Share this article:
Key Takeaways from this article
Improvement usually means doing something that we have never done before. It requires a conscious effort and Kaizen fosters this by encouraging daily, small improvements.
Shigeo Shingo
How Kaizen Transforms Operations Through Continuous Improvement
Kaizen, a Japanese term meaning "continuous improvement," is a philosophy and a method that focuses on making small, incremental changes to improve processes, enhance productivity, and reduce waste.
While it began in manufacturing, particularly within the Toyota Production System, Kaizen has since been adopted across various industries. Below, we explore several real-world examples of Kaizen in action to demonstrate its versatility and effectiveness.
Kaizen in Manufacturing
Toyota's Continuous Improvement with Kaizen Teian
The Toyota Production System (TPS) is perhaps the most famous example of Kaizen in practice. Toyota adopted Kaizen as a core principle in the 1950s, revolutionizing the automotive industry. Through continuous improvement, Toyota was able to significantly reduce waste, optimize assembly line processes, and elevate product quality.
In practice, Toyota implemented Kaizen by encouraging all employees, from assembly line workers to managers, to suggest improvements. These suggestions, known as Kaizen Teian, led to countless small changes that collectively transformed Toyota’s operations. For example, workers suggested redesigning certain tools to reduce time spent on specific tasks, leading to a smoother production process and higher efficiency.
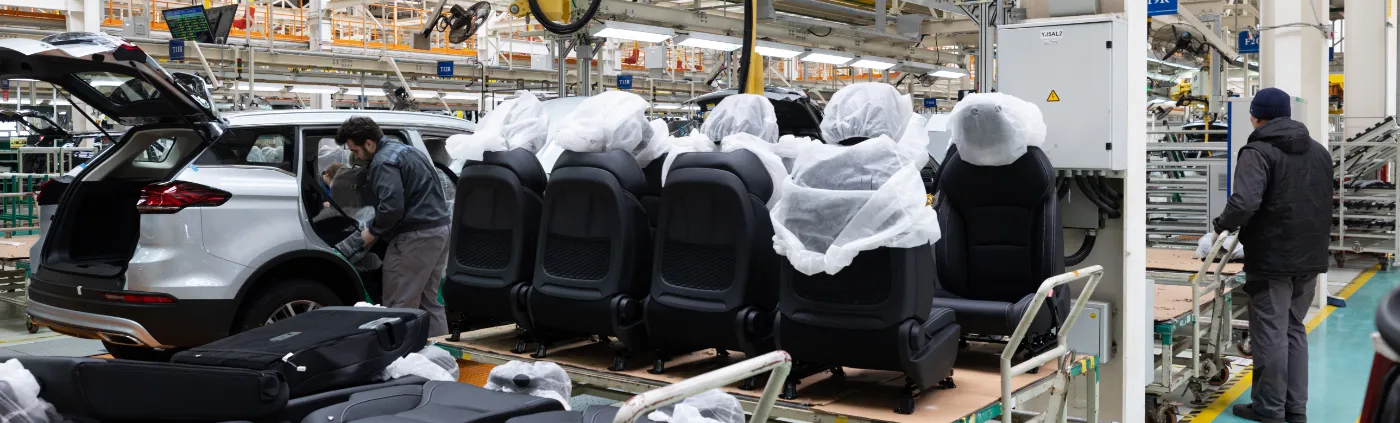
Canon's Market Response Revolution Through Kaizen Implementation
Canon, the well-known electronics and imaging company, applied Kaizen principles to its manufacturing processes to maintain a competitive edge. By focusing on lean manufacturing, Canon continuously identified inefficiencies and sought to eliminate them. This approach led to a more refined production process, reduced inventory levels, and a quicker response to market demands.
Canon’s use of Kaizen was particularly evident in its “Visual Management” strategy, where production data was made visible to all employees. This transparency allowed workers to immediately identify when something was off and take corrective action, leading to fewer defects and higher overall quality.
Kaizen in Healthcare
Kaizen Redefines Medical Excellence at Virginia Mason
Virginia Mason Medical Center in Seattle, Washington, is a pioneer in applying Kaizen to healthcare. The hospital adopted Kaizen principles to improve patient care and reduce errors. By continuously refining processes, Virginia Mason significantly reduced the time patients spent waiting for care, minimized medical errors, and improved overall patient satisfaction.
One notable example was the hospital’s initiative to optimize the process of administering medications. By involving nurses, pharmacists, and doctors in Kaizen events, the hospital reduced the time it took to get medications to patients, which directly improved patient outcomes and safety.
