Share this article:
Key Takeaways from this article
Lean Construction Scheduling is a strategic approach designed to maximize project efficiency and minimize waste across construction projects. This methodology integrates various practices, including the Last Planner® System, to refine task management and increase project predictability.
Key Components of Lean Scheduling
Value Stream Mapping
This tool involves analyzing and designing the flow of materials and information required to bring a product or service to a consumer. Value Stream Mapping helps you see the whole flow of your project, from start to finish, identifying where you can cut delays and inefficiencies.
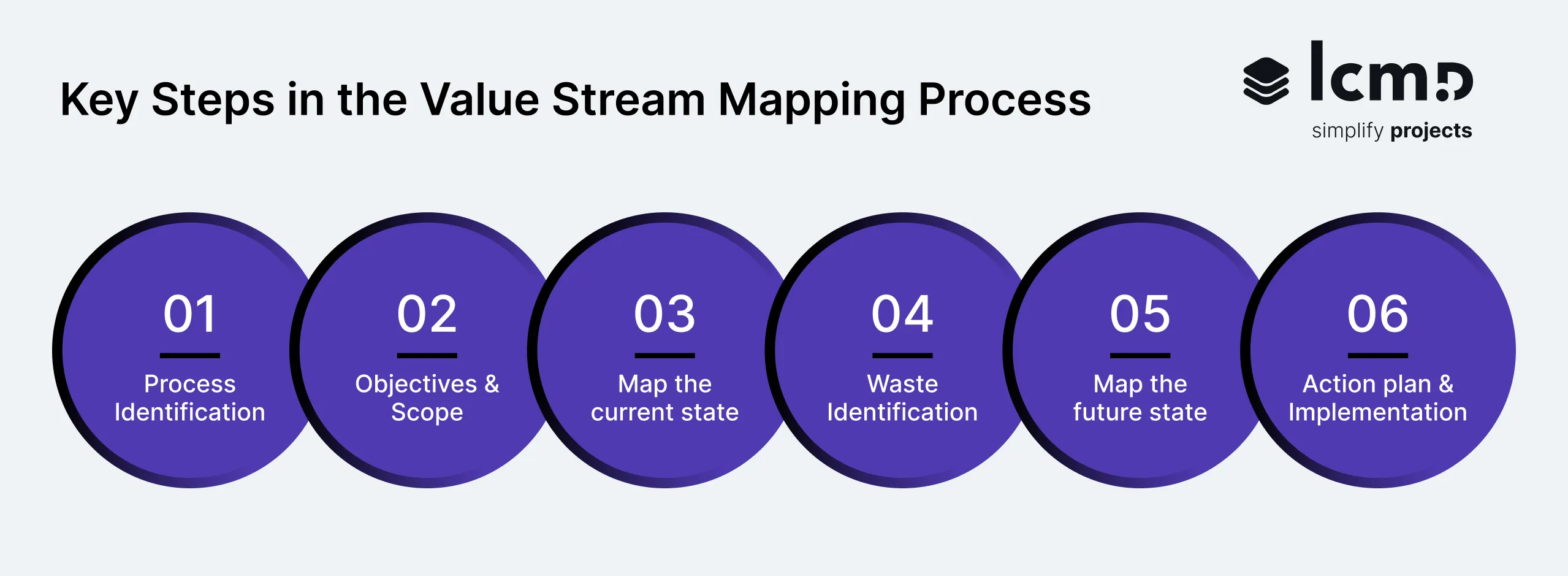
Pull Planning
Instead of a traditional push system where tasks are scheduled from the start date, Pull Planning schedules tasks based on when things are ready to go, so everything happens just in time without waiting around.
Just-in-Time (JIT) Delivery
Just like ordering food to arrive right when you want to eat, Just-in-Time delivery focuses on reducing inventory and increasing efficiency by arranging for materials and resources to be available precisely when they are needed, not before or after.
Last Planner® System (LPS)
Last Planner System is a collaborative approach to project planning and management that involves all stakeholders in the planning process to improve project outcomes. It includes several planning levels from long-term milestone planning to daily task management.
5S Workplace Organization
5S method uses a list of five Japanese words: seiri, seiton, seiso, seiketsu, and shitsuke (Sort, Set in order, Shine, Standardize, Sustain). It is aimed at setting up and maintaining a productive work environment.
Kaizen (Continuous Improvement)
Kaizen is a method where employees at all levels of a company work together proactively to achieve regular, incremental improvements to the manufacturing process.
