Share this article:
Key Takeaways from this article
How can tweaking little things in your daily workflow make a difference in your performance? As you know, small changes sometimes make a huge difference. Now, imagine this impact on a bigger scale!
With Kaizen, every little change counts; each step, no matter how small, leads to significant gains. These daily adjustments smooth out operations and drive significant business growth through constant innovation.
Ready to see how? Let's dive into the core principles of Kaizen and and their practical applications.
What is Kaizen
Kaizen is a smart blend of ongoing action and deep-seated philosophy centred on continuous improvement. It's about making small, consistent changes that, bit by bit, optimize business processes and improve productivity.
What's truly compelling about Kaizen is its focus on standardized work and the potential for improvement in every process. Why is this approach so effective?
It's because Kaizen's core values go beyond simply cutting costs. It emphasizes daily tasks, aiming to improve productivity across various aspects of an organization’s operations and the overall work environment. Kaizen involves everyone in the organization—from the ground up—to make sure that every aspect of the production process is optimized for minimal waste and maximum value.
Originating in Japanese companies, particularly within the Toyota Production System, Kaizen has become a global standard in lean manufacturing.#
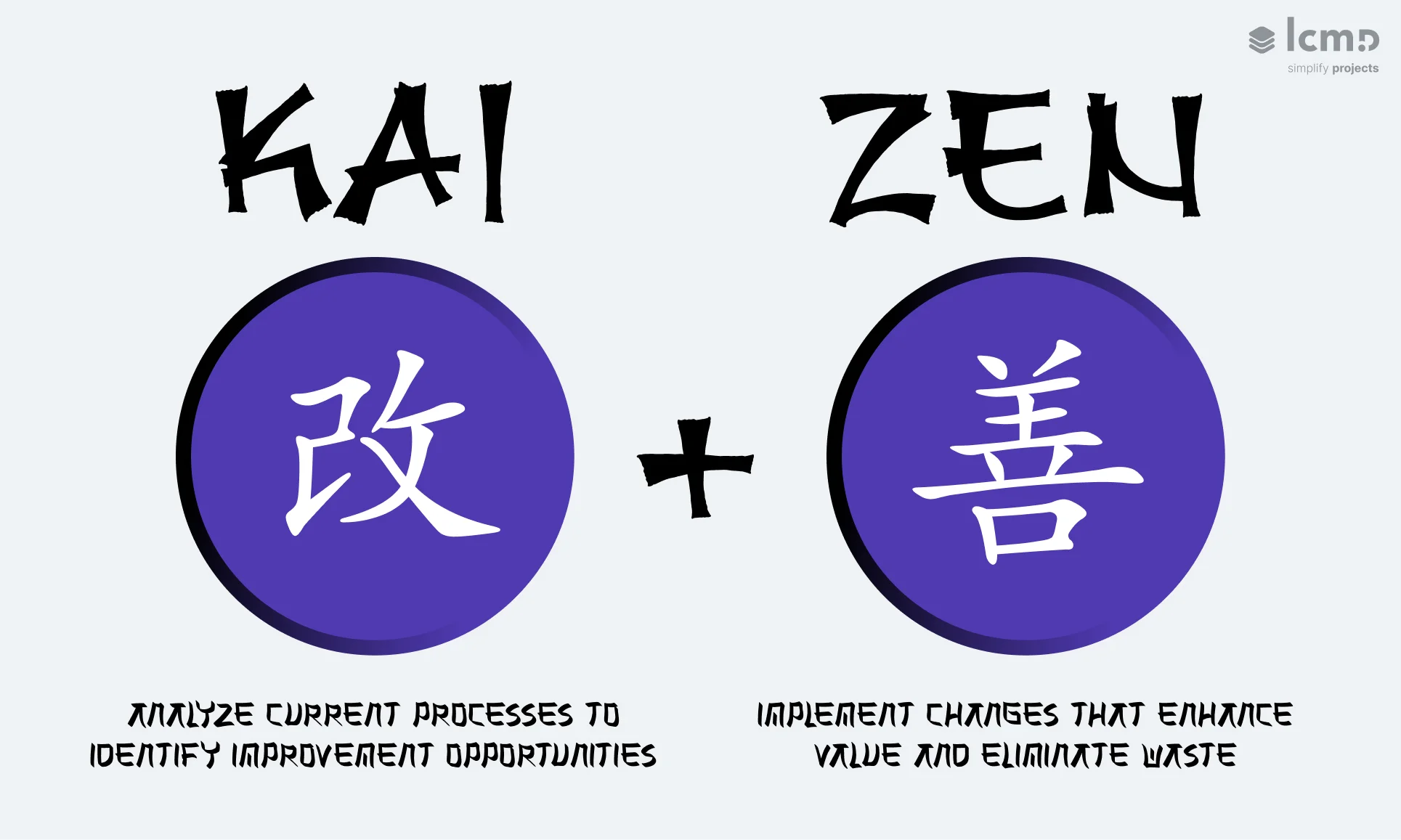
How Does Kaizen Work - 5 Kaizen Principles
How Kaizen turns small changes into big gains? It operates on five foundational principles, each designed to secure that improvements are sustainable and impactful.
