Share this article:
Key Takeaways from this article
Lean management has revolutionized the way businesses operate. Originating from a necessity to maximize efficiency and eliminate waste, its methodologies have transcended their origins, becoming fundamental to the success of various industries beyond automotive, where it first took root.
Let’s dive into the brief history of lean and break it down to see how the lean principles evolved from simple efficiency tactics into a comprehensive system transforming industries worldwide.
Origins and Early Influences of Lean Management
Ford’s production system
Back in the early 20th century, Henry Ford really pushed the envelope with his production system. You know, the assembly line where each worker does one thing?
The intention there was all about making car production faster and reducing waste. Ford's ideas laid a lot of the groundwork for what would later become Lean Management.
The Toyota Production System (TPS)
But the story doesn’t stop there. After World War II, Japan was in a tough spot—they needed to rebuild their economy and couldn’t afford to waste anything. That's when they started adapting some of Ford’s ideas and mixed in their own innovations in quality management. It was during this time that the foundations of the Toyota Production System, the precursor to modern Lean, were established.
The Foundations of Lean in the TPS
The Toyota Production System, crafted by Taiichi Ohno and his team, is - as said - the cornerstone of Lean management; it is fundamentally where modern Lean practices began.
TPS completely reshaped how industries think about production, leading to improvements that extend far beyond automotive manufacturing.
Here are the key principles of TPS, each of which has played a pivotal role in its success:
- Just-In-Time (JIT): This principle revolutionized inventory management by ensuring that parts are supplied only as needed in the production process. This approach significantly reduces waste and increases operational efficiency, serving as a foundational element of Lean practices.
- Kaizen (Continuous Improvement): Kaizen is all about never-ending improvements and involves everyone in the organization. It encourages contributions of ideas for efficiency and quality enhancements, fostering a culture of proactive problem-solving.
- Jidoka (Autonomation): Jidoka allows machines and operators to detect issues as they arise and to halt production until the issues are resolved. This ensures that quality is built directly into the manufacturing process, preventing defects from being passed along the production line.
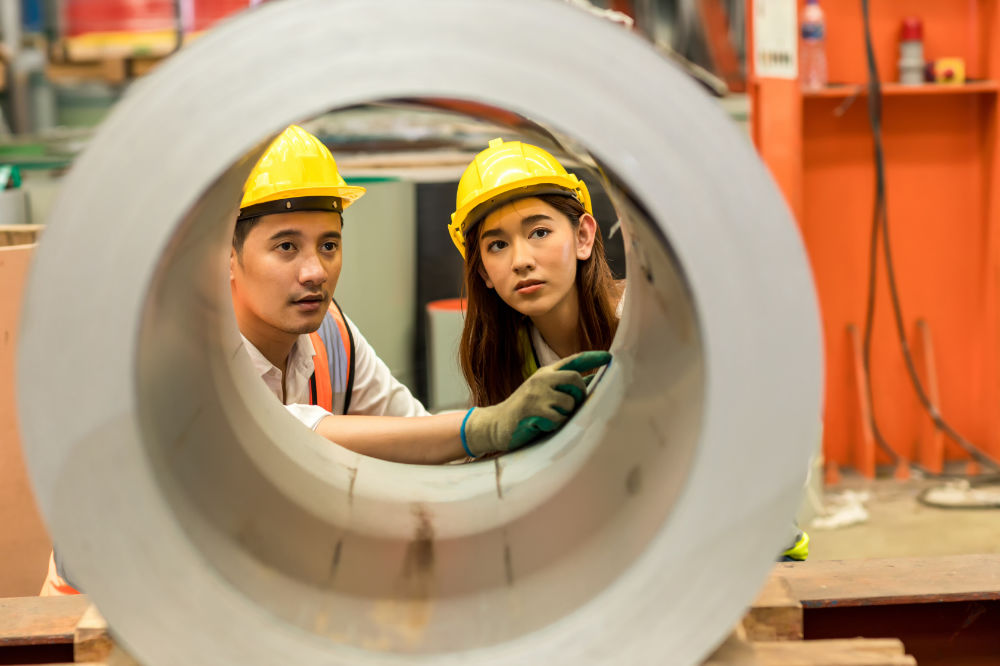
Eiji Toyoda, a key figure in Toyota's history, played a crucial role in the development and implementation of TPS. His vision for efficient production helped establish Toyota as a leading automotive manufacturer. It also set the stage for the broader Lean transformation across industries. Under Toyoda`s guidance, Toyota shifted away from mass production techniques, instead pioneering methods that would later inspire global changes in manufacturing and beyond.
