it's poor demand forecasting.
Why should you care? Storing surplus materials isn't just a space hogger; it’s a money sink. And let’s not forget, the more you produce, the higher your initial costs.
So, how do you fix this?
Fixing Overprocessing for a Leaner Construction Process
- Implementing Just-In-Time (JIT) production can change the game. It means producing exactly what's needed, when it's needed, based on real project demand, not guesses.
- Pull planning is another effective strategy to align production schedules with actual demand, ensuring that you only produce what is required.
- Lean Management Software can also help prevent overproduction waste by providing better demand forecasting and production planning tools. This allows organizations to match their production processes more closely with actual demand, reducing the likelihood of producing more than is needed.
By precisely aligning material deliveries and workflows with the phases of your construction project, you not only reduce waste but also optimize your cash flow. Isn't it better when your resources flow as smoothly as your project progresses?
3. Waiting
Whether it's materials stuck in transit, delayed approvals, or equipment not being where it needs to be, waiting can grind your project to a halt.
Why does this happen so often? Sometimes it's due to dependency issues where one part of the project stalls, causing people waiting for another to catch up. Other times, it’s poor planning or unexpected delays that throw off your whole schedule, leading to idle equipment.
What’s the cost of all this waiting? Beyond the obvious frustration, it’s a major drain on productivity. Workers are ready but idle, and every minute lost is money that’s not coming back. Projects stretch beyond their deadlines, pushing up labor costs and straining client relationships.
So, how can you cut down on waiting?
Eliminating Waiting Waste Across All Construction Phases
- The key lies in smarter project scheduling and tighter coordination. Imagine having a real-time scheduling system that updates instantly with every change.
- Or better yet, using predictive analytics to foresee delays and adjust workflows in advance.
- Lean Management Software can boost scheduling and resource allocation, reducing downtime and waiting periods. It can also improve communication between teams, securing that everyone knows when to expect deliveries of materials, when equipment is available, and when they can proceed with their tasks.
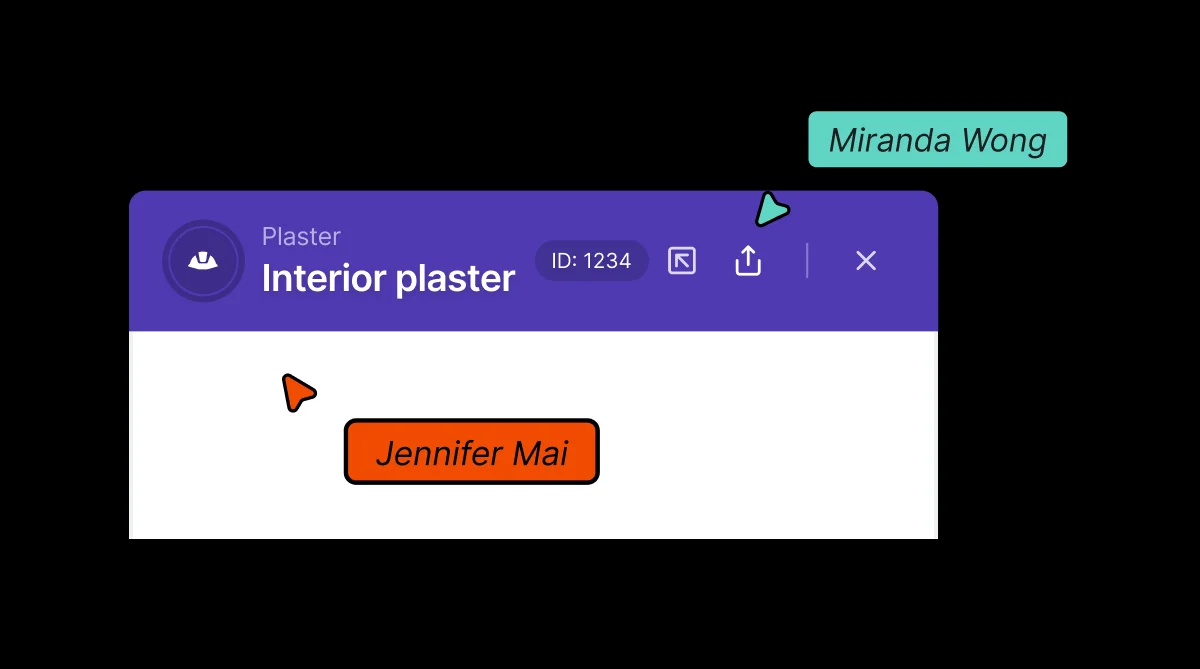
By addressing waiting waste, you not only keep your team productive but also safeguard your bottom line against the costs of waste that occurs from idle equipment and people waiting on the job site.
