Share this article:
Key Takeaways from this article
- The PDCA cycle consists of four phases: Plan (analysis & goal definition), Do (implementation), Check (result evaluation), and Act (standardization & improvement).
- 85% of process improvements fail because companies stop at "Plan" and "Do" and neglect the crucial phases "Check" and "Act."
- Successful PDCA application begins with data-based problem analysis and measurable goals in the Plan phase, followed by controlled implementation on a smaller scale.
- The Check phase requires objective evaluation based on measurable criteria, while in the Act phase, successful solutions must be established as new standards.
- PDCA differs from more complex methods like Six Sigma through its simple applicability and universal usability in different management areas.
- Typical pitfalls include superficial problem analysis, skipping the Check phase, and lack of standardization of successful solutions.
- Each PDCA phase is supported by specific tools: Pareto analyses (Plan), Gantt charts (Do), KPI dashboards (Check), and A3 reports (Act).
- Companies that consistently apply the PDCA cycle achieve measurable results such as reduced error rates and significant cost savings.
Why 85% of Process Improvements Fail — and How the PDCA Cycle Changes That
Have you ever wondered why some companies seemingly achieve continuous improvements effortlessly, while others remain stuck in a cycle of recurring problems despite their best efforts? The surprising answer lies not in more expensive tools or additional resources—but in the systematic application of a principle that is equally simple and profound.
The PDCA cycle separates successful lean initiatives from short-lived improvement programs. While most organizations stop at "Plan" and "Do," true process champions make the crucial leap to "Check" and "Act"—fundamentally changing how optimization works.
What if your management decisions were based not on assumptions, but on verified data? What if each process improvement wasn't just a one-time event, but laid the foundation for the next?
Let's take a fresh look at this powerful concept—one that could fundamentally transform your approach to leadership and process optimization.
PDCA Cycle: The Key to Continuous Improvement in Management
What makes the PDCA cycle so valuable for modern leaders?