1. Know Your Customer
Who are you improving for? Kaizen says keep your customer at the heart of improvements.
2. Let It Flow
Ever hit a bottleneck at work? Kaizen aims to smooth out those kinks in the production process, making everything run smoother, from raw materials to final products. It’s about creating a steady flow that enhances productivity.
3. Go to Gemba
This means hitting the front lines where the real work happens. Kaizen encourages managers and team leaders to get directly involved, see the challenges firsthand, and work on practical improvements.
4. Empower People
Got an idea? Kaizen wants to hear it. This principle is about giving employees the power to suggest changes that could make a big difference. It’s about fostering an environment where every employee feels they can contribute to the company’s success.
5. Be Transparent
Sharing is caring, especially in Kaizen. Transparency in management and communicationensures everyone is on the same page, which makes implementing new ideas and spotting areas for potential improvement much easier.
Using these principles, Kaizen shifts from being a mere tool to a way of life at work that helps identify areas for improvement, reduce waste, and increase efficiency—all while keeping the team informed and involved. How could these principles transform your workplace?
Application of Kaizen
Without standards, there can be no improvement. Kaizen means taking small steps toward improvement, standardizing those improvements, and then taking another small step.
Taiichi Ohno
5S Method
The 5S method is a cornerstone of the kaizen methodology and ultimately contributes to improve operational performance.
It is a structured program, which consists of five steps to systematically achieve total organization, cleanliness, and standardization in the workplace. Here’s a breakdown of each stage:
- Sort (Seiri): Remove unnecessary items.
- Set in Order (Seiton): Organize necessary items.
- Shine (Seiso): Clean the workplace.
- Standardize (Seiketsu): Standardize the best practices.
- Sustain (Shitsuke): Maintain and review standards.
The Role of Kaizen Event in Sustained Continuous Improvement
A Kaizen Blitz, also known as a Kaizen Event, is an intensive, short-term project that aims to quickly improve a specific area within an organization. It encapsulates the principles of Kaizen—continuous improvement—by rapidly implementing changes and achieving significant results.
Key Features of a Kaizen Event
- It has a short duration - typically conducted over a few days to a week.
- Targets specific process or areas for improvement.
- Involves a cross-functional team working intensively together.
- Aims to produce visible outcomes quickly to motivate and demonstrate the benefits of Kaizen principles.
Kaizen Event and the PDCA Cycles
Kaizen events are integral to the Plan-Do-Check-Act (PDCA) cycle, which ensures that changes are effective and lead to real improvements. This standardized work approach doesn't just optimize projects—it enhances the flow of resources, quality of kaizen process and strengthens overall business operations.
