Teile diesen Beitrag:
Die wichtigsten Erkenntnisse aus diesem Artikel:
Lean Management hat die Art und Weise, wie Unternehmen arbeiten, revolutioniert. Ursprünglich aus der Notwendigkeit entstanden, die Effizienz zu maximieren und Verschwendung zu eliminieren, haben sich seine Methoden über ihre Ursprünge hinaus entwickelt und sind heute grundlegend für den Erfolg verschiedener Branchen jenseits der Automobilindustrie, wo sie ihren Ursprung fanden.
Tauchen wir ein in die kurze Geschichte von Lean und sehen wir uns an, wie sich die Lean-Prinzipien von einfachen Effizienzmaßnahmen zu einem umfassenden System entwickelt haben, das weltweit Industrien verändert.
Ursprünge und frühe Einflüsse des Lean Management
Fords Produktionssystem
Im frühen 20. Jahrhundert hat Henry Ford mit seinem Produktionssystem wirklich neue Maßstäbe gesetzt. Du kennst doch die Fließbandfertigung, bei der jeder Arbeiter eine Aufgabe erledigt?
Das Ziel dabei war es, die Automobilproduktion schneller zu machen und Abfall zu reduzieren. Fords Ideen legten viel von dem Grundstein, der später zum Lean Management werden sollte.
Das Toyota Produktionssystem (TPS)
Nach dem Zweiten Weltkrieg war Japan in einer schwierigen Lage – sie mussten ihre Wirtschaft wieder aufbauen und konnten sich keine Verschwendung leisten. Zu dieser Zeit begannen sie, einige von Fords Ideen anzupassen und eigene Innovationen im Qualitätsmanagement einzubringen. Während dieser Zeit wurden die Grundlagen des Toyota Produktionssystems, dem Vorläufer des modernen Lean, geschaffen.
Die Grundlagen von Lean im TPS
Das Toyota Produktionssystem, entwickelt von Taiichi Ohno und seinem Team, ist – wie bereits erwähnt – der Eckpfeiler des Lean Managements; hier haben die modernen Lean-Praktiken ihren Ursprung.
TPS hat die Art und Weise, wie Industrien über Produktion denken, komplett verändert, was zu Verbesserungen führte, die weit über die Automobilproduktion hinausgehen.
Hier sind die wichtigsten Prinzipien des TPS, von denen jedes eine entscheidende Rolle in seinem Erfolg gespielt hat:
- Just-In-Time (JIT): Dieses Prinzip revolutionierte das Bestandsmanagement, indem sichergestellt wurde, dass Teile nur bei Bedarf im Produktionsprozess geliefert werden. Dieser Ansatz reduziert Abfall erheblich und erhöht die betriebliche Effizienz und ist ein grundlegendes Element der Lean-Praktiken.
- Kaizen (Kontinuierliche Verbesserung): Kaizen dreht sich um nie endende Verbesserungen und bezieht alle in der Organisation ein. Es fördert die Einbringung von Ideen zur Effizienz- und Qualitätssteigerung und schafft eine Kultur des proaktiven Problemlösens.
- Jidoka (Automatisierung): Jidoka ermöglicht es Maschinen und Bedienern, Probleme zu erkennen, sobald sie auftreten, und die Produktion zu stoppen, bis die Probleme gelöst sind. Dies stellt sicher, dass Qualität direkt in den Fertigungsprozess integriert wird und verhindert, dass Defekte die Produktionslinie durchlaufen.
