Teile diesen Beitrag:
Die wichtigsten Erkenntnisse aus diesem Artikel:
Effizienz steigern, Prozesse optimieren und pünktlich abliefern – das sind die Grundlagen eines erfolgreichen Unternehmens.
Value Stream Mapping (VSM) ist ein strategisches Werkzeug, das Ihnen dabei hilft, Ordnung ins Chaos zu bringen. Damit können Sie nicht nur Kosten senken und Zeitpläne straffen, sondern auch die Qualität und Effizienz Ihrer Leistungen für Kunden erhöhen.
VSM betrachtet alle Aspekte: die Rohmaterialien, die Prozesse und das Endprodukt.
Wie kann Value Stream Mapping Ihre Abläufe transformieren, um die Wertschöpfung zu maximieren, und wie wird der Mapping-Prozess durchgeführt?
Dieser Artikel führt Sie durch alles, was Sie über VSM wissen müssen. Wir erklären, warum es unerlässlich ist, wie es mit Lean-Prinzipien verbunden ist, um Verschwendung zu reduzieren, und welche Schritte notwendig sind, um selbst eine Wertstromanalyse oder ein Wertstromdesign zu erstellen. Außerdem beleuchten wir praktische Werkzeuge, Herausforderungen und Beispiele, um Ihnen den Einstieg zu erleichtern.
Was genau ist Value Stream Mapping?
Value Stream Mapping ist ein visuelles Werkzeug im Lean Management, das dazu dient, den Fluss von Materialien und Informationen zu analysieren und zu verbessern, die notwendig sind, um ein Produkt oder eine Dienstleistung zum Kunden zu bringen.
Was ist der Hauptzweck von Value Stream Mapping?
Es bietet eine klare, visuelle Darstellung jedes Schritts in Ihrem Prozess. Vom Eintreffen des Rohmaterials bis hin zum fertigen Produkt, das den Kunden erreicht – Value Stream Mapping erfasst alle Schritte.
Dieser Überblick aus der Vogelperspektive ermöglicht es Ihnen, Engpässe zu erkennen. Außerdem decken Sie Ineffizienzen auf und lokalisieren verschiedene Arten von Verschwendung in den unterschiedlichen Prozessen des Projekts.
Durch das Verständnis dieser Elemente ermöglicht Ihnen VSM, einen effizienteren, schlankeren Workflow zu entwerfen, der nicht nur Kosten senkt und Verschwendung eliminiert, sondern auch den den Wert steigert, der an Ihre Kunden geliefert wird. Dies kann zu erheblichen Kostensenkungen und größerer Kundenzufriedenheit führen. Letztendlich hilft VSM dabei, Ihre Abläufe zu transformieren, indem der Fokus auf kontinuierliche Verbesserung und maximale Wertschöpfung gelegt wird.
Schreiten Sie in die Zukunft optimierter Abläufe; Meistern Sie den Value Stream Mapping-Prozess!
Warum sollte Ihr Team Value Stream Mapping nutzen?
Stellen Sie sich vor, Sie gehen über Ihre Baustelle und sehen Stapel von Inventar, die auf Verarbeitung warten, Arbeiter, die sich ineffizient von A nach B bewegen, oder auf Freigabe von Prozessen warten. Dies sind klare Anzeichen von Verschwendung. Jetzt stellen Sie sich vor, Sie könnten diese Ineffizienzen systematisch beseitigen. Hier kann Value Stream Mapping helfen.
Vorteile von Value Stream Mapping in Bauprojekten
Mit Hilfe von Value Stream Mapping kann Ihr Team:
- Den gesamten Prozess visualisieren: Jeden Schritt von Anfang bis Ende sehen.
- Engpässe erkennen und Verschwendung reduzieren: Herausfinden, wo der Prozess stockt oder Ressourcen verschwendet werden.
- Einen effizienteren zukünftigen Zustand entwerfen: Einen Plan für einen schlanken, verschwendungsfreien Prozess erstellen.