The impact of the Toyota Production System remains profound and lasting. It emphasizes respect for people, continuous improvement, and the intelligent use of technology—all principles that remain vital in today’s fast-paced business environments.
Beyond Toyota and the Global Roots of Lean Thinking
While Toyota gets a lot of the credit, there were also other movements around the world aiming to increase efficiency. Various industries, from manufacturing in Germany to shipbuilding in Sweden, were all playing around with ways to streamline operations long before the term "Lean" was ever coined.
These efforts highlight the universal pursuit of enhanced productivity and operational excellence across diverse industries.
The Defining Moment of Lean
The concept of "Lean" itself was officially introduced by John Krafcik in 1988. In his research, Krafcik detailed the efficient practices of the Toyota Production System, showing how it optimized resource use and reduced operational time significantly compared to traditional methods. His description marked an important moment in the history of Lean. It also set the stage for its broader application.
Broadening Lean's Horizons with Lean Six Sigma
Once the concept of "Lean" was established, it quickly gained traction in the West. James P. Womack played a critical role in its adoption with his seminal book "The Machine That Changed the World," published in 1990. In this work, he helped popularize Lean Six Sigma—a methodology that blends Lean's efficiency with Six Sigma's quality control. Initially utilized in manufacturing, Lean Six Sigma has since expanded into service industries, significantly boosting operations and increasing customer satisfaction.
You can learn more about this book and other lean bestsellers here.
Lean Thinking Defined Through Five Key Principles
James Womack and Daniel Jones didn’t stop with their first book; they took Lean a step further in 1996 with "Lean Thinking." This book really broke down Lean into clear, actionable principles that could apply to any business, not just factories.
Here’s how they laid it out:
- Value: Identify exactly what the customer is willing to pay for. It’s all about focusing on what truly adds value from the customer's perspective.
- Value Stream: Map out every step in the process to deliver the product or service, and then weed out anything that doesn’t add value. It’s about streamlining the process from start to finish.
- Flow: Make sure the work process flows smoothly with no interruptions. The goal here is to ensure everything moves efficiently from one task to the next.
- Pull: Switch to a system where products are only made when there is a demand from the customer. This helps eliminate waste from overproduction.
- Perfection: Keep refining and improving the process over and over again. It’s a never-ending pursuit of reducing waste and enhancing value.
Expansion and World-Wide Adoption of Lean: From Cars to Care
It's fascinating to see how Lean Manufacturing, which started in Toyota’s workshops, has spread far and wide beyond car factories.
The set of lean principles helped turn Lean into a versatile approach that’s now influencing many industries and it`s reshaping how entire sectors operate, making businesses more efficient and responsive across the globe.
Healthcare
In healthcare, applying Lean Manufacturing has revolutionized patient care processes. By adopting principles such as Just-In-Time delivery of medical supplies and Kaizen for continuous improvement in patient services, hospitals have seen substantial improvements in operational efficiency and customer satisfaction.