The PDCA cycle has established itself as one of the most effective methods for process improvement in quality management. What appears simple at first glance—Plan, Do, Check, Act—offers a robust framework for continuous optimization in practice.
As a leader regularly dealing with process improvements, you know the challenge: How can problems not only be solved but also sustainably prevented? This is exactly where the PDCA cycle comes in.
The approach helps you:
- Analyze problems in a structured way instead of just treating symptoms
- Make decisions based on concrete data rather than assumptions
- Actually measure the effectiveness of improvement measures
- Standardize and anchor successful approaches
Let's take a closer look at the four phases and how you can implement them in your daily leadership routine.
The Four Phases of the PDCA Cycle: Explained Practically
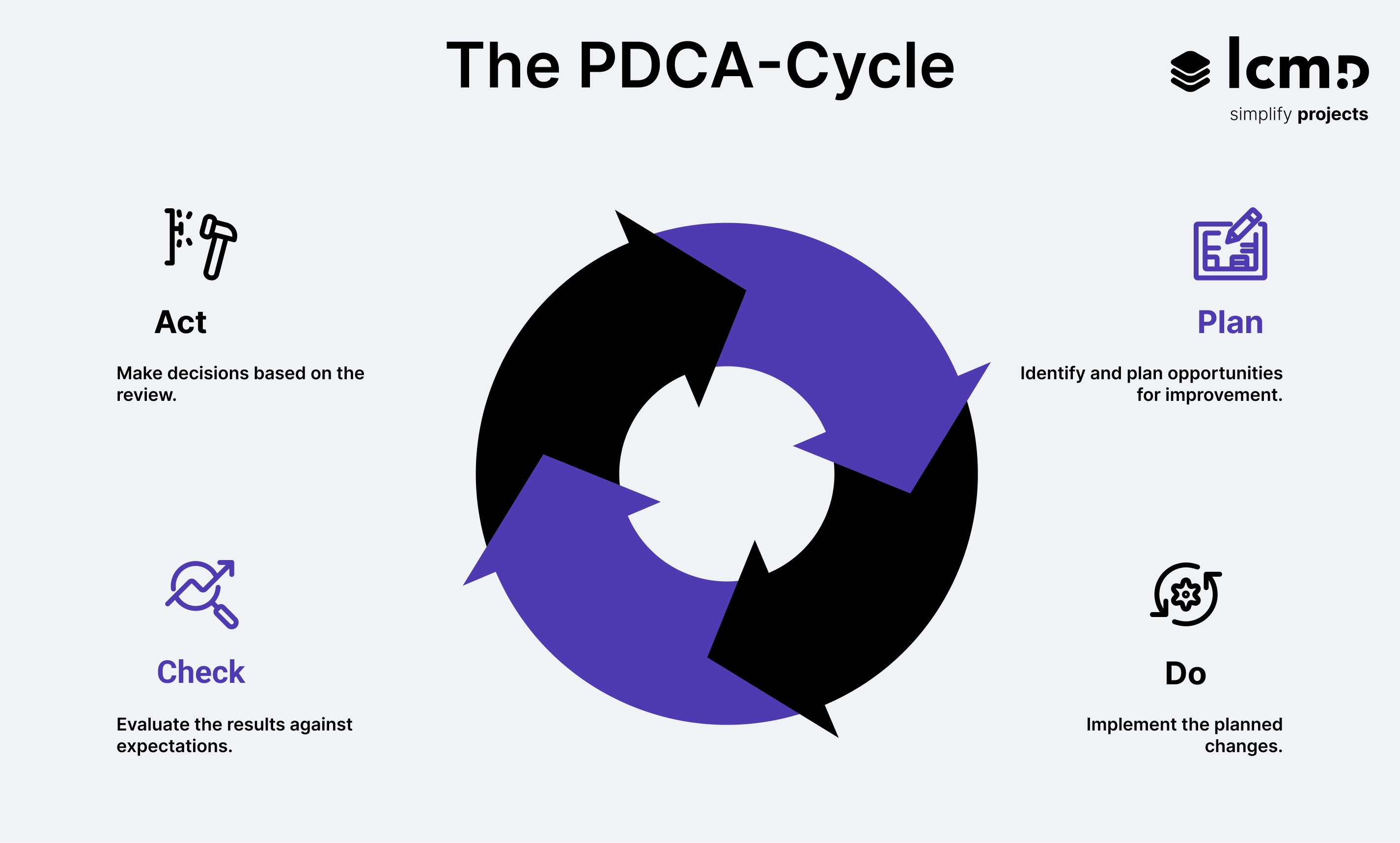
1. Plan: The Foundation of Every Successful Change
The planning phase is more than just setting a goal. It includes a thorough analysis of the current state and the causes of problems or inefficiencies.
Ask yourself the following questions:
- What exactly isn't working optimally? (Define the problem precisely)
- What data proves the problem exists? (Collect facts)
- What are the root causes? (Use analysis tools like 5-Why or Ishikawa diagrams)
- What specific, measurable goals do you want to achieve?
- What measures could achieve these goals?
The temptation to shorten this phase and quickly implement solutions is strong. Resist this impulse. Thorough planning saves time and resources in later phases.
Practical tip: Document your assumptions. You'll come back to them in the Check phase and see if your hypotheses were correct.
2. Do: From Theory to Practice
The implementation phase is about realizing the planned measures—but with care.
Proven approaches:
- First test solutions on a small scale
- Thoroughly train affected employees
- Document every step of the implementation
- Continuously collect data on effectiveness
Especially important: Stick to your plan, but remain flexible enough to respond to unforeseen challenges.
Practical tip: Establish short, regular status meetings during the implementation phase. This allows you to course-correct early if something isn't working as expected.
3. Check: The Often Underestimated Success Factor
The checking phase distinguishes the PDCA cycle from many other improvement approaches. Here, you deliberately take time to objectively evaluate the results.