- Verbesserungen umsetzen: Konkrete Maßnahmen ergreifen, um den zukünftigen Zustand zu erreichen.
Bedenken Sie: Jeder Schritt in Ihrem Prozess, der keinen Mehrwert bringt, ist im Grunde genommen Verschwendung. Und wie Sie wissen, wird Verschwendung Ressourcen, Zeit und Geld kosten.
Value Stream Mapping zielt darauf ab, Ihre Abläufe zu optimieren, indem es Verschwendung wie ineffiziente Materialhandhabung, die nicht den Kundenanforderungen entspricht, aufdeckt und eliminiert. Dieser Ansatz optimiert nicht nur Wertströme, sondern integriert auch bewährte Methoden zur Steigerung der Gesamtleistung.
Die historischen Wurzeln des Value Stream Mapping
Value Stream Mapping ist kein neues Konzept; seine Wurzeln liegen tief in den Prinzipien der Lean-Produktion.
Es entstand erstmals im Toyota-Produktionssystem, einem von Toyota entwickelten Rahmenwerk, das darauf abzielte, Produktionsprozesse zu optimieren und Verschwendung zu reduzieren. Das System betonte die Schaffung von mehr Wert mit weniger Aufwand – ein Grundsatz, der für das Value Stream Mapping zentral ist.
Durch die gründliche Abbildung jedes einzelnen Schritts im Herstellungsprozess entsprechend den Kundenanforderungen konnte Toyota Ineffizienzen identifizieren und die Abläufe in verschiedenen Geschäftsbereichen optimieren, wodurch ein neuer Standard in der Produktionseffizienz gesetzt wurde.
Entwicklung und Übernahme von Value Stream Mapping in der Lean-Produktion
Warum Value Stream Mapping in der Lean-Produktion weiterhin relevant ist
Warum ist Value Stream Mapping heute noch so wichtig in der Lean-Produktion? Ganz einfach: Die Prinzipien, die bei Toyota ihren Anfang nahmen, haben nicht nur überlebt; sie haben sich weiterentwickelt und etabliert.
Value Stream Mapping durchdringt das Durcheinander und hilft Ihnen, jeden Schritt zu visualisieren, von den Rohmaterialien bis hin zu den fertigen Produkten. Es zeigt Ihnen genau, wo Sie Zeit und Ressourcen im Material- und Informationsfluss verlieren. Die Nutzung einer Wertstromanalyse ist wie eine Lupe, die Ihnen zeigt, wo Sie ansetzen müssen, um die Effizienz und Wirksamkeit zu steigern.
Die weitreichende Wirkung von Value Stream Mapping
Value Stream Mapping beschränkte sich nicht nur auf die Automobilindustrie; es hat sich inzwischen in einer Vielzahl von Branchen etabliert, von Dienstleistungssektoren wie dem Gesundheitswesen, der Softwareentwicklung bis hin zum Bauwesen
Was macht Value Stream Mapping so anpassungsfähig? Es geht um das Kernprinzip: Prozesse schlanker zu gestalten und Verschwendung zu reduzieren. Verschiedene Branchen haben diese Idee aufgegriffen und den Ansatz an ihre spezifischen Herausforderungen angepasst.
Sehen Sie, welche Auswirkungen die Prozessoptimierung haben kann? Kein Wunder, dass Value Stream Mapping zu einer bevorzugten Strategie für jedes Unternehmen geworden ist, das seine Abläufe ernsthaft optimieren möchte.
Softwareentwicklung vereinfacht durch Value Stream Mapping
Kommen wir nun zur Softwareentwicklung – haben Sie eine Vorstellung, wie überwältigend das Management von Prozessdaten sein kann? Hier hilft die Werstromanalyse Unternehmen, sowohl den Material- als auch den Informationsfluss zu optimieren. Besonders in Bereichen, in denen Wissensarbeit stattfindet, wie zum Beispiel in der Softwareentwicklung, sind Wertstromanalysen unverzichtbar.