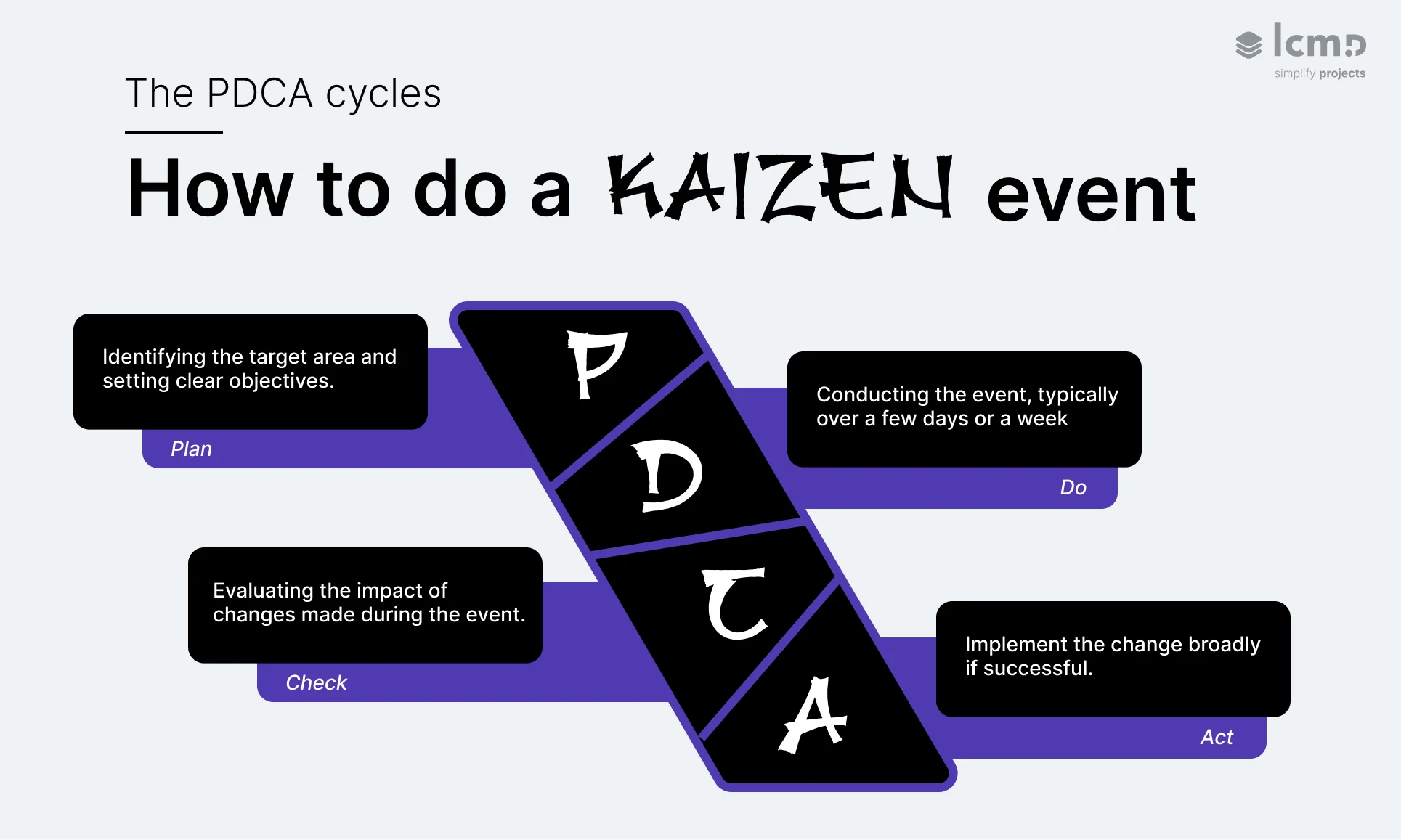
Plan-Do-Check-Act (PDCA) cycle
The Plan-Do-Check-Act (PDCA) cycle is vital in embedding continuous improvement within the Kaizen framework:
- Plan: Identifying the target area and setting clear objectives.
- Do: Conducting the event, typically over a few days, where the team collaboratively identifies issues and implements solutions.
- Check: Evaluating the impact of changes made during the event.
- Act: Implement the change broadly if successful.
This cyclical process ensures that improvements are continually being made and sustained, promoting a culture of perpetual refinement and enhancement in the work environment.
7M + 7W Checklist
The 7M and 7W checklists are key tools in Kaizen, used to scrutinize and optimiize manufacturing process. By using these checklists, organizations can identify areas for potential improvement and sustain the Kaizen philosophy of ongoing development and refinement across all operations.
7M Checklist: Analyzing Key Factors in Manufacturing Processes
- Materials
- Machines
- Methods
- Manpower
- Measurement
- Mother-nature (Environment)
- Management
7W Checklist: A Framework for Thorough Process Examination
- What is to be done?
- Why is this process necessary?
- Where should the process take place?
- When should each step occur?
- Who is responsible for each task?
- Which resources are required?
- How will the process be executed effectively?