Ask critical questions:
- Were the desired goals achieved? (Data analysis)
- If not, why not? (Deviation analysis)
- Were there unexpected effects—positive or negative?
- What have we learned from the implementation?
This phase requires intellectual honesty. It's not about confirming the success of the measures, but understanding their actual effectiveness.
Practical tip: Visualize your results. Graphical representations often make trends and connections more clearly visible than pure numerical tables.
4. Act: From Insight to Standardization
The final phase closes the cycle—and simultaneously opens it for the next iteration. Here, two central questions matter:
- How do we permanently anchor successful improvements in the system?
- What further optimizations make sense next?
Concrete steps in this phase:
- Transfer successful solutions into standards
- Document and communicate these standards
- Train employees in the new standards
- Define metrics to monitor compliance
- Initiate the next PDCA cycle
Practical tip: Celebrate successes and acknowledge the contribution of everyone involved. This strengthens motivation for future improvement initiatives.
PDCA in the Context of Other Management Methods
Why should you prefer PDCA to other methods? The following overview helps you understand the strengths and application areas of different approaches:
The PDCA cycle often forms the foundation for other methods or can be combined with them. Six Sigma, for example, uses the DMAIC cycle, which is an extension of the PDCA principle.
Practical Application of the PDCA Cycle: Role-Specific Approaches
For C-Level Executives
As a leader at the highest level, your role is less about direct application and more about creating the right framework conditions:
- Make PDCA part of the corporate strategy
- Provide the necessary resources
- Require regular PDCA reviews at the management level
- Honor data-based decision-making
- Lead by example by applying PDCA principles yourself
In management meetings, ask not only about results but also about the process: "What data led to this decision?" or "What did we learn from the last cycle?"
For Middle Management
As a department or team leader, you are the pivot point for practical PDCA application:
- Identify suitable processes for PDCA cycles
- Form cross-functional teams for improvement projects
- Ensure documentation and sharing of insights
- Integrate PDCA into regular team meetings
- Train your employees in the basics of the method
Tip: Start with a manageable pilot project that can show results relatively quickly. Nothing convinces more than visible results.
For Lean Experts and Process Owners
As a specialist in process improvement, you have a supporting and advisory role:
- Develop application-specific PDCA tools and templates
- Coach teams in applying the method
- Help select appropriate metrics
- Support complex root cause analyses
- Facilitate knowledge transfer between different teams
Your task is to make the application of PDCA as simple and effective as possible so that the method becomes second nature.
Typical Pitfalls in the PDCA Cycle — and How to Avoid Them
The most common problems in PDCA application arise from impatience or insufficient analysis. Do you recognize these situations?
Problem 1: Superficial Problem Analysis
Symptom: Problems keep recurring despite supposed "solutions."
Solution: Invest more time in root cause analysis. Ask "Why?" at least five times to get to the fundamental causes.
Problem 2: Skipping the Check Phase
Symptom: Measures are implemented, but their effectiveness isn't systematically verified.
Solution: Plan the Check phase from the beginning with specific dates and responsibilities.
Problem 3: No Standardization of Successful Solutions
Symptom: The same improvements are repeatedly "reinvented."
Solution: Document successful solutions as standards and ensure their compliance.
Problem 4: Projects Too Large or Too Vague
Symptom: PDCA projects drag on endlessly or lose focus.
Solution: Divide large improvement initiatives into smaller, clearly defined PDCA cycles.
Problem 5: Lack of Data Foundation
Symptom: Decisions continue to be based on assumptions rather than facts.
Solution: Define at the beginning of the cycle what data is required and how it will be collected.