Sie legen alles offen dar, sodass Sie die Arbeitsabläufe klar erkennen und feststellen können, wo Sie überflüssige Schritte eliminieren können.
Dieser strategische Ansatz kommt nicht nur externen Kunden zugute, sondern dient auch internen Prozessoptimierungen, indem die Servicebereitstellung innerhalb der Organisation verbessert wird.
Value Stream Mapping in agilen Frameworks
Wie sieht es mit der Anwendung von VSM in agilen Umgebungen aus?
Hier dienen Wertstromanalysen als unverzichtbare Werkzeuge, die es den Teammitgliedern ermöglichen, komplexe Aufgaben und Arbeitsabläufe umfassend zu visualisieren. Diese Visualisierung erleichtert es den Teams, sich schnell an Veränderungen anzupassen und weiterzuentwickeln. Dies ist ein Kernprinzip aller agilen Methoden.
Egal, ob Sie Scaled Agile Framework (SAFe) oder eine andere agile Methode verwenden, die Integration von VSM stellt sicher, dass alle Prozesse – von Entwicklungszyklen bis hin zur Logistik in der Lieferkette – für maximale Schlankheit optimiert sind, was kontinuierliche Verbesserung und schnelle Anpassung an neue Herausforderungen ermöglicht.
Zentrale Konzepte des Value Stream Mapping
Integration von Material- und Informationsfluss in der Wertstromanalyse
In der Wertstromanalyse werden sowohl der Material- als auch der Informationsfluss abgebildet, um einen umfassenden Überblick über den gesamten Prozess zu erhalten. Dies hilft dabei, Bereiche zu identifizieren, in denen Materialien verzögert oder falsch verwaltet werden, und zu erkennen, wo Informationen unvollständig, ungenau oder langsam weitergeleitet werden.
Materialfluss-Mapping
Materialfluss bezieht sich auf die Bewegung physischer Gegenstände durch die verschiedenen Phasen eines Produktionsprozesses. Dazu gehören der Transport von Rohmaterialien, Halbfabrikaten (WIP) und Fertigwaren. Im Wertstromdesign wird der Materialfluss dargestellt, um zu zeigen, wie Produkte durch den Herstellungs- oder Dienstleistungsprozess vom Anfang bis zum Ende bewegt werden. Das Ziel ist es, Engpässe zu identifizieren und zu beseitigen, Wartezeiten zu reduzieren und den physischen Warenfluss zu straffen, um die Effizienz zu steigern.
Schlüsselelemente des Materialflusses
- Rohmaterialien: Die anfänglichen Eingaben, die für den Produktionsprozess erforderlich sind.
- Work-in-Progress (WIP): Gegenstände, die derzeit verarbeitet oder montiert werden.
- Fertigwaren: Fertiggestellte Produkte, die zur Lieferung an den Kunden bereitstehen.
- Transport: Die Bewegung dieser Materialien zwischen den verschiedenen Phasen des Prozesses.
- Lagerung: Bereiche, in denen Materialien als Rohmaterial, WIP oder Fertigwaren gelagert werden.
Informationsfluss
Der Informationsfluss bezieht sich auf die Bewegung von Daten und Informationen, die zur Unterstützung und Steuerung des Produktionsprozesses erforderlich sind. Dazu gehören Anweisungen, Zeitpläne, Aufträge und Feedback, die angeben, wie Materialien verarbeitet werden sollen. In der Wertstromanalyse wird der Informationsfluss abgebildet, um zu verstehen, wie Daten durch die Organisation fließen und um Ineffizienzen, Verzögerungen oder Kommunikationslücken zu identifizieren.
Schlüsselelemente des Informationsflusses
- Produktionsaufträge: Anweisungen, die festlegen, was produziert werden soll, in welcher Menge und bis wann.