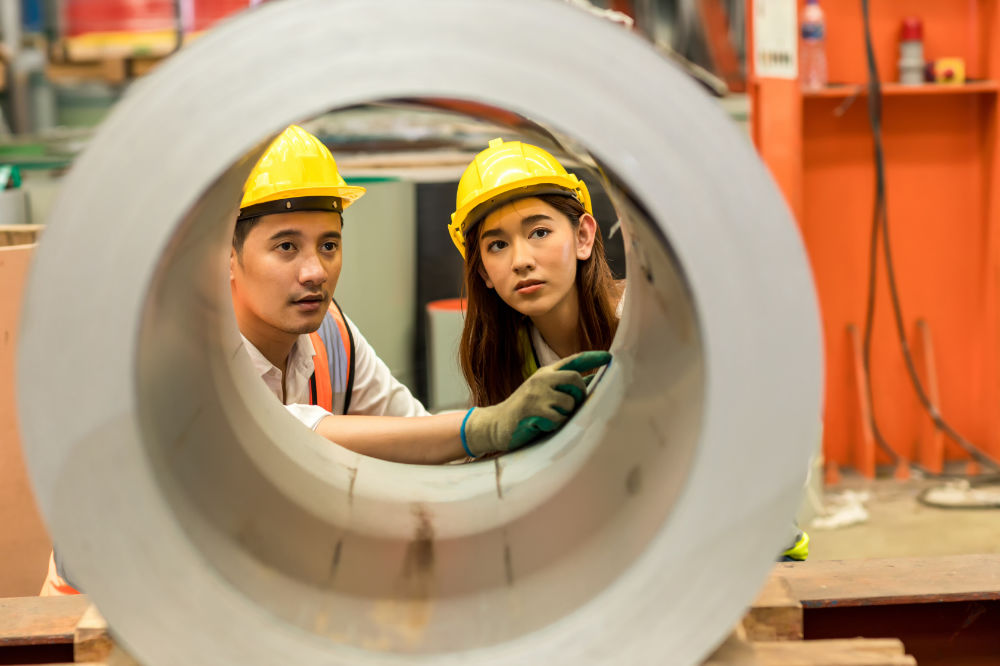
Eiji Toyoda, eine Schlüsselfigur in der Geschichte von Toyota, spielte eine entscheidende Rolle bei der Entwicklung und Implementierung des TPS. Seine Vision von effizienter Produktion half, Toyota als führenden Automobilhersteller zu etablieren. Es bereitete auch den Weg für die breitere Lean-Transformation in verschiedenen Branchen. Unter Toyodas Führung wandte sich Toyota von Massentechniken ab und entwickelte stattdessen Methoden, die später globale Veränderungen in der Fertigung und darüber hinaus inspirieren sollten.
Die Auswirkungen des Toyota Produktionssystems sind tiefgreifend und dauerhaft. Es betont den Respekt vor Menschen, kontinuierliche Verbesserung und den intelligenten Einsatz von Technologie – alles Prinzipien, die in den heutigen schnelllebigen Geschäftsumgebungen von entscheidender Bedeutung bleiben.
Über Toyota hinaus und die globalen Wurzeln des Lean Thinking
Während Toyota viel Anerkennung erhält, gab es auch weltweit andere Bewegungen, die darauf abzielten, die Effizienz zu steigern. Verschiedene Industrien, von der Fertigung in Deutschland bis zum Schiffbau in Schweden, experimentierten lange vor der Prägung des Begriffs "Lean" mit Möglichkeiten zur Rationalisierung von Abläufen.
Diese Bemühungen unterstreichen das universelle Streben nach gesteigerter Produktivität und operativer Exzellenz in verschiedenen Branchen.
Der entscheidende Moment des Lean
Das Konzept des "Lean" selbst wurde offiziell 1988 von John Krafcik eingeführt. In seiner Forschung beschrieb Krafcik die effizienten Praktiken des Toyota Produktionssystems und zeigte, wie es die Ressourcennutzung optimierte und die Betriebszeit im Vergleich zu traditionellen Methoden deutlich reduzierte. Seine Beschreibung markierte einen wichtigen Moment in der Geschichte von Lean und bereitete auch den Weg für seine breitere Anwendung.
Erweiterung der Horizonte von Lean mit Lean Six Sigma
Sobald das Konzept des "Lean" etabliert war, gewann es im Westen schnell an Bedeutung. James P. Womack spielte eine entscheidende Rolle bei seiner Verbreitung mit seinem bahnbrechenden Buch "The Machine That Changed the World," veröffentlicht 1990. In diesem Werk half er, Lean Six Sigma—eine Methodik, die die Effizienz von Lean mit der Qualitätskontrolle von Six Sigma verbindet—zu popularisieren. Ursprünglich in der Fertigung eingesetzt, hat sich Lean Six Sigma mittlerweile auf Dienstleistungsbranchen ausgeweitet und dort die Abläufe erheblich verbessert und die Kundenzufriedenheit gesteigert.
Hier können Sie mehr über das Buch und weitere Lean-Klassiker erfahren.
Lean Thinking durch fünf zentrale Prinzipiendefiniert
James Womack und Daniel Jones hörten nach ihrem ersten Buch nicht auf; sie gingen 1996 mit "Lean Thinking" einen Schritt weiter. Dieses Buch zerlegte Lean wirklich in klare, umsetzbare Prinzipien, die auf jedes Unternehmen angewendet werden können, nicht nur auf Fabriken.
So haben sie diese dargestellt:
- Wert: Identifizieren Sie genau, wofür der Kunde bereit ist zu zahlen. Es geht darum, sich auf das zu konzentrieren, was aus der Sicht des Kunden wirklich Wert schafft.