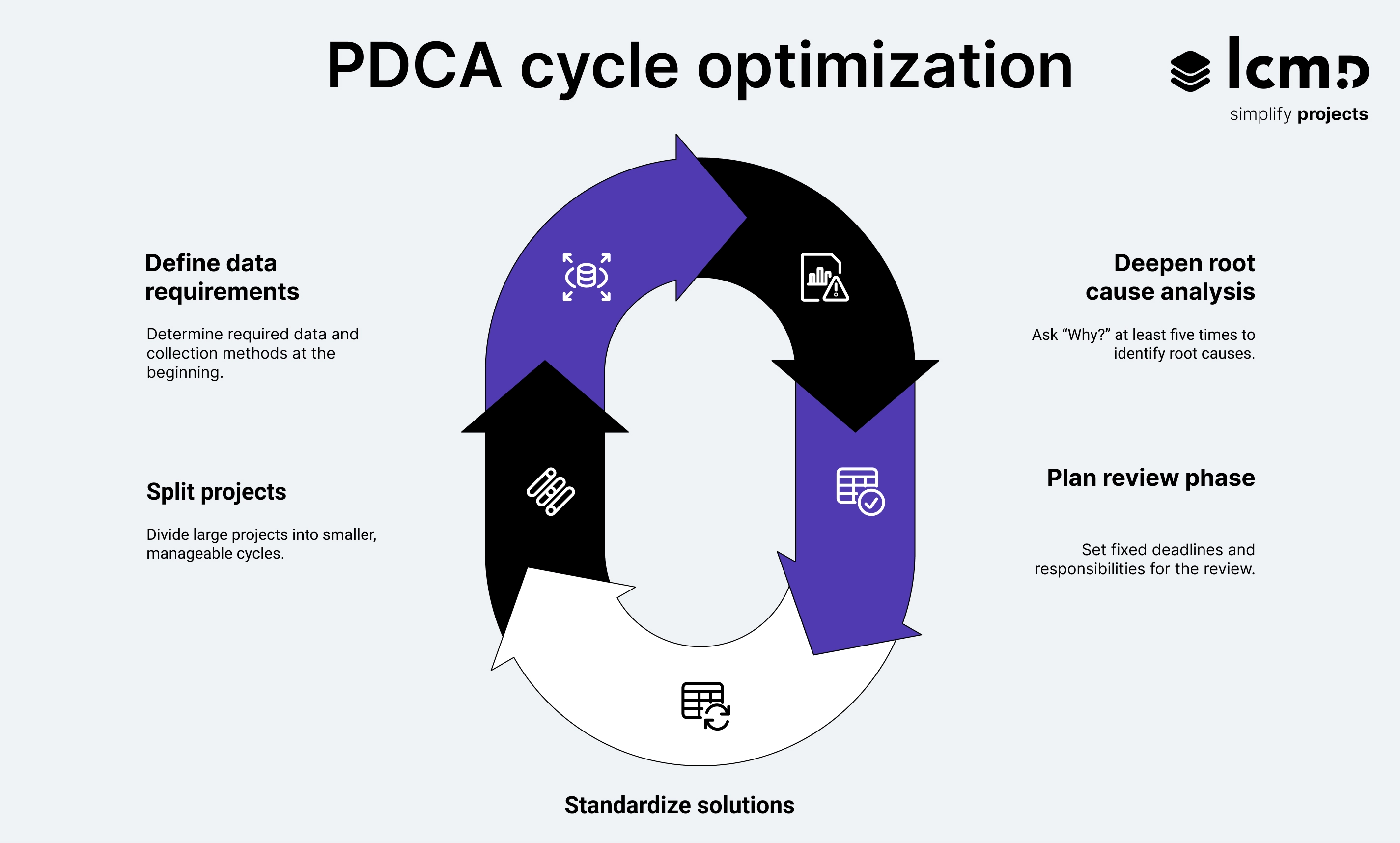
Case Study: PDCA Success in Practice
A medium-sized manufacturing company was struggling with high scrap rates in a production process. Through systematic application of the PDCA cycle, they achieved impressive improvement:
Plan:
- The team defined the problem: 4.2% scrap rate for component X
- Data analysis showed that 80% of defects were due to five main causes
- The team developed specific countermeasures for each cause
Do:
- One production line served as a pilot area
- Operators received training on the new procedures
- Detailed process data was collected over four weeks
Check:
- Data analysis showed that three of the five measures significantly reduced the scrap rate
- Two measures showed no measurable effect
- The overall scrap rate in the pilot line decreased to 1.8%
Act:
- The three effective measures were standardized and implemented in all production lines
- The ineffective measures were discarded
- A new PDCA cycle focused on the remaining causes of defects
Result after six months: The scrap rate decreased company-wide to 1.5%, resulting in annual savings of €875,000.