- Zeitpläne: Zeitliche Abläufe und Pläne, die das Timing der verschiedenen Phasen im Prozess koordinieren.
- Kommunikation: Informationsaustausch zwischen Abteilungen, Teams oder Einzelpersonen, die am Produktionsprozess beteiligt sind.
- Feedback-Schleifen: Informationen, die aus dem Prozess zurückfließen, wie Qualitätsprüfungen, Leistungsdaten und Kundenfeedback, die zur Anpassung und Verbesserung genutzt werden.
- Datensysteme: Werkzeuge und Plattformen, die zur Verwaltung und Übertragung von Informationen verwendet werden, wie ERP-Systeme, Tabellenkalkulationen oder spezialisierte Software.
Es gibt im Allgemeinen drei Haupttypen von Wertstromanalysen, die jeweils einem anderen Zweck dienen:
- Ist-Zustands-Diagramm
- Soll-Zustands-Diagramm
- Idealzustands-Diagramm
1. Ist-Zustands-Diagramm
Das Ist-Zustands-Diagramm wird verwendet, um den bestehenden Prozess so darzustellen, wie er derzeit abläuft. Dies umfasst alle Schritte, Materialien und Informationsflüsse, die an der Lieferung eines Produkts oder einer Dienstleistung an den Kunden beteiligt sind.
Anwendung: Dieses Diagramm hilft dabei, Engpässe, Verschwendung und Verbesserungsmöglichkeiten zu identifizieren, indem es ein klares Bild des aktuellen Betriebszustands liefert.
2. Soll-Zustands-Diagramm
Das Soll-Zustands-Diagramm skizziert den optimierten Prozess nach erfolgten Verbesserungen. Dieses Diagramm zielt darauf ab, Verschwendung zu eliminieren und die Abläufe zu verschlanken, um die Effizienz und Wertschöpfung zu steigern.
Anwendung: Dieses Diagramm wird verwendet, um die notwendigen Änderungen zu planen und zu visualisieren, um einen effizienteren und effektiveren Prozess zu erreichen. Es dient als Fahrplan für die Umsetzung der in der Ist-Zustands-Analyse identifizierten Verbesserungen.
3. Idealzustands-Diagramm
Das Idealzustands-Diagramm stellt die ultimative Vision des perfekten Prozesses ohne jegliche Einschränkungen dar. Es zeigt das bestmögliche Szenario mit maximaler Effizienz und null Verschwendung.
Anwendung: Dieses Diagramm dient als langfristiges Ziel oder Vision für die Organisation. Auch wenn es möglicherweise nicht sofort erreichbar ist, bietet es eine Richtung und eine Inspiration für kontinuierliche Verbesserungsbemühungen.
Wesentliche Elemente für eine effektive Wertstromanalyse
- Wertstromanalyse: Entscheidend, um jeden Schritt zu zerlegen und sicherzustellen, dass er einen Mehrwert schafft.
- Kaizen-Events: Kurzzeitprojekte, die schnelle, schrittweise Veränderungen umsetzen, um den Idealzustand zu erreichen.
- Lean-Techniken: Lean-Methoden, Werkzeuge und Strategien, die die kontinuierliche Verbesserung von Prozessen unterstützen.
So starten Sie den Value Stream Mapping-Prozess
Die Optimierung Ihrer Abläufe beginnt mit einem soliden Plan.
Eine effektive Wertstromanalyse zu erstellen, erfordert eine Reihe klar definierter Schritte, die jeweils unerlässlich sind, um Verschwendung zu beseitigen und Verbesserungsmöglichkeiten in Ihren Abläufen zu identifizieren.
Doch bevor wir uns den Schritt-für-Schritt-Anweisungen widmen, lassen Sie uns klären, was in Ihrem Prozess wirklich zählt:
- Wertschöpfende Schritte: Dies sind die Aktionen, für die Ihre Kunden tatsächlich bezahlen, die direkt zum Produkt oder zur Dienstleistung beitragen.