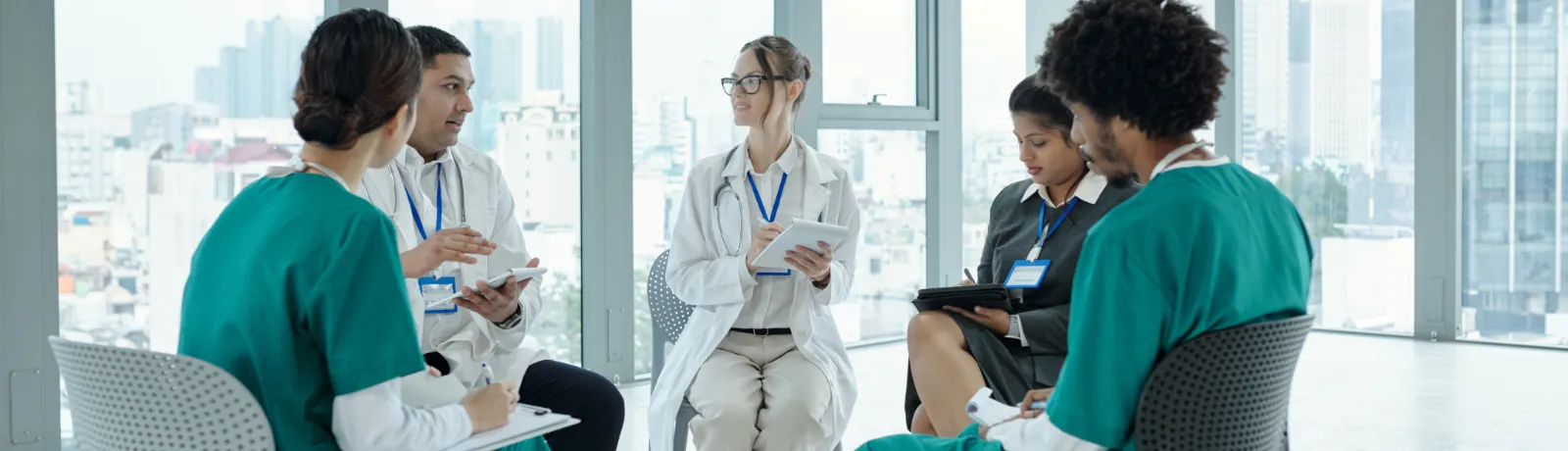
Kaizen in Office Settings
Kaizen Innovations in Ford’s Office Workflows
While Ford is traditionally known for its manufacturing, it also applied Kaizen principles to its office environments. By analyzing workflow and administrative processes, Ford identified numerous opportunities for improvement. For instance, the company restructured its document handling system to reduce the time employees spent searching for information, thereby boosting productivity.
Ford also focused on reducing unnecessary meetings, simplifying communication channels, and automating routine tasks. These changes, although small individually, collectively led to a more efficient and productive office environment, showcasing the flexibility of Kaizen beyond the factory floor.
Kaizen in Retail
Tesco’s Continuous Improvement
Tesco, one of the world’s largest retailers, utilized Kaizen to increase its operational efficiency and customer service. The company implemented a system where employees at all levels could suggest improvements, from store layout changes to checkout process optimizations.
For example, by analyzing customer flow and checkout wait times, Tesco was able to rearrange store layouts and add self-checkout stations where needed. These changes led to reduced wait times, higher customer satisfaction, and ultimately, increased sales.
Kaizen in Software Development
Atlassian’s Innovation Weeks
Atlassian, a global software company known for products like Jira and Confluence, integrates Kaizen into its development process through “Innovation Weeks.” During these weeks, employees are encouraged to work on any project or improvement idea they believe will benefit the company.
This Kaizen approach has led to numerous enhancements in Atlassian’s products and internal processes. For instance, teams have developed new features, improved software performance, and streamlined development workflows—all of which have contributed to better product quality and customer satisfaction.
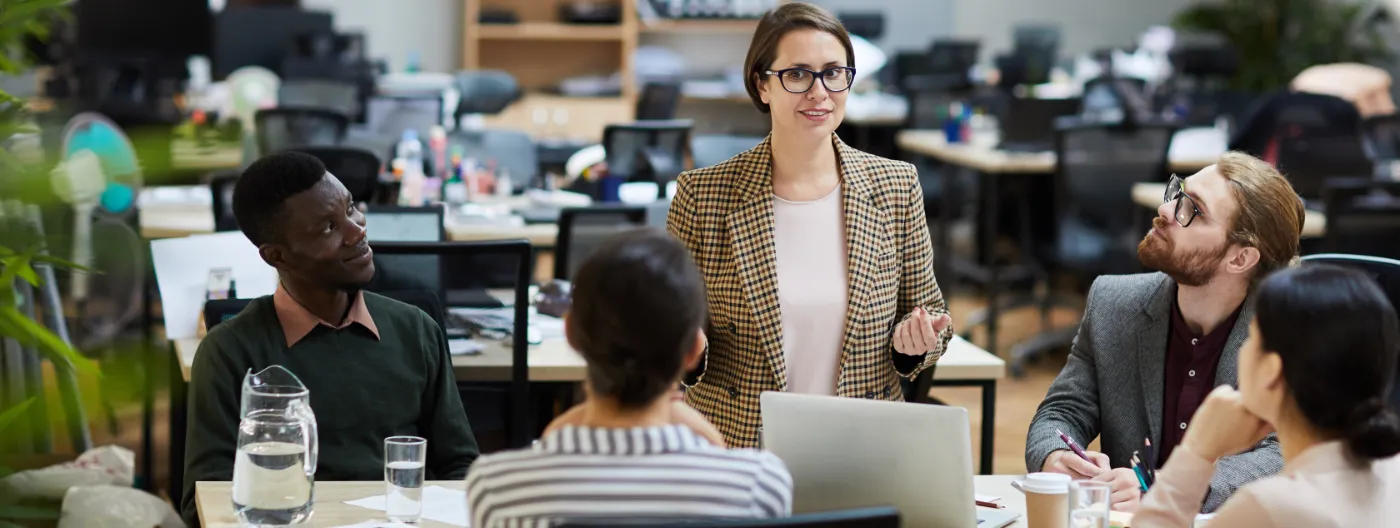
Kaizen in Construction
Boldt Construction’s Continuous Improvement with OneBoldt
Boldt Construction is a recognized leader in applying Kaizen to the construction industry. Their approach, branded as "OneBoldt," emphasizes continuous improvement through shared learning and collaboration across all projects. By encouraging project teams to share insights and experiences, Boldt consistently optimises project delivery, becoming better, faster, and safer with each completed project.