Kaizen and Just in Time
Just-in-Time (JIT) manufacturing naturally aligns with Kaizen by reducing inventory levels and minimizing waste. In Just-in-Time approach, materials and components are ordered and received only when needed, preventing excess and reducing storage costs. The synergy between Just-in-Time and Kaizen supports productivity by streamlining operations and focusing resources where they are most effective.
By integrating Just-in-Time with Kaizen, organizations can further reduce waste and enhance their overall operational effectiveness, focusing on continuous improvement in every stage of their business processes.
These principles and tools collectively underscore Kaizen’s pivotal role in driving perpetual growth and efficiency in organizations worldwide.
Implementing Kaizen with Lcmd in Lean Construction
Kaizen's principles of continuous improvement and waste reduction align perfectly with lean construction practices. Lcmd enhances these principles through digital tools, making Kaizen more accessible and effective in construction projects.
Real-Time Feedback for Continuous Improvement
Lcmd enables live-time feedback and communication, involving the entire team in the process of continuous improvement. This aligns with Kaizen's emphasis on employee engagement and the "Go to Gemba" principle, allowing for immediate identification and resolution of issues.
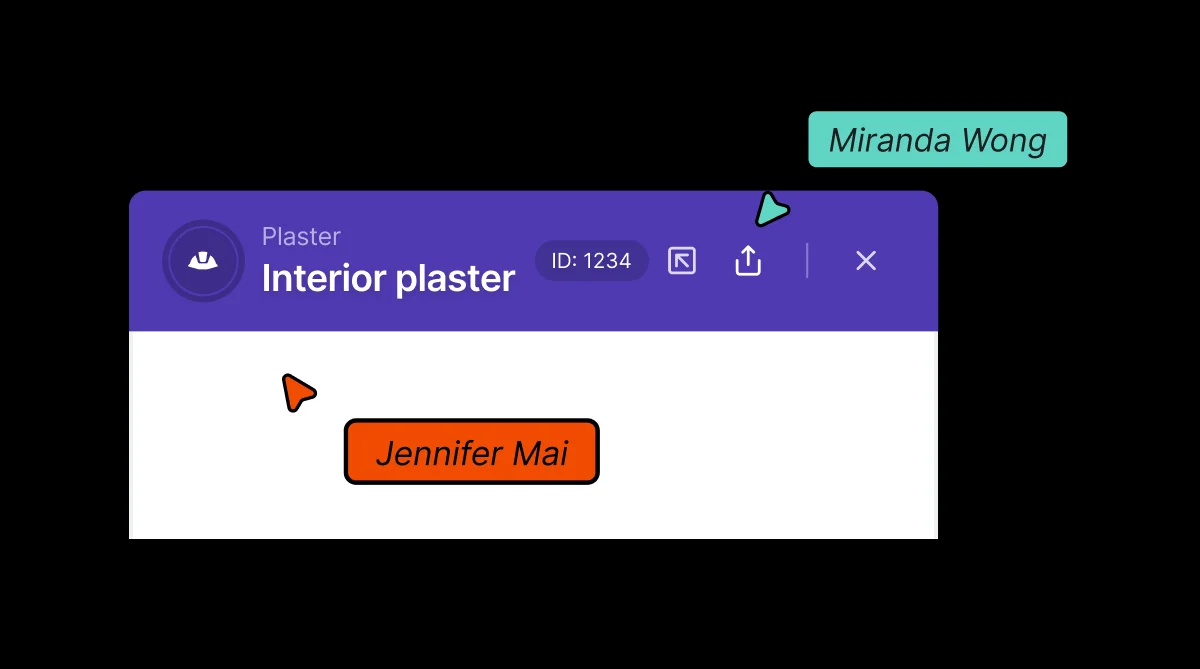
Proactive Problem Solving
By identifying interference reasons through dashboard analysis, Lcmd supports Kaizen's focus on root cause analysis. This feature allows teams to make small, incremental changes to avoid future issues, embodying the essence of Kaizen's continuous improvement cycle.