- Nicht-wertschöpfende Schritte (Verschwendung): Diese Schritte verbrauchen Ressourcen, fügen jedoch aus Sicht des Kunden keinen Wert hinzu.
Und so gehen Sie vor, um eine Wertstromanalyse zu erstellen:
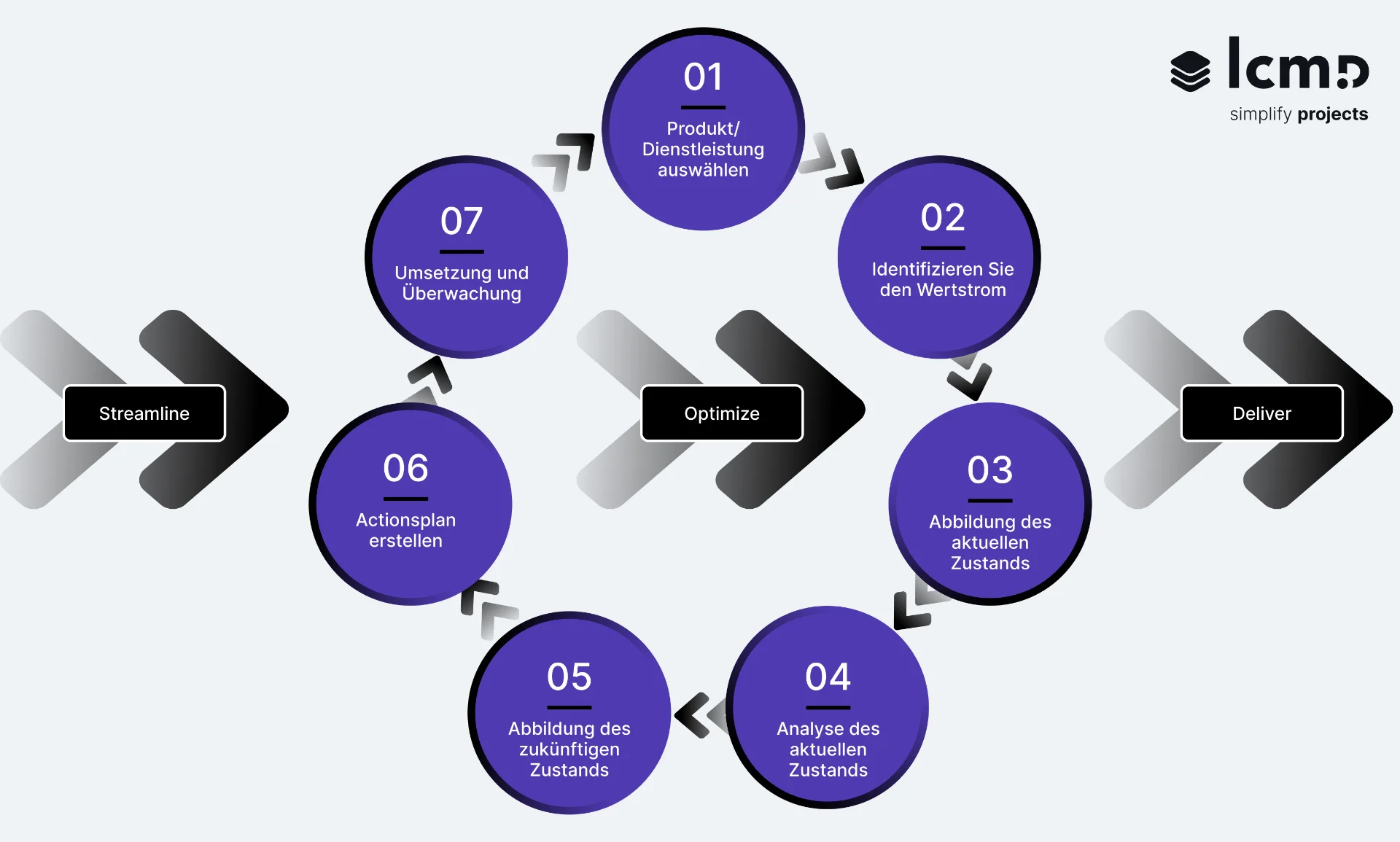
1. Auswahl der Produkt- oder Dienstleistungsfamilie
Beginnen Sie damit, den Umfang des Prozesses oder der Produktfamilie zu definieren. Dieser erste Schritt hilft, die Analysebemühungen zu fokussieren, und legt den Grundstein für eine detaillierte Analyse zur Erfassung von Prozessdaten.