During construction projects, Boldt Construction effectively utilizes Kaizen principles to improve operations. By focusing on improving the flow of materials, reducing waste, and enhancing team communication, they continuously address inefficiencies as they arise. Regular Kaizen events enable teams to quickly identify and implement real-time solutions, leading to significant improvements in both project timelines and cost efficiency.
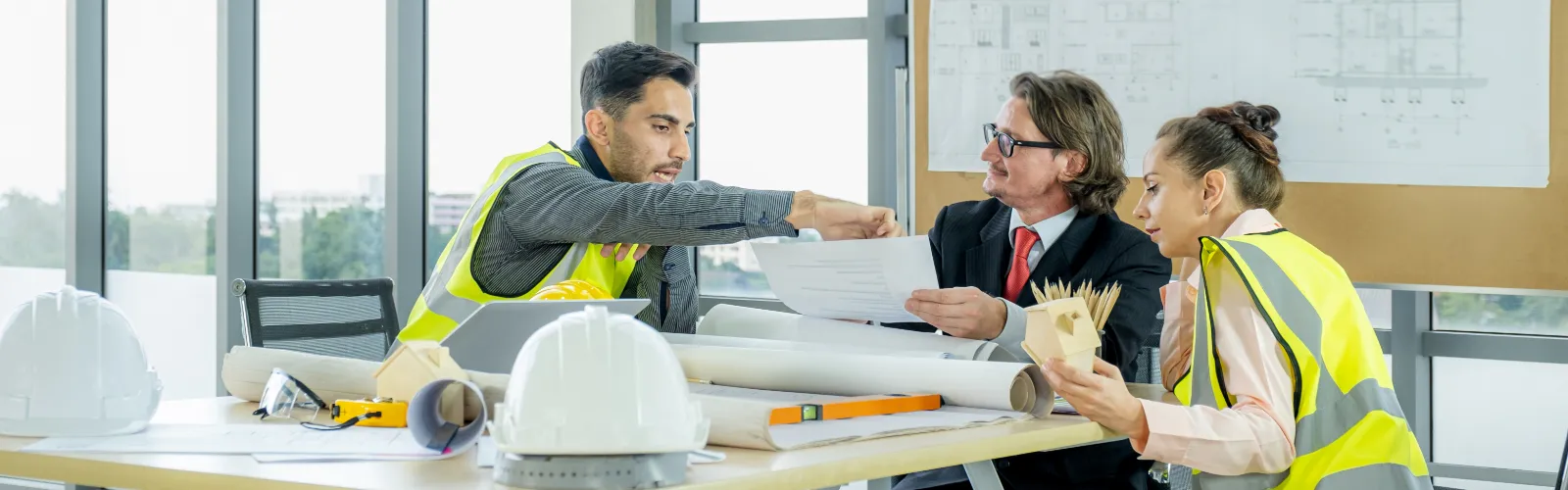
Lcmd: Digital Kaizen Implementation in Lean Construction
Lcmd revolutionizes the application of Kaizen in the construction industry through digital tools. It enables real-time feedback, proactive problem-solving, and process optimization. With Lcmd, construction teams can effectively implement Kaizen principles by driving continuous improvements, reducing waste, and promoting employee engagement. This digital solution makes Kaizen more accessible and effective by allowing immediate identification and resolution of issues, thus significantly increasing efficiency in construction projects.
{{cta}}
Conclusion
Kaizen is not confined to any single industry or type of work. From manufacturing and healthcare to office environments and construction industry, the philosophy of continuous improvement drives organizations to become more efficient, responsive, and innovative.
By focusing on small, incremental changes, Kaizen empowers employees at all levels to contribute to the success of the organization, making it a powerful tool for any business committed to excellence.