Takt Time Planning
Takt Planning aligns production pace with customer demand by determining the maximum time allowed to produce a product in order to meet the demands consistently.
Constraint Analysis
Identifying potential bottlenecks in advance that could delay the project schedule and finding solutions or workarounds before they impact progress.
Continuous Feedback Loops
Encourages regular updates and adjustments to the project plan, supporting adaptability and immediate responses to any project changes or challenges.
What is the Last Planner® System in Lean Construction?
The Last Planner® System (LPS) is one key component of lean construction scheduling. It's a collaborative approach designed to improve project delivery in the construction sector. It’s simplifies and smooth communication and coordination among all team members involved in a project.
The system breaks down into several stages like pull planning, weekly work plans, and daily huddles. They are practical steps to keep everyone on the same page.
- Phase Scheduling (Pull Planning): This is where the magic starts. Imagine sitting down with your whole team, and instead of dictating how things will go, you ask them when and how they can deliver their part of the project.
- Weekly Schedule Plans: Every week, everyone comes together to make promises. Yes, promises! Each team member outlines what they’ll accomplish in the coming week. It’s a commitment, and because they set these goals themselves, they’re more likely to follow through.
- Daily Huddles: Quick daily meetings to check in on these commitments. It’s a great way to adjust on the fly and address any issues before they become real problems.
- Milestone Planning: Sets the major goals and deadlines of the project to guide overall progress.
- Percent Plan Complete (PPC): It serves to measure how many of the tasks that were promised for completion were actually completed, providing a metric for assessing planning reliability and effectiveness.
Core Principles of the Last Planner® System (LPS)
Core Principles of the Last Planner® System (LPS) are designed to improve project management and efficiency in construction. These are similar to the core principles of lean construction management.
Respect for People
Respect for People emphasizes the importance of acknowledging and valuing all team members involved in a project.
It means listening to everyone’s ideas and making sure that everyone, from the site workers to the project managers, feels like their input matters. When people feel respected, they’re more likely to contribute positively to the project.
Removal of Waste
In construction, there’s often a lot of wasted time, materials, and effort. This principle focuses on cutting out all that unnecessary stuff. Less waste means smoother operations and lower costs.
Focus on Process & Flow
It prioritizes maintaining a smooth and uninterrupted workflow. It aims to minimize disruptions and ensure that the project team proceeds without unnecessary delays.
By focusing on the overall process and ensuring tasks are well-coordinated, projects can achieve better productivity and eliminate bottlenecks.
Generation of Value
Generation of value aims to maximize the value delivered to clients and stakeholders.
Every step in the project should contribute positively to the final outcome. By coordinating tasks with the project schedule, teams ensure timely and efficient delivery of all deliverables.
Continuous Improvement
Continuous Improvement is essential in construction project management. It involves regularly reflecting on past projects to learn and improve.
This principle aims on consistently enhancing processes and outcomes, helping teams to adapt and evolve. By doing so, teams ensure better use of time and resources, making each project more efficient than the last.
Optimize the Whole
Optimize the whole stresses the importance of viewing the project as an integrated system rather than focusing on individual parts.
It consideres each milestone and make sure that all elements work together harmoniously.
Levels of the Last Planner® System (5 Conversations)
The Last Planner System organizes planning through a series of levels that are sometimes referred to as "five crucial conversations." These levels are structured around specific planning meetings and activities that promote collaboration and commitment among all project team members.