- Wertstrom: Kartieren Sie jeden Schritt im Prozess zur Lieferung des Produkts oder der Dienstleistung und eliminieren Sie alles, was keinen Wert schafft. Es geht darum, den Prozess von Anfang bis Ende zu optimieren.
- Fluss: Stellen Sie sicher, dass der Arbeitsprozess reibungslos und ohne Unterbrechungen abläuft. Das Ziel ist es, alles effizient von einer Aufgabe zur nächsten zu bewegen.
- Zug: Wechseln Sie zu einem System, bei dem Produkte nur hergestellt werden, wenn es eine Nachfrage vom Kunden gibt. Dies hilft, Verschwendung durch Überproduktion zu vermeiden.
- Perfektion: Verbessern Sie den Prozess immer wieder. Es ist ein nie endendes Streben nach Reduzierung von Verschwendung und Steigerung des Wertes.
Ausweitung und weltweite Übernahme von Lean: Von Autos bis zur Pflege
Es ist faszinierend zu sehen, wie sich Lean Manufacturing, das in Toyotas Werkstätten begann, weit über Autofabriken hinaus verbreitet hat.
Das Set von Lean-Prinzipien hat Lean in einen vielseitigen Ansatz verwandelt, der heute viele Industrien beeinflusst und die Arbeitsweise ganzer Sektoren verändert, indem er Unternehmen weltweit effizienter und reaktionsschneller macht.
Gesundheitswesen
Im Gesundheitswesen hat die Anwendung von Lean Manufacturing die Patientenpflegeprozesse revolutioniert. Durch die Übernahme von Prinzipien wie Just-In-Time-Lieferung von medizinischen Vorräten und Kaizen zur kontinuierlichen Verbesserung der Patientendienste haben Krankenhäuser erhebliche Verbesserungen in der betrieblichen Effizienz und der Kundenzufriedenheit erzielt.
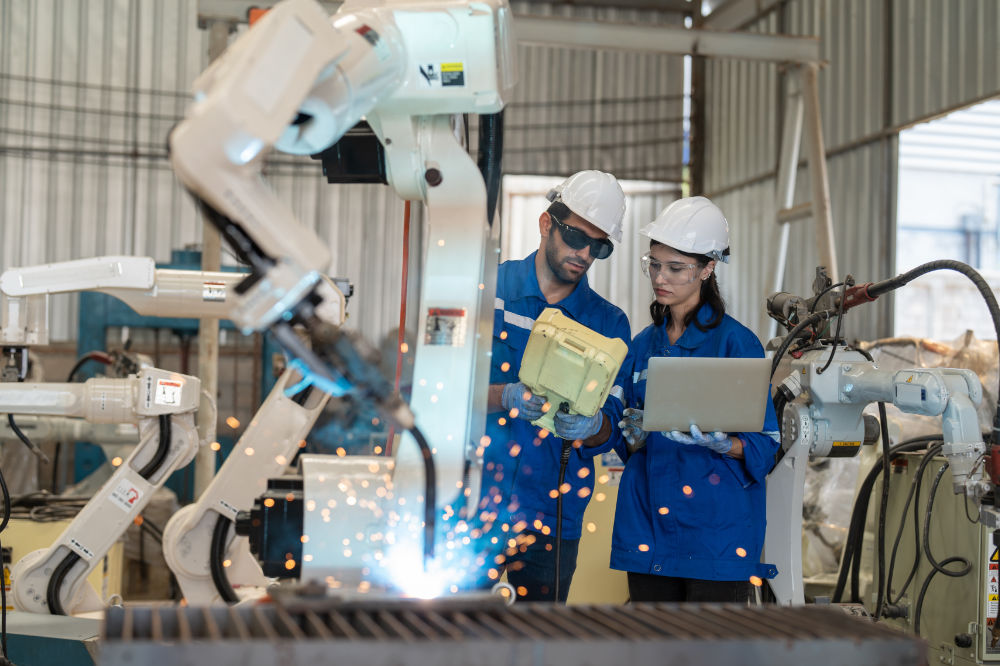
Bauwesen
Die Bauindustrie hat von Lean Manufacturing profitiert, indem sie den Materialabfall reduziert und die Projektzeitpläne optimiert hat. Die Integration von Lean Manufacturing-Praktiken hilft bei der präzisen Planung und Ressourcenzuweisung, was entscheidend für die Verwaltung großer Bauprojekte ist.
Hier erfahren Sie mehr über Lean Construction Management.