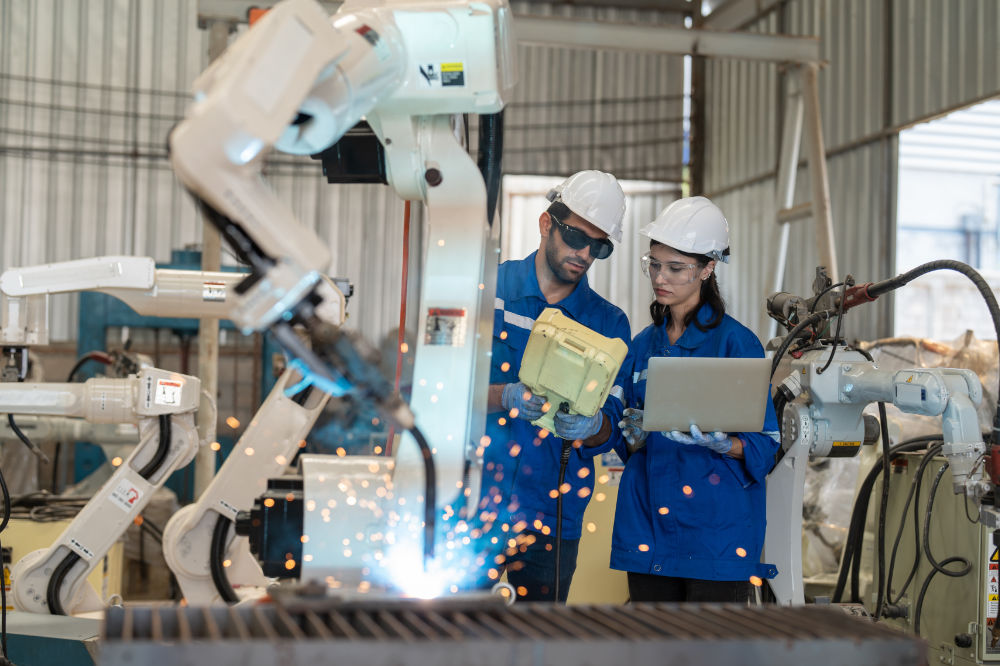
Construction
The construction industry has benefited from Lean Manufacturing by reducing material waste and optimizing project timelines. Incorporating Lean Manufacturing practices helps in precise planning and resource allocation, which are crucial for managing large-scale construction projects.
Here you can learn more about Lean Construction Management.
Software Development
Lean Manufacturing has seamlessly transitioned into the tech world under Agile development practices. The emphasis on minimizing waste and maintaining flexibility in project management allows for rapid iteration and response to changing customer needs.
Across these industries, the Lean philosophy encourages a culture of continuous improvement and efficient resource management. The adaptability of Lean principles, such as refining the manufacturing process and integrating visual management tools, has made them invaluable across diverse operational landscapes.
Modern Lean Driving Efficiency from Robotics to AI
Lean principles have evolved, now integrating AI and robotics to enhance manufacturing beyond the traditional. AI in Lean systems predicts when machines need maintenance to reduce downtime, and robotics handle repetitive tasks, boosting efficiency in the processes.
Lean management software is transforming how businesses meet customer demand and achieve operational excellence.
It acts like a central hub, pulling in data across the business to offer real-time insights and streamline operations. It helps manage inventory, optimize workflows, and drive improvements, making it essential for any business applying Lean principles. This integration of technology with Lean isn't just keeping things running smoothly—it's pushing the boundaries of what Lean can do across industries.
{{cta}}
Future Trends and Technological Integration
So, here's where things are heading with Lean production and tech: The mix of Lean thinking and new technologies like AI and IoT is revolutionizing how we manage and improve processes.
Think about this: with advanced data analytics, companies can now predict problems before they even happen. This predictive approach means a shift toward more proactive process improvement—It’s a proactive strategy that stops problems in their tracks before they begin.
Lean strategy is popping into areas you wouldn't expect, like lean software development, where it’s all about making software creation leaner and meaner, speeding up development without sacrificing quality.
As we move forward, the integration of these tech tools with Lean principles means that businesses will not only become more efficient but also more adaptable and sustainable. It's an exciting time, and Lean is right at the heart of it, proving that old concepts can find new life in the modern world.
Conslusion
It’s impressive how Lean, initially designed to improve car production, now extends its influence to managing hospitals, constructing buildings, and developing software. Lean principles, such as continuous improvement and eliminating waste, have demonstrated their universal applicability, significantly enhancing operations across various industries.
As Lean management continues to evolve, it keeps proving itself as indispensable, not just for quality and efficiency but also for promoting sustainable practices across different fields. It has become more than a manufacturing upgrade; it is a versatile and powerful set of principles that helps organizations rethink operations and do more with less, no matter the industry.
This adaptability underscores the transformative power of Lean principles, making them essential for any sector aiming to improve processes and outcomes in a rapidly changing business landscape.