2. Identifikation des Wertstroms
Identifizieren und dokumentieren Sie den vollständigen Fluss von Materialien und Informationen durch den Prozess. Dazu gehört die Verwendung standardisierter Symbole innerhalb eines Informationsflussdiagramms, um verschiedene Prozessschritte und Flüsse klar darzustellen.
3. Abbildung des Ist-Zustands
- Beobachten Sie den Prozess
- Verfolgen Sie den Materialfluss und den Informationsfluss durch den Prozess und dokumentieren Sie jeden Prozessschritt, um eine gründliche Wertstromanalyse sicherzustellen.
- Verwenden Sie gängige Symbole
- Nutzen Sie standardisierte Symbole, um verschiedene Prozessschritte und Flüsse innerhalb eines Informationsflussdiagramms darzustellen.
- Identifizieren Sie Lean-Verschwendung
- In dieser Phase identifizieren Sie alle 8 Arten von Verschwendung. Das Mapping des Informationsflusses kann hier besonders nützlich sein, um nachzuvollziehen, wie Daten durch das System fließen, was für die Ziele der Wertstromanalyse entscheidend ist.
- Beseitigen Sie Lean-Verschwendung
- Entwickeln Sie Strategien zur Reduzierung oder Beseitigung identifizierter Verschwendungen, indem Sie Mapping-Techniken anwenden, um jeden Prozessschritt zu verfeinern und zu optimieren.
4. Analyse des Ist-Zustands
Analysieren Sie die Ist-Zustands-Darstellung, um Ineffizienzen und Bereiche zu erkennen, die Änderungen oder Verbesserungen erfordern. Achten Sie besonders auf Zykluszeit, Durchlaufzeit und Wartezeit.
- Zykluszeit ist die gesamte Zeit, die benötigt wird, um einen bestimmten Prozess oder eine Aufgabe von Anfang bis Ende abzuschließen. Dazu gehört die tatsächliche Arbeitszeit, aber nicht die Wartezeiten.
- Durchlaufzeit ist die Gesamtzeit, die vom Start eines Prozesses bis zu dessen Abschluss benötigt wird. Dies umfasst sowohl die Zykluszeit als auch alle Wartezeiten und deckt die gesamte Dauer von der Bestellung bis zur Lieferung ab.
- Wartezeit ist die Zeit, die ein Produkt oder Material zwischen den Prozessschritten wartet. Dies wird als nicht-wertschöpfende Zeit betrachtet und ist ein Schlüsselfaktor zur Identifizierung und Reduzierung von Ineffizienzen.
5. Erstellen der Soll-Zustands-Darstellung
Entwerfen Sie die Soll-Zustands-Darstellung, um einen effizienteren Prozess mit verbessertem Material- und Informationsfluss darzustellen, und stellen Sie sicher, dass alle identifizierten Verbesserungen klar abgebildet sind.
6. Entwicklung eines Aktionsplans
Dieser letzte Schritt umfasst die Erstellung eines detaillierten Plans, um die gewünschten Prozessverbesserungen zu erreichen, einschließlich Zeitplänen, Ressourcen und spezifischen Maßnahmen, die umgesetzt werden sollen. Dieser Plan dient als Blaupause für eine kontinuierliche Lieferung.