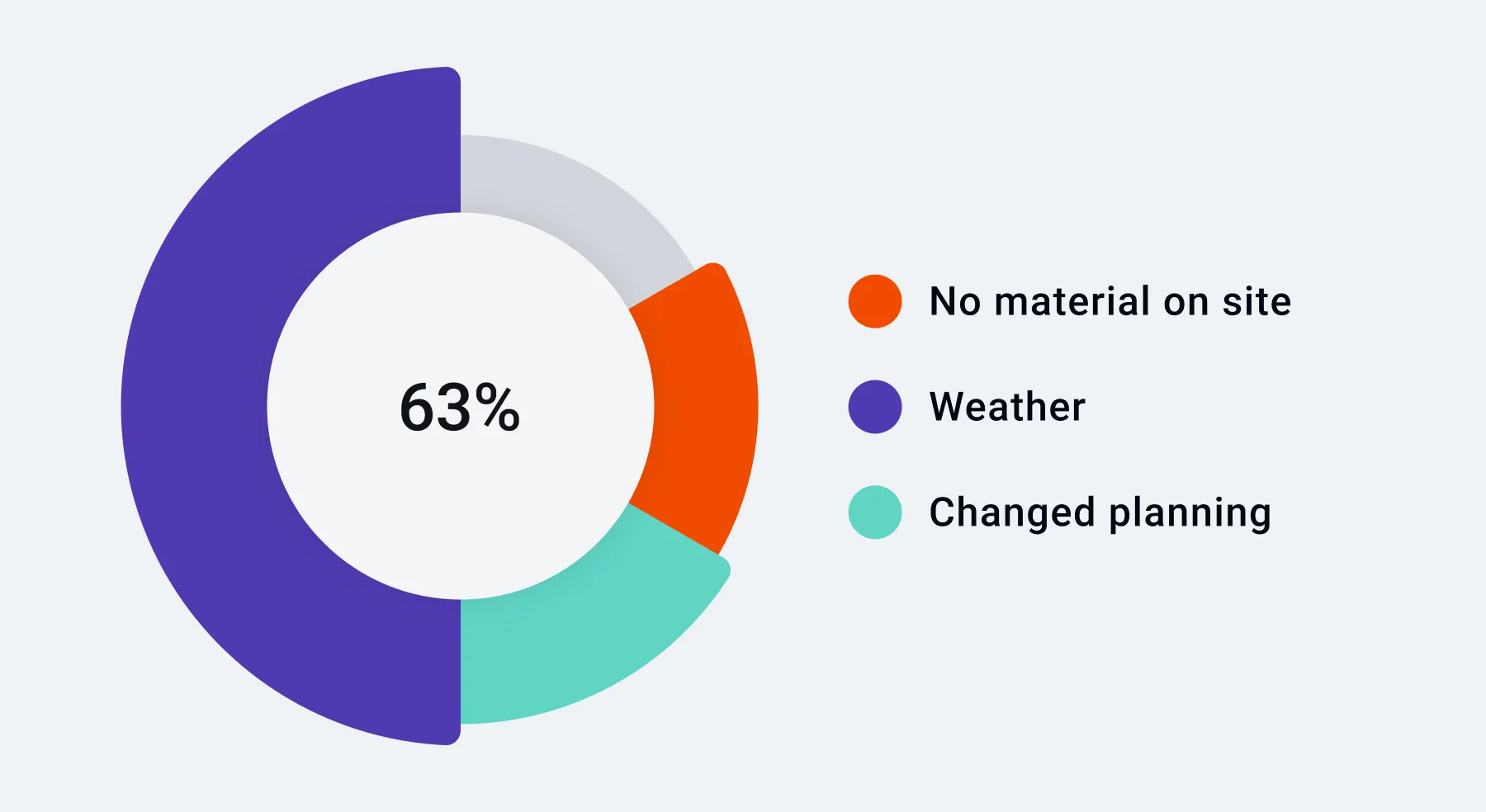
Standardization and Process Optimization
Lcmd's real-time task status monitoring facilitates standardization of work processes, a key aspect of Kaizen. It allows teams to quickly identify deviations from standard procedures and make necessary adjustments, promoting efficiency and reducing waste.