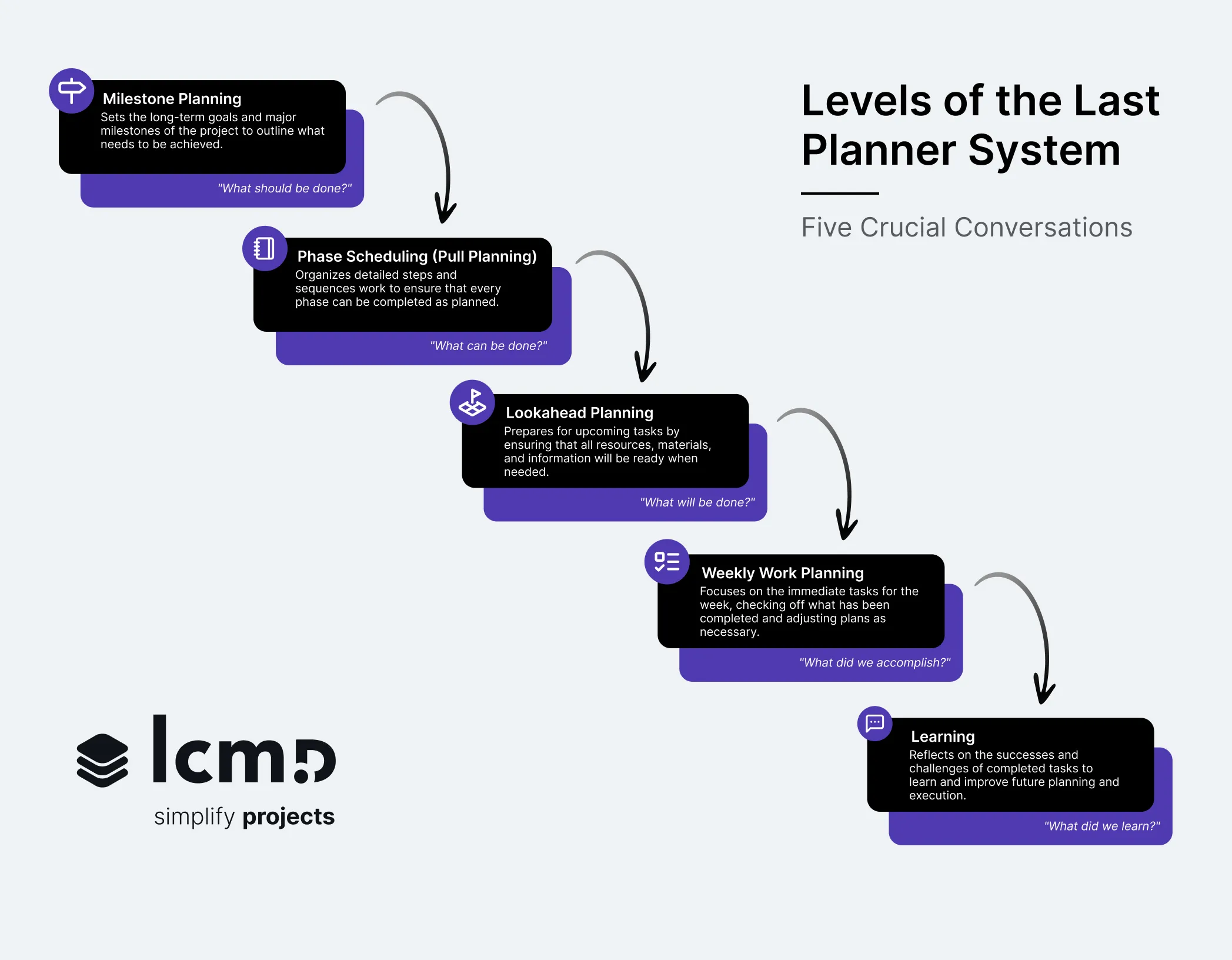
The levels are often described through a sequence of key questions that align with specific action verbs—these verbs help to frame the conversations and actions taken at each level. Here's a simplified explanation of each level with the associated action verbs:
1. Milestone Planning (Should)
"What should be done?"
Sets the long-term goals and major milestones of the project to outline what needs to be achieved.
2. Phase Scheduling (Pull Planning) (Can)
"What can be done?"
Organizes detailed steps and sequences work to ensure that every phase can be completed as planned.
3. Lookahead Planning (Will)
"What will be done?"
Prepares for upcoming tasks by ensuring that all resources, materials, and information will be ready when needed.
4. Weekly Work Planning (Did)
"What did we accomplish?"
Focuses on the immediate tasks for the week, checking off what has been completed and adjusting plans as necessary.
5. Learning (Learn)
"What did we learn?"
Reflects on the successes and challenges of completed tasks to learn and improve future planning and execution.
These verbs—Should, Can, Will, Did, Learn—guide the project team through a structured process of planning and reflection, ensuring that each phase of work is thoughtfully prepared and executed with the opportunity for continuous improvement.
The Advantages of the Last Planner® System
The Last Planner® System offers numerous advantages to construction scheduling efficiency. By utilizing the five conversations and action verbs, project teams can experience improved collaboration, productivity, and overall project success.
Here are the most significant benefits:
- Better Collaboration
- Increased Transparency
- Reduced Waste
- Greater Flexibility
- Faster Project Completion
- Higher Quality Outcomes
- Higher Client Satisfaction
Integrating Lean Construction Software
The Role of Software in Lean Construction
Integrating lean construction software into this system can really up your game. These tools provide critical data visualization, real-time progress tracking, and scenario simulation to aid decision-making throughout the project lifecycle.