7. Implementierung und Überwachung
Setzen Sie schließlich den Aktionsplan um und überwachen Sie den Prozess kontinuierlich. Nutzen Sie das Feedback, um Anpassungen vorzunehmen und die Wertstromanalyse weiterzuentwickeln, um die Abläufe noch weiter zu verfeinern und zu optimieren.
Werkzeuge und Symbole in der Wertstromanalyse
Werkzeuge und Software für einen optimierten Wertstromanalyse-Prozess
Wenn Sie in die Wertstromanalyse eintauchen, können die richtigen Werkzeuge den entscheidenden Unterschied machen. Welche sollten Sie also verwenden?
Erstellung der Wertstromanalyse
- Diagrammsoftware (z. B. Microsoft Visio, Lucidchart): Diese visuellen Werkzeuge bieten robuste Funktionen zum Erstellen genauer Diagramme mit Vorlagen, Symbolen und Features, die den VSM-Standards entsprechen. Sie erleichtern es, Prozessschritte und -abläufe zu visualisieren.
- Whiteboards und Marker: Unverzichtbar in kollaborativen Umgebungen wie Workshops, da sie es den Teams ermöglichen, dynamisch Ideen beizusteuern und während der Mapping-Phase in Echtzeit Anpassungen vorzunehmen.
Datenerfassung und Stream-Analyse
- Excel und Minitab: Diese Werkzeuge werden verwendet, um Prozessdaten zu sammeln und zu analysieren, was bei der Entscheidungsfindung unterstützt und komplexe statistische Analysen im Zusammenhang mit dem Produktionsvolumen ermöglicht.
- Wertstromanalyse-Software: Diese Software geht über die traditionelle Diagrammerstellung hinaus, indem sie Datenanalysen direkt in die Sream Analyse integriert und automatisierte Einblicke für die Stream-Analyse und Prozessverbesserung bietet.
Kommunikation und Zusammenarbeit
- Online-Kollaborationstools (z. B. Lucidchart, Google Workspace): Diese Tools erleichtern das nahtlose Teilen und die Zusammenarbeit an VSM-Projekten, sodass alle Teammitglieder, unabhängig vom Standort, auf dem neuesten Stand bleiben.
- Lean-Management-Software: Diese Tools integrieren verschiedene Funktionen, die für eine effektive Kommunikation und Zusammenarbeit unerlässlich sind. Sie bieten zentrale Kommunikation, Workflow-Automatisierung und Dokumentenkontrolle, um sicherzustellen, dass alle mit den neuesten Informationen arbeiten. Diese Software bietet auch Funktionen zur Projektverfolgung und Berichterstattung, die den Teams helfen, den Fortschritt zu messen und Pläne bei Bedarf anzupassen. Dabei sind alle Funktionen darauf ausgelegt, die Prinzipien des Lean Managements konsequent zu unterstützen.
- Präsentationstools (z. B. PowerPoint): Nützlich zur Formalisierung und Präsentation der Ergebnisse aus der Wertstromanalyse für Stakeholder in einem klaren und strukturierten Format, oft unter Verwendung von Informationsflussdiagrammen.
Kontinuierliche Verbesserung und Überwachung
- Prozessüberwachungstools: Fortschrittliche Funktionen in einigen Wertstromanalyse-Tools ermöglichen die kontinuierliche Verfolgung von Verbesserungen und Benachrichtigungen bei Abweichungen, was rechtzeitige Korrekturmaßnahmen fördert.
Symbole der Wertstromanalyse
Während Werkzeuge die Erstellung einer Wertstromanalyse erleichtern, werden Symbole strategisch innerhalb dieser Diagramme platziert, um spezifische Elemente des Herstellungs- oder Dienstleistungsprozesses darzustellen.