Softwareentwicklung
Lean Manufacturing hat nahtlos den Übergang in die Technologiewelt unter den Praktiken der agilen Entwicklung geschafft. Der Schwerpunkt auf Minimierung von Verschwendung und Erhaltung der Flexibilität im Projektmanagement ermöglicht schnelle Iterationen und Reaktionen auf sich ändernde Kundenbedürfnisse.
In diesen Branchen fördert die Lean-Philosophie eine Kultur der kontinuierlichen Verbesserung und des effizienten Ressourcenmanagements. Die Anpassungsfähigkeit der Lean-Prinzipien, wie die Verfeinerung des Herstellungsprozesses und die Integration von visuellen Management-Tools, hat sie in verschiedenen operativen Landschaften unverzichtbar gemacht.
Modernes Lean treibt Effizienz von Robotik bis KI an
Lean-Prinzipien haben sich weiterentwickelt und integrieren nun KI und Robotik, um die Fertigung über traditionelle Methoden hinaus zu verbessern. KI in Lean-Systemen sagt voraus, wann Maschinen gewartet werden müssen, um Ausfallzeiten zu reduzieren, und Robotik übernimmt repetitive Aufgaben, wodurch die Effizienz in den Prozessen gesteigert wird.
Lean-Management-Software transformiert die Art und Weise, wie Unternehmen die Kundennachfrage erfüllen und operative Exzellenz erreichen.
Sie fungiert als zentrale Plattform, die Daten im gesamten Unternehmen sammelt, um Echtzeit-Einblicke zu bieten und Abläufe zu optimieren. Sie hilft bei der Bestandsverwaltung, der Optimierung von Arbeitsabläufen und der Förderung von Verbesserungen, was sie für jedes Unternehmen, das Lean-Prinzipien anwendet, unverzichtbar macht. Diese Integration von Technologie mit Lean sorgt nicht nur dafür, dass alles reibungslos läuft – sie erweitert die Grenzen dessen, was Lean in verschiedenen Branchen leisten kann.
Zukünftige Trends und technologische Integration
Hier ist der Stand der Dinge bei Lean Production und Technologie: Die Mischung aus Lean Thinking und neuen Technologien wie KI und IoT revolutioniert die Art und Weise, wie wir Prozesse verwalten und verbessern.
Stell dir vor: Mit fortschrittlicher Datenanalyse können Unternehmen jetzt Probleme vorhersagen, bevor sie überhaupt auftreten. Dieser prädiktive Ansatz bedeutet eine Verschiebung hin zu einer proaktiveren Prozessverbesserung – eine Strategie, die Probleme im Keim erstickt, bevor sie beginnen.
Lean-Strategie taucht in Bereichen auf, die man nicht erwarten würde, wie z. B. bei der Lean-Softwareentwicklung, bei der es darum geht, die Softwareerstellung schlanker und effizienter zu gestalten und die Entwicklung zu beschleunigen, ohne die Qualität zu opfern.
Während wir voranschreiten, bedeutet die Integration dieser technologischen Werkzeuge mit Lean-Prinzipien, dass Unternehmen nicht nur effizienter, sondern auch anpassungsfähiger und nachhaltiger werden. Es ist eine aufregende Zeit, und Lean steht im Mittelpunkt, was beweist, dass alte Konzepte im modernen Zeitalter neues Leben finden können.
Fazit
Es ist beeindruckend, wie Lean, das ursprünglich zur Verbesserung der Automobilproduktion entwickelt wurde, nun seinen Einfluss auf die Verwaltung von Krankenhäusern, den Bau von Gebäuden und die Entwicklung von Software ausweitet. Lean-Prinzipien wie kontinuierliche Verbesserung und Beseitigung von Verschwendung haben ihre universelle Anwendbarkeit unter Beweis gestellt und die Abläufe in verschiedenen Branchen erheblich verbessert.
Während sich Lean Management weiterentwickelt, erweist es sich nicht nur als unverzichtbar für Qualität und Effizienz, sondern auch für die Förderung nachhaltiger Praktiken in verschiedenen Bereichen. Es ist mehr als nur ein Fertigungs-Upgrade; es ist eine vielseitige und kraftvolle Reihe von Prinzipien, die Organisationen helfen, ihre Abläufe neu zu überdenken und mit weniger mehr zu erreichen, unabhängig von der Branche.
Diese Anpassungsfähigkeit unterstreicht die transformative Kraft der Lean-Prinzipien und macht sie unverzichtbar für jeden Sektor, der darauf abzielt, Prozesse und Ergebnisse in einem sich schnell verändernden Geschäftsumfeld zu verbessern.