4. Non-utilized Talent
Non-utilized talent means that the business is missing out on valuable skills that could drive projects forward more effectively. It`s a common pitfall in many industries, and construction is no exception. Failing to harness the full potential of your workforce can lead to significant inefficiencies.
Consider the scenario where a skilled carpenter spends most of his time handling basic site cleanup because of poor task allocation. Not only does this slow down the project, but it also wastes the unique skills the carpenter brings, which could otherwise contribute to more complex and value-added activities.
The cost here is twofold: there's the direct financial impact of paying high-skill wages for low-skill work, and there’s the indirect cost associated with slower project progression and potential delays. This inefficiency can balloon project costs and extend timelines unnecessarily.
So, how do you address this waste?
Maximizing Non-utilized Talent for Higher Quality Work Processes
- Effective talent management starts with a solid understanding of the skills and human potential within your team. It means pairing people’s capabilities with the right tasks.
- Training and development play a crucial role here, as do strategies like cross-training and multi-skilling.
- By engaging employees to handle a variety of tasks, you use their time more efficiently and also prepare your team to step into different roles as needed, without missing a beat.
By maximizing human potential and engaging employees you elevate project success. This approach unlocks hidden capacity and delivers superior business results.
5. Transportation Waste
Every unnecessary movement across a construction site or between locations increases fuel costs, wear and tear on vehicles, and the risk of material damage. This not only adds to transportation waste but also complicates logistics.
Here's the impact: More transport waste means higher expenses and more potential for delays—especially if something goes wrong en route. These delays can ripple through your project, pushing back critical deadlines and piling up indirect costs.
The solution?
Reducing Unnecessary Transportation in Construction
- Streamline your logistics and material handling to reduce unnecessary transportation.
- Plan site layouts to minimize distance between storage and usage points, cutting down on moving equipment and materials more than needed.
- Use efficient routing software to schedule and track movements, making sure that materials are moved only when absolutely necessary.
- Implementing just-in-time delivery can also keep your site free from clutter and reduce handling requirements, keeping your project lean and mean on the move.
By tightening up transportation strategies, you can shave off unnecessary costs and keep your project timeline on track.
6. Inventory
Excess inventory on construction sites can lead to more than just physical clutter. It ties up funds in unused materials, occupies valuable space, and increases the risk of degradation and obsolescence. While stockpiling may seem like a precaution, it often results in higher storage costs and a greater risk of inventory loss due to damage or spoilage, inflating project costs and complicating logistics unnecessarily.
What’s the strategy to deal with it?
Managing Inventory Waste for Better Use of Materials
- Demand-driven ordering, for instance, synchronises material deliveries with actual project schedules, securing that you have just what you need, just when you need it. This method significantly cuts down on unnecessary movement of materials back and forth across the site.
- Additionally, adopting a Kanban system can help in managing on-site materials more efficiently, reducing excess and minimizing handling. Kanban keeps your work in progress at optimal levels, avoiding overstock and underuse.
- Management software is excellent for inventory control, offering tools to track stock levels in real time, predict reorder points, and optimize order quantities. This reduces excess inventory and the costs associated with storage and potential waste.
Effective inventory management cuts down on waste and improves overall project efficiency by ensuring that resources are available when needed without overburdening the site with unneeded supplies. This approach helps keep your project lean and cost-effective.
By focusing on efficient processes and process improvement, this strategy keeps your project lean and cost-effective.
7. Motion Waste
Think about how often workers move equipment from one end of the site to the other because there wasn’t a plan for where it should go. Or the energy spent maneuvering around a poorly laid out workspace, where obstacles are frequent, and nothing seems to be within easy reach. These scenarios are far too common and a clear sign that there’s much room for improvement.
What are the impacts? Poor workflow design not only leads to ergonomic issues, risking worker health and safety, but it also eats into project time, making tasks take longer than necessary. These unnecessary steps, if left unchecked, can balloon project timelines and costs.