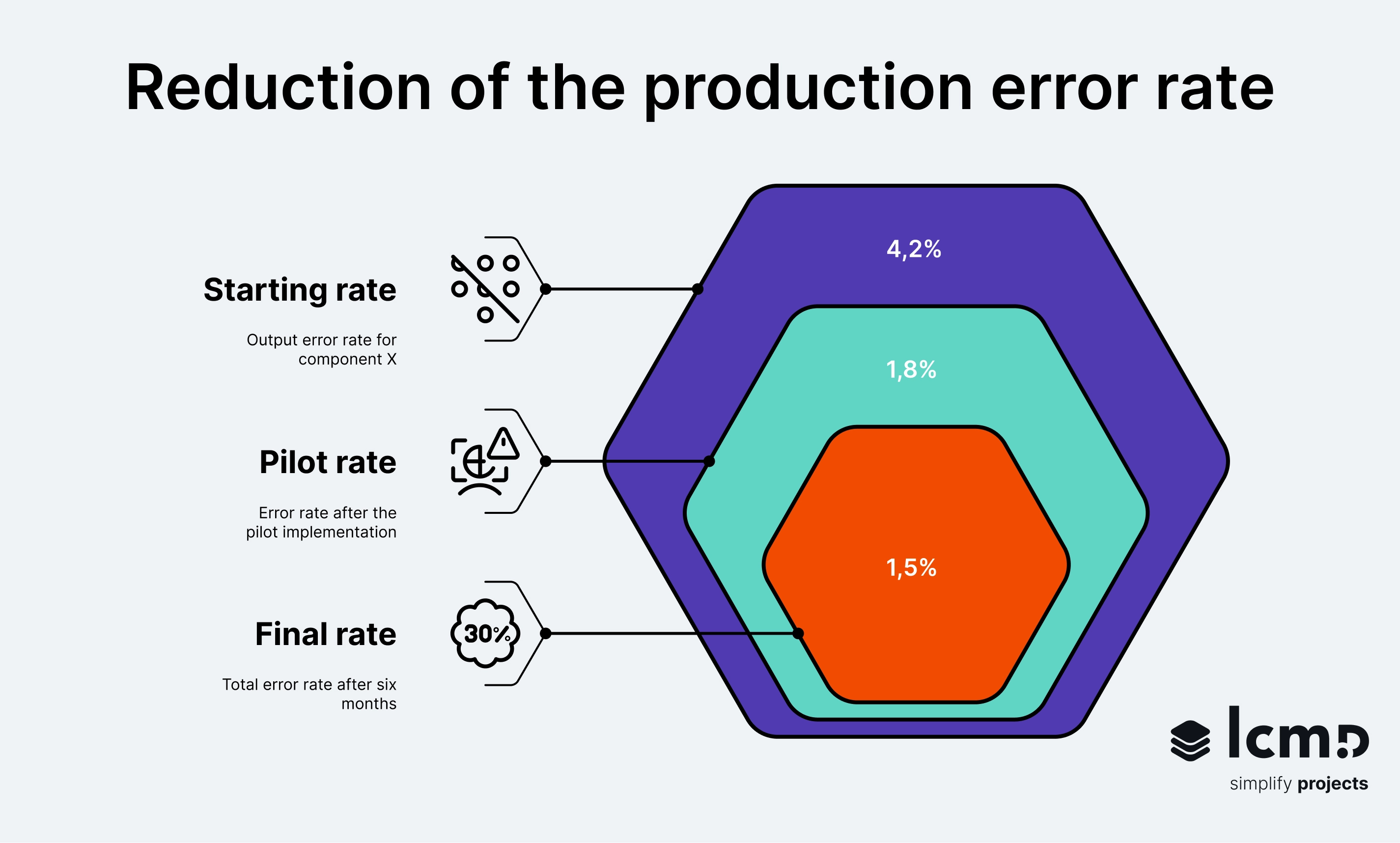
This example shows: PDCA is not a theoretical concept, but a practical tool with measurable benefits.