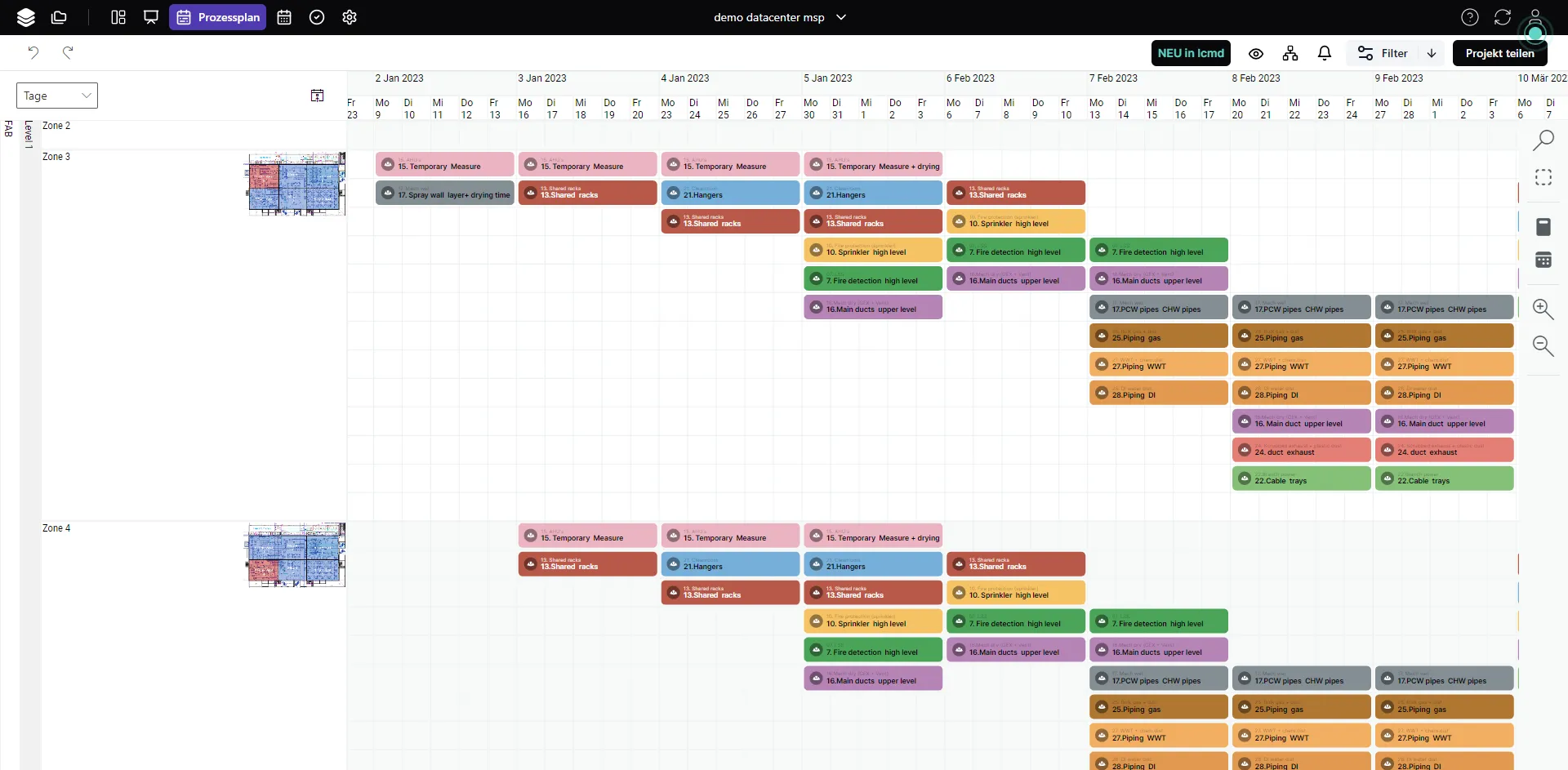
Selecting the Right Lean Construction Software
Choosing the right software is essential. The best lean construction software should offer seamless integration with existing systems, easy collaboration features, and robust analytics to track and improve project efficiency. Get a free consultation today to learn how Lcmd can help you to successfully implement the Last Planner System in your next project.
Conclusion
Implementing the Last Planner System and lean construction principles can profoundly impact the success of construction projects. By focusing on efficiency, collaboration, and continuous improvement, lean construction scheduling prepares projects for success in a competitive industry.