Im Allgemeinen werden die Symbole der Wertstromanalyse nach ihrer Funktion innerhalb des Diagramms in Gruppen unterteilt. Diese Gruppen sind weithin anerkannt, und ihre standardisierte Natur hilft, Konsistenz und Verständnis zwischen verschiedenen Teams oder sogar externen Stakeholdern zu gewährleisten, die mit den Praktiken der Wertstromanalyse vertraut sind.
Symbolkategorien in der Wertstromanalyse
Die Symbole der Wertstromanalyse werden typischerweise in die folgenden Kategorien unterteilt:
- Prozesssymbole
- Materialsymbole
- Informationssymbole
- Allgemeine Symbole
- Kaizen-Burst-Symbole
Integration von Six Sigma in die fortgeschrittene Wertstromanalyse
Wie passt Six Sigma in dieses Bild?
Wertstromanalysen können als visuelle Ergänzung zum rigorosen, datengetriebenen Ansatz von Six Sigma gesehen werden. Die Kombination beider Methoden bedeutet, Probleme zu identifizieren und sie mit Präzision zu lösen.
Wichtige Integrationen
- Datenfelder und Prozessschritte
Six Sigmas Fokus auf Datenfelder zur Erfassung von Kennzahlen wie Zykluszeit, Durchlaufzeit und Wartezeit bei jedem Prozessschritt bereichert das visuelle Layout der Wertstromanalyse.
- Linienoptimierung
Durch die Ausrichtung der Six Sigma-Tools auf die Wertstromanalyse können Linienarbeiter und Teammitglieder Ineffizienzen erheblich reduzieren, was direkt die Linienverbesserung und die kontinuierliche Lieferung verbessert.
- Von der Visualisierung zur Umsetzung
Die Integration erleichtert einen robusten Umsetzungsplan, der Qualitätsverbesserungen über die Produktionsstufen hinweg abbildet und umsetzt, sodass jeder Prozessschritt effektiv zum Endprodukt beiträgt.
Doppelte Vorteile
- Fehlerminimierung und Qualitätsmaximierung
Die Verbindung dieser Methoden stellt sicher, dass Fehler minimiert und die Qualität über die Prozessschritte hinweg maximiert wird – entscheidend, um die Kundennachfrage zu erfüllen.
- Effizientes Ressourcenmanagement
Dieser strategische Ansatz optimiert die Ressourcenzuweisung und -nutzung, was sich erheblich auf die Produktionszeitpläne und die Kundenzufriedenheit auswirkt.
Fazit
Ein Wertstromanalyse-Diagramm ist wie der Bauplan Ihrer Geschäftsprozesse. Es zeigt, wie Materialien und Informationen vom Anfang bis zum Ende fließen.
Es identifiziert die Schwachstellen in Ihrem System und beleuchtet genau, wo Ihr Prozess optimiert werden kann. Wertstromanalysen geben Ihnen einen klaren Überblick über Ineffizienzen und leiten Sie an, wie Sie einen optimierten zukünftigen Zustand erreichen können.
Eine Wertstromanalyse hilft Ihrem Team, Engpässe visuell zu identifizieren und Prozesse zu verschlanken, was letztlich die kontinuierliche Lieferung verbessert. Sie zeigt auch, wie jeder Schritt zur Schaffung von Kundenwert beiträgt und stellt sicher, dass jeder Teil des Workflows auf das Ziel ausgerichtet ist, Kundenzufriedenheit zu schaffen.
Effektiv, effizient und anpassungsfähig – sind das nicht die Kennzeichen eines leistungsstarken Teams?
{{cta}}
Bereit, den Ansatz Ihres Teams für Herausforderungen zu revolutionieren und die Effizienz zu steigern? Tauchen Sie in die Wertstromanalyse ein, um Ihre Abläufe zu optimieren. Starten Sie jetzt – steigern Sie gleichzeitig die Leistung und die Kundenzufriedenheit! Lassen Sie sich von der Wertstromanalyse leiten, um Ihre Ziele zu übertreffen.