Practical Tools for Each PDCA Phase
Each phase of the PDCA cycle requires specific methods. Here's a selection of proven tools:
Plan Phase
- Pareto Analysis: Identifies the "vital few" causes
- Ishikawa Diagram: Visualizes cause-effect relationships
- 5-Why Method: Determines root causes through repeated questioning
- SMART Criteria: Ensures precise goal definitions
Do Phase
- Gantt Charts: Visualize timelines and responsibilities
- Standard Work Instructions: Ensure uniform implementation
- Checklists: Guarantee completeness of measures
- Visual Management Boards: Create transparency about progress
Check Phase
- Control Charts: Show process behavior over time
- Before-After Comparisons: Visualize the effectiveness of measures
- KPI Dashboards: Provide overview of relevant metrics
- Process Capability Analyses: Evaluate the stability of the improved process
Act Phase
- A3 Reports: Document the entire PDCA process compactly
- Standardization Forms: Define new standards
- Lessons-Learned Workshops: Secure insights for future cycles
- PDCA Storyboards: Visualize the improvement process
These tools don't all need to be used simultaneously. Select those that fit your specific context and organizational culture.
How Technology Supports the PDCA Cycle
Digital tools can significantly facilitate PDCA application:
- Data Collection and Analysis: Modern BI tools enable deeper insights and faster analyses.
- Project Management Software: Structures implementation and creates transparency about progress.
- Collaboration Platforms: Facilitate cross-team collaboration and documentation.
- Process Mining: Automatically identifies bottlenecks and improvement potential in processes.
- Knowledge Databases: Secure insights from previous PDCA cycles for future projects.
However, technology should support the method, not replace it. The human factor—critical thinking, creativity, and collaboration—remains crucial for success.
{{cta}}
PDCA as Part of Your Management DNA
The true power of the PDCA cycle unfolds when it's understood not as an isolated method, but as a fundamental principle of management. It's about a mindset that considers continuous improvement as a natural part of daily work.
How can you anchor PDCA in your organization?
- Lead by Example: Apply PDCA in your own decision-making processes and communicate this transparently.
- Integration into Meetings: Structure regular meetings according to the PDCA principle.
- Recognition and Appreciation: Acknowledge teams that successfully apply PDCA.
- Qualification: Ensure continuous training in PDCA methods at all levels.
- Visual Management Tools: Make PDCA cycles visible within the company.
The PDCA cycle is not a complicated concept, but its consistent application requires discipline and perseverance. The results—measurable improvements, fact-based decisions, and a culture of continuous optimization—fully justify this commitment.
Conclusion: The First Step to Systematic Improvement
The PDCA cycle offers leaders a proven framework for not only improving processes but continuously optimizing them. It combines the power of systematic analysis with pragmatic implementation and objective evaluation.
Start with a manageable but relevant process in your area of responsibility. Conscientiously go through all four phases of the cycle and document your findings. The visible improvements will pave the way for further PDCA applications.
Remember: Continuous improvement is not a one-time initiative, but an ongoing journey. The PDCA cycle is your compass on this path.