How do you make it better?
Strategies to Reduce Excessive Motion in Construction Process
- Streamlining operations is key. Start by analyzing current workflows and identifying areas where motion waste can be minimized.
- Lean management software plays also an important role here—it provides detailed insights into daily operations, helping to pinpoint excessive movement and inefficient layout designs.
- Consider redesigning workspaces to keep tools and materials within easy reach or reorganizing job sites to ensure that the most frequently used resources are centrally located. This promotes a smooth flow of operations and reduces unnecessary movement.
- Additionally, investing in training for workers to follow optimized paths and routines can further cut down on wasted motion.
This approach helps you streamline operations. It is also beneficial in protecting your workforce from the physical strain of needless activity, guaranteeing both efficiency and workplace safety. Improving the production flow and work process ensures a smoother, safer, and more productive environment.
8. Excess Processing
In the construction world, doing more than what’s necessary isn’t a bonus—it’s a burden. The last, eighth waste - excess processing, whether it's over-engineering or adding layers of approval that aren't needed - can dramatically inflate project costs and extend timelines. Identifying where you’re adding unnecessary steps is the first step towards leaner operations.
What’s the real impact here? When you overcomplicate processes, you’re not just wasting materials and time; you’re also tying up your workforce on tasks that don’t add value. This misallocation can divert attention from critical project elements that genuinely require focus and precision.
So, how can you improve?
Reducing Over Processing Waste in Construction
- It starts with a clear understanding of project requirements and sticking strictly to them.
- Scrutinize all process steps and ask whether it aligns with the client’s needs and project goals.
- Optimising approval processes, for instance, can save days or even weeks over the course of a project.
- Also here, to address over processing, lean management software can be your ally in this effort. With its ability to provide detailed tracking and reporting, such software helps pinpoint precisely where your process might be bloated. Are there extra processing steps that routinely cause delays without improving the outcome? Can some of the quality checks be consolidated?
Conclusion
We've navigated through the treacherous waters of 8 wastes of lean in construction, pinpointing each type of waste ready to sabotage your efficiency and budget.
Adopting a continuous improvement mindset allows you to refine process continually and it` s essential for staying competitive and responsive in today's fast-paced market.
By continually seeking ways to identify waste and streamline your production process, you make sure that every resource is maximized and every minute counts.
This isn't just about making do; it's about pushing the boundaries of what's possible in construction.
Each step you take towards reducing waste is a step towards more sustainable, efficient, and cost-effective project management. So, why settle for the status quo when you can redefine it?
{{cta}}
Isn't it time you took a hard look at how your projects are run? Assess and integrate lean principles into your construction projects today. Explore the tools and strategies we've discussed, from pull planning to lean management software, and start your journey towards a leaner, meaner production line.
Ready to clean up the mess and boost your efficiency? Join countless others in the western world who have transformed their operations. Let's make waste reduction not just a goal but a reality.
FAQS
How does the acronym 'DOWNTIME' help in identifying waste?
'DOWNTIME' categorizes the eight types of waste in lean construction: Defects, Overproduction, Waiting, Non-utilized talent, Transportation, Inventory, Motion, and Excess processing. This framework helps professionals eliminate waste systematically to optimize operations.
What are the examples of 'non-value-added' activities in construction?
Non-value-added activities are those that do not contribute to the end customer's value, such as over-processing or unnecessary movements of people and equipment on the job site. Identifying and eliminating these can significantly enhance efficiency.
What impact does lean construction have on project management?
Implementing lean principles in construction helps improve project timelines, reduce costs, and enhance overall quality.
Why is it important to continuously improve in lean construction?
Continuous improvement in lean construction ensures that processes are always evolving to become more efficient. It involves analyzing feedback and data to make iterative changes that refine project outcomes and reduce waste.
What role does lean management software play in managing waste in lean construction?
Lean management software plays a crucial role in managing waste in lean construction by providing real-time data and analytics that help identify and eliminate inefficiencies, streamline operations, and ensure optimal resource allocation.
How does addressing waste improve production processes?
Addressing waste in production processes can significantly boost productivity. by streamlining operations, minimizing delays, and ensuring that resources are utilized more efficiently and effectively. This leads to smoother, faster workflows and an overall increase in output.