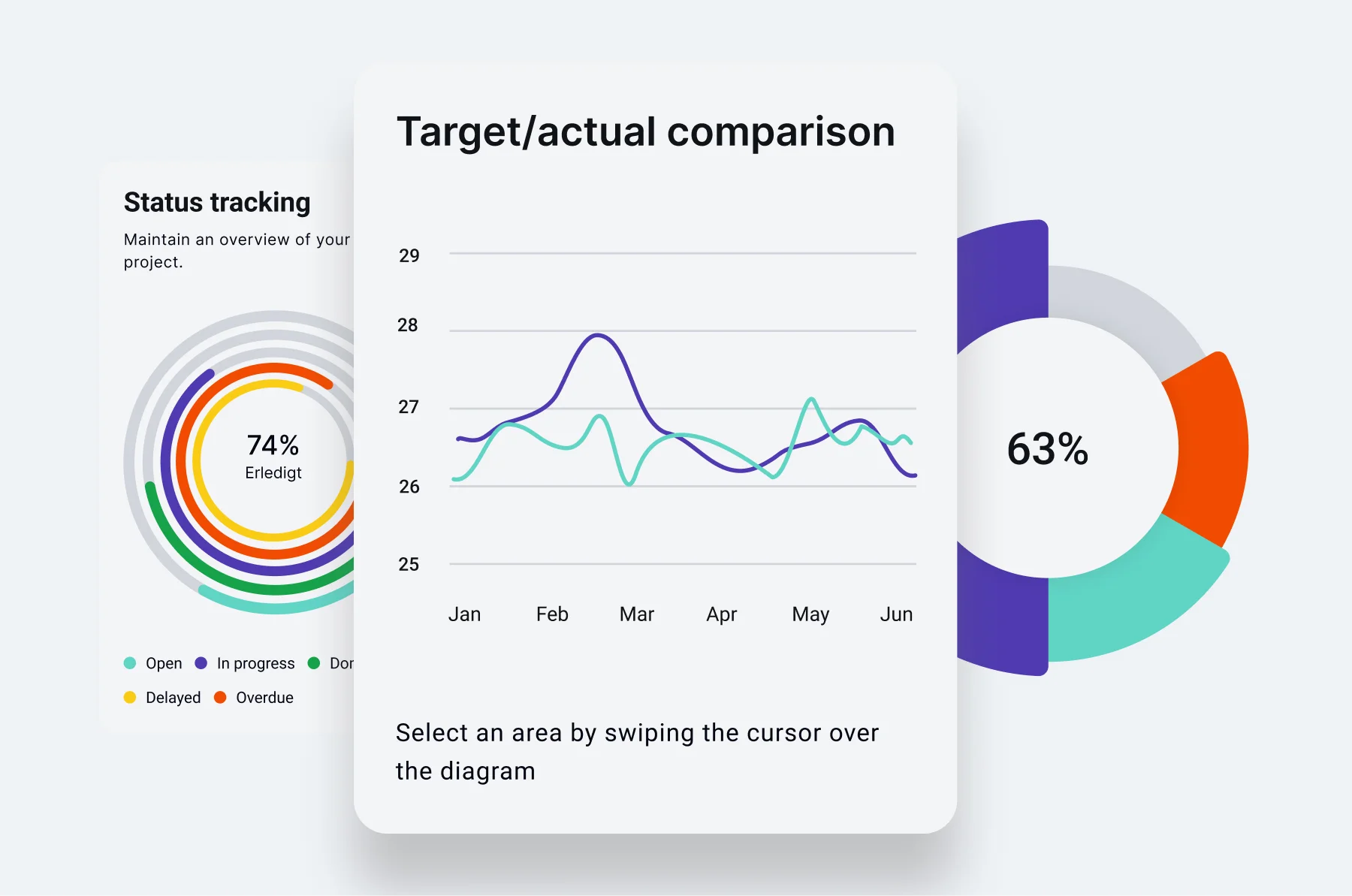
By integrating Lcmd into your lean construction practices, you can create a digital Kaizen environment, where continuous improvement becomes an integral part of your project management approach.
{{cta}}
Conclusion
Kaizen means improvement. Moreover, it means continuing improvement in personal life, home life, social life, and working life. When applied to the workplace, Kaizen means continuing improvement involving everyone – managers and workers alike.
Masaaki Imai
Kaizen, which embodies the art of continuous improvement, marries philosophy with practical action. It involves every level of an organization in small, incremental changes aimed at enhancing processes and overall efficiency.
The kaizen philosophy encourages a workplace culture where every employee is engaged in suggesting and implementing improvements, making it a holistic approach to business growth.
Kaizen is not merely a method; it's a way of life that integrates continuous improvement into the fabric of an organization’s culture, empowering employees to contribute to the company's success.
How could small changes drive major success in your own projects or work environment?